The work of the West Haven Wastewater Pollution Control Facility is vital to the city of West Haven, Connecticut, a seacoast community with a view of Long Island Sound featuring beaches and a boardwalk. It services approximately 55,000 residences in West Haven and a portion of the neighboring town of Orange. After a decade-long relationship with an independent municipal wastewater management firm, the city of West Haven resumed operation of its 12.5 million gallons per day (mgd) water pollution control plant (WPCP). The WPCP team immediately began to review their current processes to recognize target areas for improvement. The goal was focused on identifying ways to increase equipment reliability, general efficiencies and promoting operator safety while trying to reduce operational costs and the environmental impact to New Haven Harbor. Some of the processes targeted were in the plant’s three polymer activation systems.
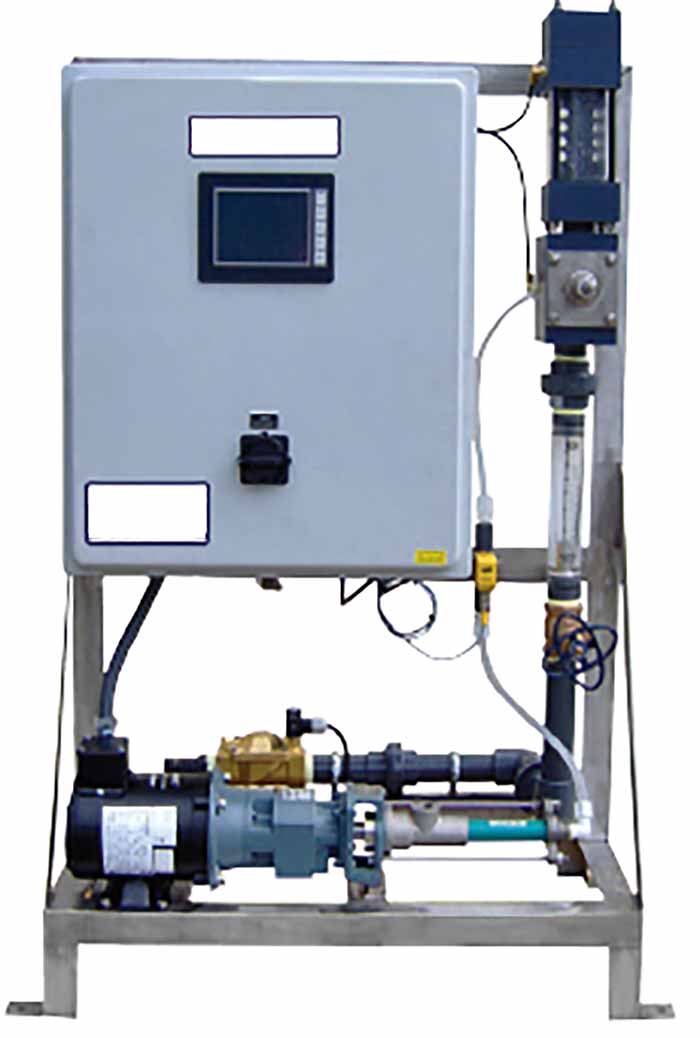
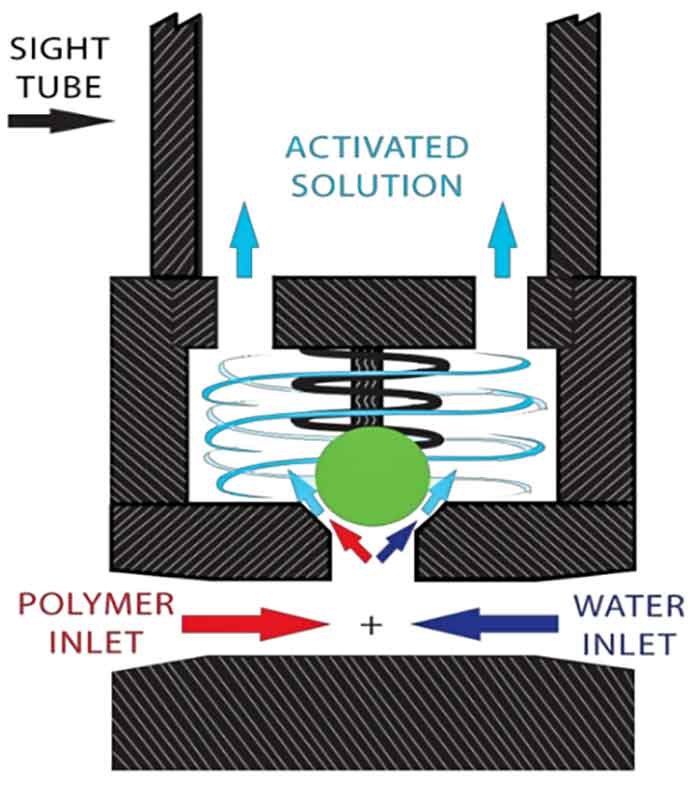
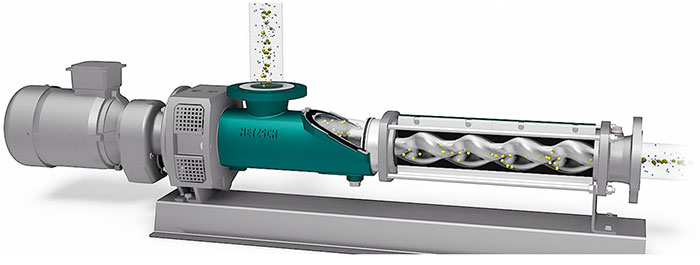