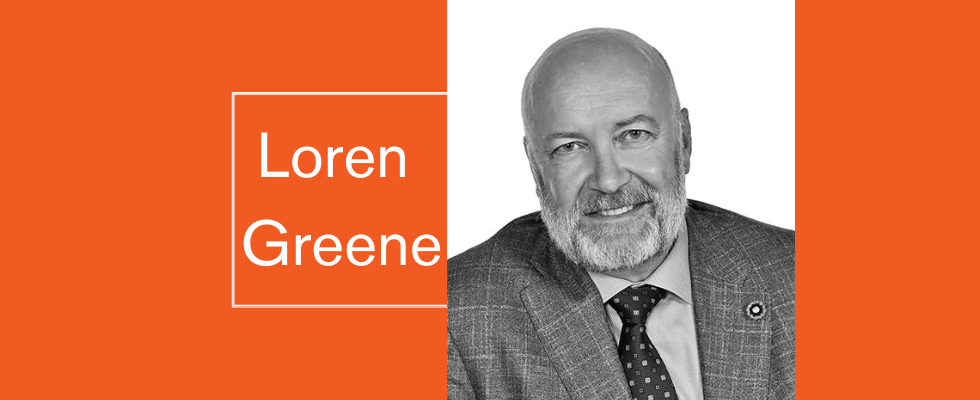
Sanitary pumps are vital components in industries where hygiene and contamination prevention are critical. Primarily used in the food, beverage, pharmaceutical and biotechnology sectors, these pumps facilitate the transfer of fluids while adhering to strict sanitary standards. They are designed to handle liquids, semi-liquids and suspensions, accommodating a wide range of fluid viscosities and heads, potentially anything from water to peanut butter.
The head refers to the maximum height a pump can raise a fluid against the force of gravity and serves as a measure of the pump’s power. Essentially, the more pressure a pump can generate, the greater the fluid head it can achieve.
The choice of design, application, lubrication and maintenance methods significantly impacts the efficiency and effectiveness of sanitary pumps. Key considerations when selecting a pump include the expected flow rate, pressure range, power source, physical size and construction materials. Many of these applications require variable frequency drives (VFDs), which enhance efficiency. When combined with programmable logic controllers (PLCs), they provide extremely precise control over fluid flow.
Design of Sanitary Pumps
The design of sanitary pumps is crucial for ensuring that equipment used in sensitive industries, such as food, beverage, pharmaceuticals and biotechnology, adheres to the regulations set by organizations such as the Food and Drug Administration (FDA) and the European Hygienic Engineering & Design Group (EHEDG). These guidelines require the elimination of crevices and dead zones where bacteria could proliferate.
The material composition of sanitary pumps is a fundamental design consideration. The primary materials used are stainless steels, specifically grades 304 and 316L. While grade 304 stainless steel is generally less resistant to corrosion than 316L, it remains highly durable and suitable for many applications where contact with salty or highly acidic substances is unlikely. Grade 316L stainless steel is preferred in environments with corrosive fluids or in processes requiring high-level disinfection and sterilization.
The addition of molybdenum in 316L enhances its resistance to pitting corrosion, making it better suited for handling chlorides and other aggressive substances. Stainless steel enables smooth surfaces with minimal roughness, which is crucial for preventing bacterial adhesion and facilitating easy cleaning.
Surface finish is a critical aspect of sanitary pump design. The surface roughness, typically denoted as Ra (roughness average), should generally be less than 0.8 micrometers. Ensuring that the internal surfaces are smoothly polished aids in reducing crevices where bacteria could thrive. Electropolishing is a common technique used to eliminate microscopic high points, further reducing surface roughness. Additionally, electropolishing improves the cleanability and passive layer of stainless steel, providing an extra layer of corrosion resistance.
Sanitary Pump Hygiene
The design of sanitary pumps incorporates various hygienic features that facilitate easy disassembly and thorough cleaning. Tri-clamp fittings allow for rapid disassembly without requiring tools, thus reducing cleaning and maintenance. Designs that will enable pumps to be completely drained of all fluids minimize the risk of microbial growth and contamination between uses. Nontoxic, food-grade elastomers such as ethylene propylene diene monomer rubber (EPDM), polytetrafluoroethylene (PTFE), Viton and silicone are used for seals and gaskets. These materials can withstand high sterilization temperatures and aggressive cleaning agents, maintaining their integrity over time without releasing harmful substances into the pump system.
A key component of sanitary pump design is tight control over clearances and tolerances. Components must be manufactured to precision specifications to prevent stagnant areas. Close tolerances ensure maximum efficiency while pumping and also minimize vibration and mechanical noise. In addition, they result in better energy efficiency and longer pump lifespans. Reduced seal clearances prevent leakage of liquids and vapors, maintaining hygienic barriers between the process area and the external environment.
Design for cleanability is a primary focus in sanitary pump design. The aim is to do as much of the cleaning process as possible without disassembling significant components. Most sanitary pumps are designed to be clean-in-place (CIP) and sterilize-in-place (SIP) compatible, allowing cleaning and sanitization processes to occur without disassembly. This design feature is crucially essential in minimizing downtime. However, if manual cleaning is necessary, the pump housing should provide easy access to all areas that contact the product.
In addition to centrifugal and positive displacement designs, additional variations are targeted toward specialized applications. Rotary lobe pumps are designed for handling viscous and shear-sensitive fluids. The rotary lobe pump design incorporates two opposing lobes rotating within a casing, ensuring gentle handling.
Diaphragm pumps utilize a flexible diaphragm to move fluids. These pumps accommodate slurries and long-life cycles without leaks and meet hygienic standards. Progressive cavity pumps, with their single-helix rotor within a double-helix cavity, are often employed for viscous fluids, guaranteeing the steady flow rates and gentle handling necessary for sensitive fluid properties.
The intricacies of sanitary pump design reflect the necessity of maintaining cleanliness, efficiency and regulatory compliance across industries focused on consumable or health-related products. By focusing on materials, surface finishes, hygienic features and specialized design principles, manufacturers can create sanitary pumps that meet the diverse needs of their applications while emphasizing reliability, ease of cleaning and operational efficiency. As these industries continue to advance, the role and sophistication of sanitary pump design will evolve to meet new challenges and regulations, ensuring ongoing safety and performance in essential applications.
Sanitary pumps play a vital role in processes across multiple sectors:
Food and beverage: Sanitary pumps are used to move ingredients and finished products, which may range from water-thin beverages to viscous syrups. Precise control of flow rates ensures consistent product quality and batch uniformity.
Pharmaceutical: Sanitary pumps facilitate the precise, contamination-free movement of active ingredients and formulations in producing vaccines and other pharmaceuticals. Their ability to be sterilized by steam-in-place (SIP) methods is crucial to maintaining product integrity.
Fermentation: Sanitary pumps are also integral in processes like fermentation, where they must handle live microorganisms without causing damage. This requires a delicate balance of efficiency and gentleness, often achieved with positive displacement pumps.
Lubrication of Sanitary Pumps
The lubrication of sanitary pumps is a critical aspect that can influence their longevity and efficiency.
Lubricant selection: Lubricants used in sanitary pumps must comply with food-grade standards, such as those established by the National Sanitation Foundation (NSF) under categories like H1, which allows incidental food contact, or H3, which is soluble or edible oils.
Water-based lubricants: In some applications, water-based lubricants are preferred for their low toxicity should they come into contact with the pumped product. However, their corrosion prevention capabilities are limited compared to traditional lubricants.
Grease lubrication: Sanitary pumps may use grease to lubricate bearings and sealing areas, especially if they operate under heavy load conditions. Like all lubricants used in these pumps, grease must meet food safety regulations to avoid the risk of contamination.
Maintenance of Sanitary Pumps
Regular maintenance is critical to ensure sanitary pump reliability and longevity:
Preventive maintenance: Regular inspection routines involve checking seals for wear, ensuring appropriate lubricant levels and verifying the integrity of electrical components. Scheduling maintenance activities prevents unscheduled downtime and extends pump life.
Cleaning protocols: Sanitary pumps are cleaned using CIP techniques. In CIP systems, cleaning solutions are cycled through the pumps without disassembly, reducing downtime and labor costs.
Wear and component replacement: Key components like seals, impellers and valves require regular inspection and replacement as needed. Wear limits should be clearly defined based on manufacturer recommendations to ensure components are replaced before failure occurs.
Sanitary pumps are indispensable in industries where hygiene and product integrity are vital. Their design, aimed at preventing contamination, is coupled with precise applications ranging from the food sector to biotechnology.
Food-grade lubricants and regular maintenance ensure these pumps operate efficiently and safely. As technology and regulatory standards evolve, so will the design and application of sanitary pumps, presenting ongoing opportunities and challenges for industries relying on these crucial components.
For more on sanitary pumps, visit pumpsandsystems.com/tags/sanitary-pumps.