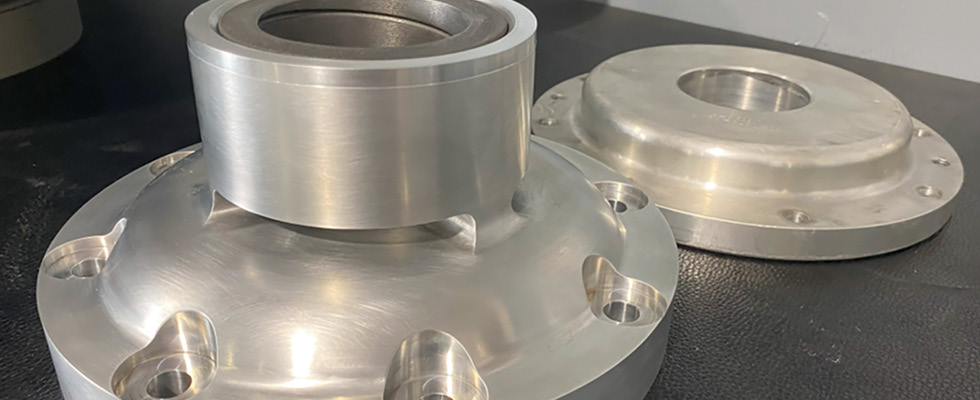
A U.S.-based pump repair company was asked to provide submerged cryogenic pump maintenance and services on a vertical pump at an ammonia manufacturing plant in liquid anhydrous ammonia service.
The pump’s design operating temperature was -27 F (-33 C) with a specific gravity of 0.686. It ran at a pump design pressure of 9.3 gauge pressure (barg), had a headplate/suction valve design pressure of 25.2/25.2 barg, a rated flow capacity of 729 cubic meters per hour (m3/h), a rated differential head of 111 meters (m) and a rated speed of 1,800 rotations per minute (rpm) driven by a 240-kilowatt (kW) motor. This pump was crucial to facility revenue, as it delivered the final hydrous ammonia product to be supplied to pipelines and vessels and taken to buyers.
The vibration monitoring system reported potentially catastrophic vibration levels, far beyond operational allowances. Operators took the machine offline and immediately called in the pump repair company to deal with the problem and get it back into operation fast.
The maintenance technicians’ first task was to rewire and upgrade the vibration monitoring system to verify the earlier results. The same high readings were found. To address vibration, a series of design changes were introduced. Customized housings were developed for the pump and the motor, the shaft was lengthened by 32 inches and a tail bushing and upper bushing made from a graphite-metal alloy were added to the shaft.
Further inspection found that some of the original bushings and bearings had contributed to extreme levels of vibration. The original bushings were made of various metals, including bronze and aluminum. Plant maintenance personnel reported that these components were regularly failing. Their average lifespan was found to be less than one year, or 100 hours of service. One bushing failed during a one-hour factory performance test.
Faulty bushings were also found to be a factor in other problems being experienced by the pump, such as shaft instability. Furthermore, the very tight clearances specified by some ammonia pump OEMs (tighter than the guidelines contained in American Petroleum Institute [API] 610) had led to contact between rotating components. When warmer fluids operate at high pressure in anhydrous ammonia pumps, metal-on-metal contact occurs with resultant adhesion, surface roughening, galling and material transfer.
(Image courtesy of Graphite Metallizing Corp.)
Anhydrous ammonia pumps deal with fluids in the -30 F (-35 C) range, quite different from the -260 F (-162 C) of liquid natural gas (LNG) fluids. As they operate at higher temperatures than other cryogenic pumps, there is more flexibility in selecting materials. Carbon steel can be used for the tanks, vessels and downstream components at the ammonia manufacturing plant. However, the use of carbon steel means there is usually more debris found in those fluids than in LNG applications.
The bearings in use at the plant were also causing problems, as they were not designed to deal with the heavy thrust loads that were taking place every time the pump started. Over time, bearing damage and failure resulted.
To address these issues, the cryogenic pump maintenance team made a series of modifications to the pump housing and the motor housing for smoother operation. The vibration monitoring system was also upgraded. Bronze and aluminum bearings and bushings were removed. New Babbitt-grade bushings were installed in custom housings. These bushings are designed to keep the tight tolerances required by the pumps.
The new bushings were made from nongalling material with improved wear resistance. Graphite metal alloy bushings improved overall component longevity and could cope with heavy thrust loads during startup. New bushings at the tail of the shaft and the upper end of the shaft provided greater rotor stability.
The repair shop coordinator requested that the bushings be slightly undersized. The goal was to conduct finish machining on the inside diameter to achieve the required dimensions and meet OEM clearances while also adding a spiral groove on the inside to prevent accumulation of debris (inspection had revealed the anhydrous ammonia fluid had some rust particulate debris).
Available grades can withstand temperatures as high as 1,000 F (535 C) and down to -450 F (-265 C). Graphite metal alloy materials are self-lubricating and have a low coefficient of friction. They are also dimensionally stable and have a low coefficient of thermal expansion across a wide temperature range.
After two years of service, the pump is working well and has not suffered another outage. Instead of the bushings failing
after an average of 84 hours, they have been running for about 1,000 hours without any problems. The upgraded
pump has the lowest vibrations of the three units at the facility. These have been measured at vibration levels that are nine
to 10 times lower than the others. As a result, the other two units at the facility are now undergoing a similar upgrade.