Blowers have been around since before the U.S. Civil War, but their operation is still sometimes misunderstood. Actually, the blower is a relatively simple device—as the shaft rotates, the impellers rotate in opposite directions with fine clearances between each other, as well as between themselves and the casing.
Probably the most confusing, and thus error prone, area in the application of blowers is the understanding of actual cubic feet per minute (ACFM) and standard cubic feet per minute (SCFM).
Engineers sometimes will specify flow in SCFM terms, which means it must be converted to the actual site conditions. This can make specifying for blowers complicated.
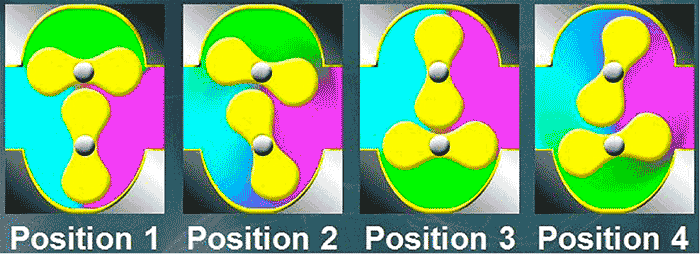
Blower Basics
Lobes, or impellers, rotate in four positions during operation. In this illustration, the top lobe rotates clockwise and the bottom lobe rotates counterclockwise (Image 1). As each impeller passes the inlet, a measured quantity of air is trapped between the impeller and the casing. As the shafts continue to rotate, this “pocket” of air is transported around the casing to the discharge side of the machine where it is expelled against the pressure prevailing in the discharge line. Every time this “pocket” is expelled to a higher pressure, a pulse occurs. A pocket of air is expelled four times—per one revolution of the shaft, or twice for each impeller. Hence, the frequency of the pulse is four times the shaft speed.
Volumetric efficiency = actual displacement/theoretical displacement
Equation 1
There is a leakage or “slip” component that is part of the machine’s inefficiency. Slip is dependent on the geometry of the blower and the discharge pressure. The higher the discharge pressure, the greater the amount of slip.
The 1 pound per square inch (psi) slip test is a quality control benchmark for the blower for clearances. In this test, the blower discharge is blanked-off and the blower is rotated at a speed to achieve 1 pounds per square inch gauge (psig) on the discharge; this rotational speed is used to calculate the slip rate in CFM, which can be used to extrapolate the slip at higher pressures.
Blower Limitations
The following items impact the efficiency of blowers:
Temperature rise: Temperature rise is the difference between the inlet temperature and the discharge temperature. The increase in temperature is caused primarily by the heat of compression according to the gas laws—plus inefficiencies within the blower and slip, which is internal recirculation and friction.
The impellers experience alternately inlet and discharge temperatures, thus operating at an average. The casing sees both temperatures plus ambient temperature. As a result, it typically operates at a lower temperature than the impellers. Due to this difference, the impellers change at a different rate than the casing reducing, the internal clearances. If the maximum temperature rise is exceeded, the impellers make contact with the casing, causing failure.
Discharge temperature: The discharge temperature is different from temperature rise. If starting with a high temperature with only a small rise, there can still be problems. Lubrication breaks down quicker and carbon forms causing increased friction for the bearings and gears. Eventually, the seals will fail, and there will be thermal distortion of parts, causing misalignment, excess stress and failure due to high temperature.
Mechanical limitations: Torque is a function of horsepower (hp)—and also of pressure. The higher the pressure, the higher the torque loads on the gears, which causes premature wear and failure.
Differential pressure: Impellers are simple beams. If the pressure limitations are exceeded, the impellers will deflect to a point by which they contact each other and or the casing.
Working pressure: Much like differential temperature and discharge temperature, working pressure is the inlet pressure plus the differential pressure. The working pressure can be exceeded even though the differential is within limits. The example would be a high-inlet pressure application.
Compressor Types
Below are some common types of compressors:
Pressure ratio: Like pumps, low-flow compressors with high-pressure ratios normally have a positive displacement design. This is not to say high-pressure ratios cannot be achieved with centrifugal machines. There are many multistage centrifugal machines capable of pressure ratios of 100 on heavier gasses. However, at lower flow values (Rotary lobe & vane: Rotary machines have a strong demand in many markets. Due to the construction, they are normally applied in markets handling air or relatively non-hazardous gas mixes. These blowers typically have a pressure ratio of around 2 to 2.5, and a sliding vane machine around 4.
Reciprocating piston: Reciprocating pistons can often provide the solution to low-flow, high-ratio applications. The simplest of these is a portable tank mounted air compressor. These are single-stage units usually rated for 100 psig and would have a flow rate of around 5 to 10 ACFM.
Multiple cylinder reciprocating: These machines are applied on hazardous gas mixes where higher-pressure ratios are required. This includes ratios such as hydrogen recycle where the pressure ratio is above 50. Most large ones will have intercoolers between each stage to remove the heat of compression before the gas enters the succeeding stage.
These heat exchangers can be as large as the machine and mounted adjacent to the compressor. Multistage models are often sited on a mezzanine elevated 15 or 20 feet above grade to accommodate the motor, which can be a large diameter synchronous design running at 400 or 500 rpm. These units are most commonly found compressing process gasses in refineries and large chemical plants.
Screw machines: Screw machines are used in both the air and gas market. This market uses 100 to 125 psig industrial plant air machines, provided in a noise enclosure and usually between 100 and 250 hp. Screw machines can be dry screw with Teflon-coated rotors or lubricated. Electronic and aerospace facilities insist on very pure plant air to avoid contamination in manufacturing. They lean toward dry screw technology. There are lots of older reciprocating plant air machines still pounding away in the basements of many manufacturing plants worldwide.
Large centrifugal: These compressors in the 30,000- to 100,000-hp range are routinely built and can deal with pressure ratios from single digit to over 100, depending on the process variables.
Specialty gas diaphragm: These compressors are used for very high-pressure ratio exotic gasses in aerospace and cylinder filling. They will be 50 to 100 hp and achieve ratios of 500 or more. They are best with very low flow rates at very high pressures.
Fans: On the other end of the gas-handling spectrum are fans, which are low-ratio machines. Fans are usually rated in inches of water column pressure and come in a wide variety of designs depending on the application. Fans produce large volumetric flow rates at low pressures.
Conclusion
Compressors are a wide variety of sizes, strengths and designs and there is no correlation from one application to the next. Unlike a pump where size visualization becomes more or less intuitive as you gain experience, a compressor offers no clue when you initially tackle the above sizing procedures.
Take note of the wide range of hps. Also note the effect inlet pressure has on hp with machines with similar pressure ratios. Remember that doubling the inlet pressure doubles the hp at the same volumetric flow. A compressor expert can help with the right selection.
Blower History
As with many inventions, the blower was discovered by accident. In the mid-1800s, the Roots Brothers were working on a better design for the water wheel, which ran machinery in their woolen mill. However, the water caused the counter rotating wooden paddles, or impellers, to swell and the device stuck. One of the brothers forced rotation and a burst of air blew his hat off. They immediately recognized the new machine—a rotary blower.
The blower was patented in 1860. By 1870, the major use of blowers was in foundry cupola furnaces in the steel industry and the mining industry for shaft ventilation. Other early uses included aeration, pneumatic conveying and supercharging.
Today, blowers are commonly used in oil and gas, chemical processing and wastewater treatment.