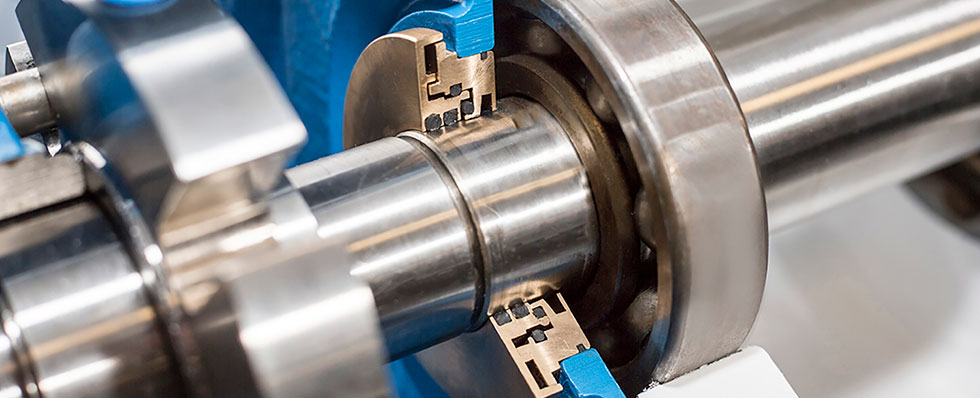
As better performing equipment was needed to survive harsher environments, so were better protections for bearings. This led to innovation in the form of bearing isolators, which are a relatively recent development in seal technology and act as a protective measure to replace traditional seals on bearings within rotating equipment.
A Quick Introduction to Bearings
Bearings are the bread and butter of the rotating equipment industry. They support rotating shafts in various machinery and engines, allowing for motion throughout pumps, motors and more. When bearings fail, the whole machine they support stops working as well. Aspects such as operating conditions and improper lubrication are the most common causes of bearing failure, as both involve bearing housings becoming contaminated. This is where bearing isolators come in.
Bearing Isolators
Bearing isolators are a type of lubrication seal designed to protect the lubrication of the bearing from contaminants, such as process fluid. These types of seals are the parts that separate the bearings of a machine from the external environment and any contaminants that would damage them.
They also play the vital roles of keeping the lubricant within the bearing cavity and keeping other components from contacting the bearings. Overall, bearing isolators increase the bearing’s life, so the machine’s life is also extended.
Types of Bearing Isolators
A common type of bearing isolator used to protect bearing lubrication is the contacting, compound labyrinth bearing isolator with a dynamic O-ring. Most other isolators are a derivative of this original design. The O-ring expands under dynamic conditions, which allows the housing to vent through the seals. Once the machine shuts down, the O-ring then contracts. This development was beneficial in advancing rotating equipment and is able to keep contaminants out by directing them outside the seal.
Contact-bearing isolators have their limitations. They struggle in environments with heavy contaminants, such as sand, dust and other debris, and settings with steam or oil mist. Because they typically contact the lip seal within the housing, they also cause the seal to wear down, and they cannot block contaminants during machine shutdown. Noncontact, compound labyrinth isolators are similar in design to the contact version but function differently.
Noncontact-bearing isolators use specific clearances, gap changes and direction changes to direct contaminants away from the bearing through gravity and centrifugal force. Because they do not contact a lip seal to operate, there is less wear on the seal and the bearing within. Noncontact-bearing isolators also struggle under static conditions.
As the machine shuts down, the bearing housing draws in air from the environment to reach a state of equilibrium, which can also draw in contaminants from the environment. Vertically oriented, noncontact isolators use their design of specific gaps and chambers to break down these contaminants’ energy and eventually force them away from the housing while still allowing in air that will not damage the lubrication. In other words, these isolators will enable the housing to breathe while controlling precisely what the housing inhales through the laws of energy conservation and gravity.
These new isolators are much more robust while still being small and manageable. As a result, they are incredibly flexible and can be used in various applications, such as electric motors, gearboxes, pillow blocks, turbines and more.