When MPP (not his real initials), a manager for a process pump manufacturer, told me his company was working on the thrust chamber design for its new horizontal pump, I was interested. After all, millions of process pumps would benefit from improved lubricant delivery and better bearing housings. So, in early 2016, I was pleased to respond to his query. MPP mentioned that the company’s pump speeds varied from about 1,800 revolutions per minute (rpm) to 4,200 rpm. Typical operation is at 3,600 rpm. The manufacturer’s goal was to design a superior “ball bearing thrust chamber” that could handle a force of up to 10,000 pounds (44,482 Newtons) of axial load. MPP and his team were considering three angular contact (7315) ball bearings to achieve this unusually high load capacity for a process pump. The inboard bearing could be either a typical deep-groove radial or an angular contact type to handle any minor short-duration reverse thrust action in the normally inactive direction. MPP communicated the following five other questions related to lubrication:
- Would a flinger disc provide enough lubrication for the third bearing if one were to maintain the oil level below the lowermost rolling element?
- They were considering raising the oil level to midpoint on the lowermost rolling element in the bearing. Would a flinger disc provide enough “splash” to cool the oil?
- Had I ever experimented with different shapes of flinger discs? MPP considered having a curved disc made, arguing that the curvature would help splash oil directly onto the bearing.
- Understanding that the oil splash (or flow rate) decreases with speed when using a flinger disc, MPP also had considered adding holes in the disc to provide additional oil splash. What were my thoughts on this? Plan B for his design would be to use only two rear bearings with an oil splash or bath. Suppose the third bearing would be required: Should MPP provide an oil mist system?
- Does anyone still make my Viton flinger disc patent? The original manufacturer of this technology no longer offered the flexible disc flinger. Did I know if these flexible discs were not profitable, or were there issues with reliability?
A Partial Answer
Because I know the end user’s mode of operating and maintaining pumps, I hesitated to recommend triple angular contact bearing sets1 for MPP’s new horizontal process pump. I imagined the purchaser’s hard-pressed reliability technicians trying to ascertain and supervise the proper installation of matched-bearing triple sets after explaining their cost to the global vice president of modern supply chain management. Triple sets require the expenditure of much more than the customary training, educational effort or maintenance money allocated to pumps at most plants. Flexible flinger discs were developed for snap-open insertion into bearing housings with openings/bores slightly smaller than the disc diameter. The original manufacturer of the Viton flinger disc later discontinued this product for economic reasons. The plastic discs that allow high peripheral speeds will not deflect much, and the ones that allow much deflection will not permit high peripheral speeds. In contrast, contoured metal discs similar to the straight one shown in Figure 1 are found in a number of thoroughly engineered pumps.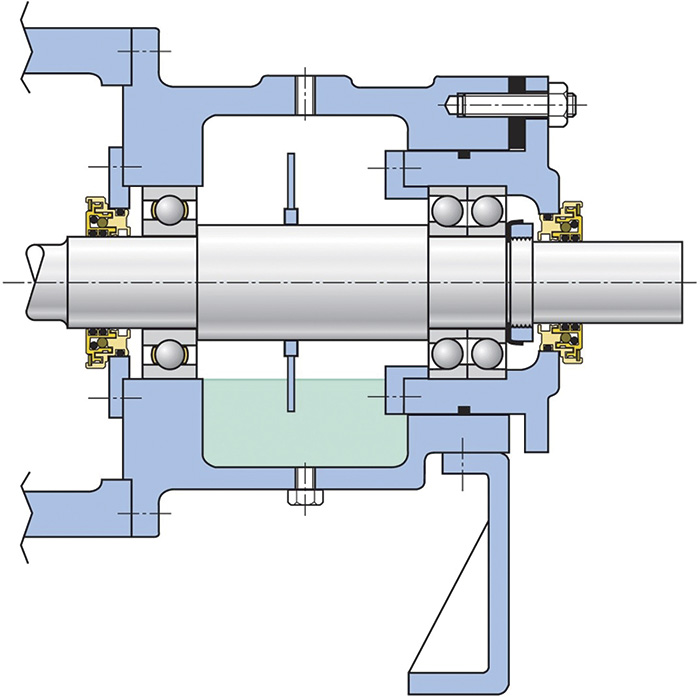