Pumps & Systems columnist Jim Elsey has more than 40 years of experience in the pump industry. During these four decades, he has witnessed numerous common pumping mistakes that, if avoided, could significantly increase pump system efficiency and reliability as well as prevent costly damage and safety hazards. Check out the list below to see if you're making these common errors.
1. Ignoring the IOM
"For every field problem on which I have been asked to consult, the problem could have easily been avoided if the end user read the instruction and operating manual (IOM). Actually, many of the top 20 mistakes could easily be avoided by simply reading and following the IOM before installing and starting the pump. Listing this as the top mistake may seem silly. Many professionals in our industry think reading the instructions makes them look uninformed. I still highly recommend reading the IOM, even if other personnel do not."
Read more.
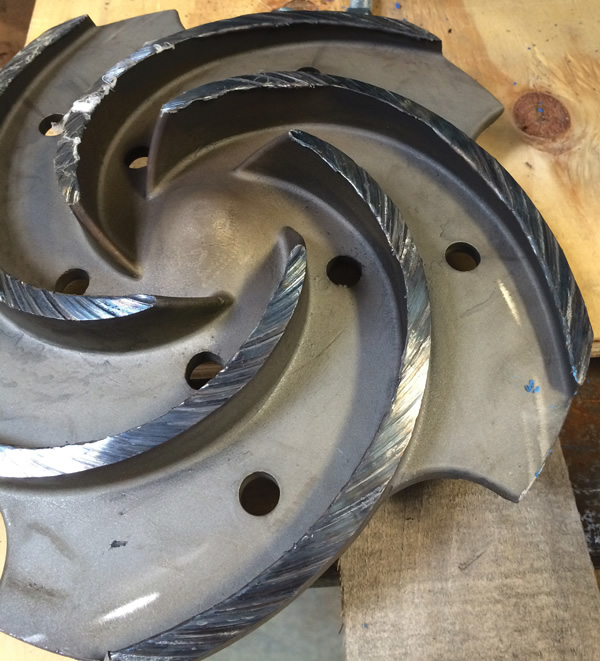
2. Operating the pump backward
"The second most common mistake is operating the pump in reverse rotation—basically, running it backward. This occurs when a pump should operate clockwise (CW) but it operates counterclockwise (CCW) or vice versa. I see this occur at least once per month.
For pumps with no way to prevent the impeller from backing off—such as American National Standards Institute (ANSI) pumps with threaded shafts and impellers—this is a major issue."
Read more.
3. Starting new pumps with no oil in the bearings
"Contrary to popular belief, pump manufacturers do not put oil in the pump bearing housings before shipment. This is usually because shipping a pump with oil in the housings is illegal in most circumstances. At least three U.S. governmental entities restrict this practice, because oil—especially when being transported—falls under hazardous material regulations. ... Manufacturers also avoid placing oil in the pump bearing housings because they typically do not know which type or brand of oil the end user will choose, and the oil can easily be spilled, leaked or contaminated during the transportation and installation processes. Most pump manufacturers publish explicit warnings about the need to add oil to the bearings both in their instruction operating manuals and on the pumps. Despite these cautions, starting a new pump without oil in the bearings is one of the most common mistakes end users make—far more common than it was forty years ago. The resulting damage is usually significant, causing unwanted downtime and additional material and labor costs."
Read more.
4. Confusing suction pressure with NPSHA
"The common misconception is that the pump will "suck" the fluid from the suction system into the pump.
Perhaps if liquids had tensile strength characteristics, that could be remotely possible (I acquiesce that the impeller does create a small differential pressure at the eye), but the suction-side system must have adequate energy to deliver the fluid to the pump. Using the analogy of a cellphone, if the suction-side system does not have enough "signal strength" (bars of energy), then the "call" will be dropped or be of poor quality—in other words, the pump will cavitate."
Read more.
5. Running a second pump in parallel to increase flow without considering the system requirements
"In a typical scenario, someone observes there is an additional installed pump and decides the solution is to simply start and operate the second pump. To an untrained person who sees two pumps installed in the same system, it seems logical that operating the second pump in parallel will increase the flow. This may work in some instances but often does not. When the system is not designed for two (or more) pumps to operate at the same time (in parallel), it will not take long for both pumps to experience issues."
Read more.