While power plants in the U.S. require trillions of gallons of water each year, various substances in significantly more precise measurements are needed to transform the liquid into ultra-pure water for boilers that help generate electricity. These compounds commonly include ferric sulfate, which is a crystalline salt that is soluble in water and used as a coagulant, and sulfuric acid, which is a highly corrosive and toxic mineral acid that is soluble in water at all concentrations. In power plants, ferric sulfate helps remove solid particulates from water, and sulfuric acid is used to control the pH, or alkalinity, of the water used in boilers. Ensuring that proper doses and flow rates of ferric sulfate and sulfuric acid are reliably achieved is important for power plant operators. To ensure the proper concentration and flow of ferric sulfate and sulfuric acid, hydraulically actuated diaphragm metering pumps may be an ideal solution. They can help guarantee that water used in power generation meets the high levels of purity required.
The Challenge
The purification of water needed for power generation occurs through a number of specific operational stages. The first involves the water's passage through a clarifier, where any large, solid impurities are removed. Next, the water travels through a filter, where any dissolved solids—not visible to the naked eye—are removed. These initial pretreatment stages are critical because, from there, the water moves through a demineralizer that cannot handle water containing solids When water is demineralized, most of the positive and negative ions are removed, creating, by definition, an ion-free solution. This is another critical stage in the power generation process because only demineralized water can be heated in the boilers to create the steam that generates power.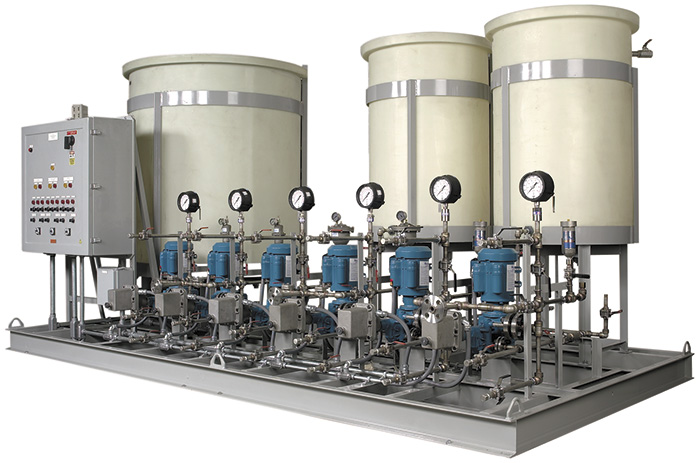
One Solution
Hydraulically actuated diaphragm metering pumps possess the operational capabilities and reliability to perform these crucial operations in a power plant. For instance, metering pumps can handle these applications because they can be dialed in to meet specific flow and dosage parameters, which are the lifeblood of a power plant's water purification process.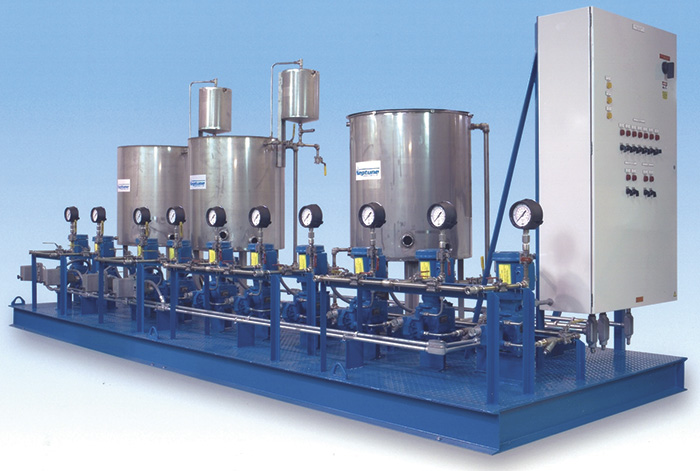