One of the main difficulties of analyzing the operative performance of centrifugal compressors involves how the data is presented. Expected performance is generally depicted using graphs of discharge pressures and temperatures, polytrophic heads, efficiencies and absorbed power related to the design inlet gas conditions (i.e. gas mix composition, inlet pressure and temperature). However, actual performances are strictly related to field inlet gas conditions that are different from design conditions. The comparison of field measurements to expected values is complex because the expected performances must be adjusted to the actual suction field conditions. This article presents a method and tools for evaluating centrifugal compressor field performances and comparing them to design/expected performances. The current practice is based on simplified theories, which are often neglected at the plant/machine level. This oversight can lead to a lack of analytical support capability for the evaluation of machine health and performance, which can negatively affect maintenance decision-making. These simplified theories become progressively more approximate, especially when approaching the high-pressures range. In order to execute this advanced performance analysis, the research lab employing these evaluation methods used a dedicated software tool based on the most recent gas theories and centrifugal machine models. The software tool is designed to easily and quickly reveal centrifugal compressor performance evaluations. It offers centrifugal compressor analysts and industry users a powerful and easy tool to predict machine performance under different operative conditions.
Method
For a centrifugal compressor, performance is strictly linked to the inlet gas conditions. Accurately comparing different inlet conditions is impossible. It is necessary to adjust and align performances to the same reference inlet conditions. When attempting to evaluate performances by comparing field-measured parameters and expected parameters, the trick is to remember that one of the two performances must be manipulated and adjusted to the inlet conditions of the second one. In other words, inlet conditions must be homogeneous (see Figure 1).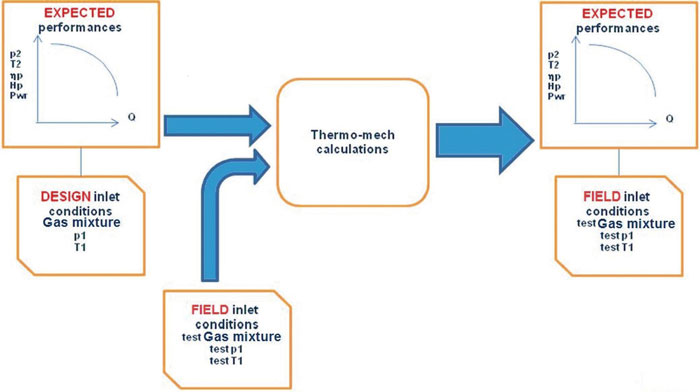
- Step 1: Adjust expected performances related to design inlet conditions to field suction conditions.
- Step 2: Compare field performances to adjusted expected performances.
Software
The starting point is the availability of a centrifugal compressor performance curve, the relevant gas mix composition and thermodynamic conditions (pressure and temperature). Using this input data, the software performs calculations in a fully automated way. It also produces the expected compressor performances for inlet pressures, inlet temperatures and gas mix compositions different from design or reference performances. The software is intuitive, and it provides automatic data storage for quick consultation and historical trends. The software allows analysts and engineers to build their own machinery database and maintain records of all executed calculations. Once the project is set up, the software has all necessary data to perform the computations. Beginning the calculation requires inputting the new gas mix before calculating the new inlet pressures and temperatures. Once completed, the software will display the new compressor performance map. After this first calculation step, a performance analysis tool can compare field-measured data with expected data.Case Study
In the following example, a compressor was running under off design inlet conditions. An analysis provided a performance evaluation and comparison to the design values. A centrifugal compressor performance map in two different inlet conditions of pressure and temperature were available (see Table 1).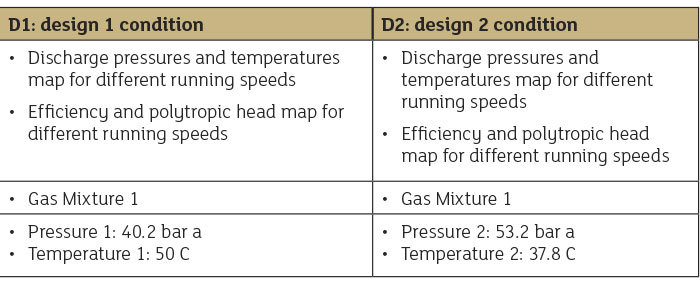
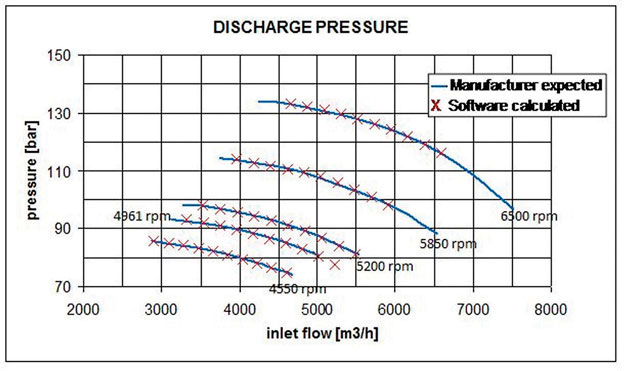
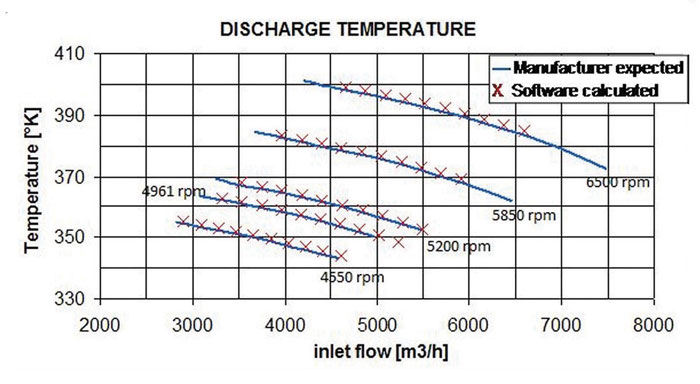
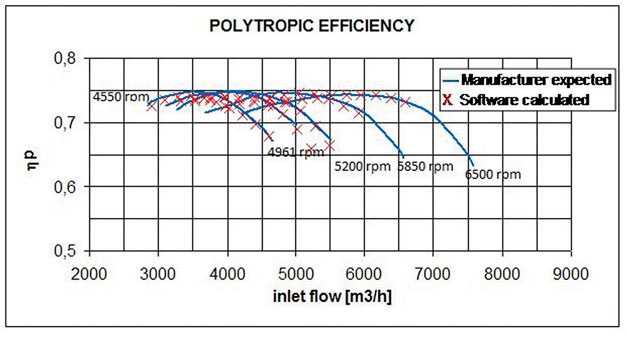
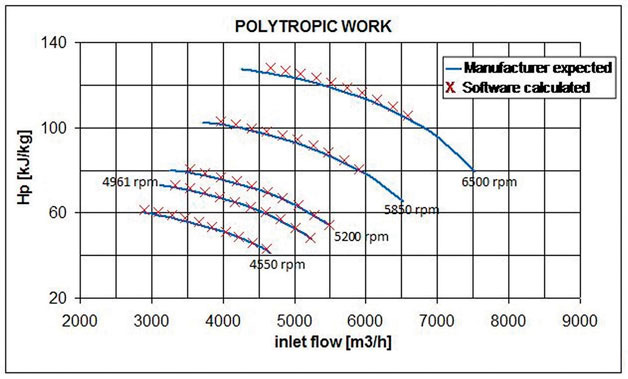
Conclusion
The methods proposed and described in this article can provide the following benefits to end users:- Predict the performances of a centrifugal compressor under varying thermodynamic conditions of the inlet gas. The prediction of compressor performances is accurate even at high pressures, where the ideal gas theory commonly used introduces considerable errors.
- Analyze the performance of the compressor during operation and compare results with those expected provided by the manufacturer.
- Implement advanced protection from a surge, overcoming limits of the current technology.
- Deliver useful indications on the health of the compressor (diagnostics) based on the capability to analyze the performances and efficiency of the machine in a simple and immediate way.
- Support decisions and planning of predictive maintenance and activities.