Chronic problems are rarely solved unless the underlying issue is addressed. Often in pumping systems, diagnosing these problems is difficult and it may not be the first culprit suspected. Here, a paper mill was able to reduce operating, maintenance and capital costs while increasing system performance by fixing a chronic maintenance problem. The mill was experiencing persistent cracking on the discharge header on a vat at a dilution pump resulting in a discharge header that required repair. To fix the discharge header, the plant had to be shut down, the pipeline drained of its valuable product and sent to the environmental treatment ponds. In addition to the pipe cracking, there was severe movement of the discharge pipe, along with excessive pump vibration causing additional damage. After years of dealing with the issues caused by ongoing vibrations and cracking in other parts of the mill, plant managers decided it was time to correct the problem. Time-consuming and costly hit-and-miss diagnostics were initially used to determine the root cause of the issue. The primary problem to address was the extensive cracking in the pump-discharge piping system. The mill reasoned it was due to thermal stresses caused by rapid heating of the discharge piping during plant startup. As a result, the focus on plant modifications to reduce the rate of temperature change during plant startup was the first initiative. Second, the team determined it was necessary to look for ways to minimize the pump vibration and bring the pump maintenance cost in line with similar pumps in the plant. Their first efforts in correcting the cracking problem by minimizing the rate of temperature change in the discharge header were not effective. After a false start, management decided to look at the operation of the piping system.
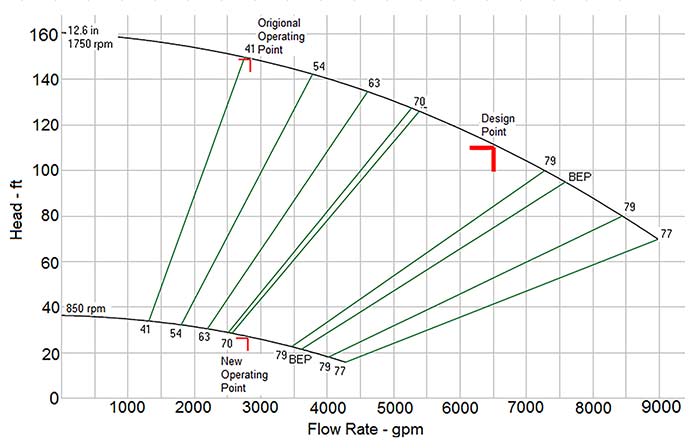
Discovering the Root Cause
After careful review, the team decided to focus on the interaction between the pump and its system. The pump was initially specified for a 6,500 gallon per minute (gpm) flow rate and 110 feet of head. It was supplied with a 250-horsepower (hp) motor running at 1,750 revolutions per minute (rpm). The best efficiency point (BEP) for the installed pump occurred at 7,900 gpm (see Image 1). Looking at the operation of the vat dilution system using piping software, it was discovered the required flow rate was only 2,800 gpm. Running at this lower flow rate resulted in the pump operating below its original design point and far to the left of the BEP flow. After performing an analysis of the entire system, it was determined the pump was oversized both in the specified flow rate and pump head. The results of the study determined that the system required only 26 feet of the pump head to meet the 2,800 gpm flow requirement of the vat dilution system. To better match the pump to the system, a variable frequency drive (VFD) was installed. With the pump operating at 850 rpm, the pump was able to meet the flow rate of 2,800 gpm with the required system head. The pump operation at 850 rpm is displayed in Image 1.Reducing Operating Costs
Notice on the pump curve that with the pump operating at 1,750 rpm, the pump produces approximately 145 feet of head with a flow system flow rate of 2,800 gpm. The pump operating at this flow rate requires approximately 170 hp. At the lower speed of 850 rpm, the pump is able to meet the system flow and head requirements by consuming only 70 hp. This reduction in speed resulted in a 60 percent savings on the cost of power to operate the pump. The lower power requirement at the slower speed also allowed for the use of a low-voltage motor and VFD, resulting in significant savings. Using the plants low power cost of $0.025 kilowatt hours (kWh), installing the VFD resulted in a calculated energy savings of $16,500/year. Based on the cost of the VFD and the savings in energy consumption, the project had a return on investment (ROI) of 20 months.Cutting Maintenance Costs
To project future maintenance savings when evaluating a pumping system, there is 100 hp less power going into the fluid in the system. That extra 100 hp supplied by the pump, due to running at a higher speed, was removed from the fluid by using an over-throttled control valve. This also reduced wear and tear on system components. Another way of looking at the system is the excess power was wasted, pushing more energy than necessary, operating the equipment at a higher threshold, causing more stress on the equipment thereby increasing the maintenance costs. Lastly, looking at the pump curve, we can see that when the pump is operating at 850 rpm with a flow rate of 2,800 gpm it is operating much closer to the BEP. Running a pump closer to its BEP has been proven to increase pump reliability. Once the VFD was installed in the system and the pump operated at a lower speed, the vibration on the pump and discharge header were virtually eliminated. One year after operating the pump at the lower speed, the pipe cracking in the discharge header was eliminated along with the need to repair pump seals and bearings. With the loss of the pump vibration, discharge header cracking, pump bearing and seal repairs, a documented $15,000 per year in maintenance savings was realized. By factoring the documented maintenance savings into the power savings the ROI for the VFD was reduced from 20 months to 10 months. For the past five years, the only maintenance performed on the vat dilution pump had been routine preventative maintenance.Increasing Plant Up-Time
With the system operating with fewer repairs, there were additional savings due to increases in system uptime. Just like maintenance savings, increases in plant uptime are difficult to project. In our vat dilution example, once the VFD was installed, the cracking in the pump discharge header and excessive pump maintenance was eliminated, and as a result:- The vat dilution system was able to operate for longer time periods without breakdowns, resulting in increased plant uptime.
- The cost associated with draining the vat dilution systems for repairs and sending the filtrate for environmental treatment was eliminated.
- Since the number of unplanned outages of the vat dilution system was reduced, the entire plant was able to operate longer and produce products at a higher quality.
Lessons Learned
By performing this assessment, the plant had several takeaways:- Running the pump more efficiently (closer to its BEP) resulted in energy savings, and those savings can be easily calculated.
- Running the pump more efficiently reduces the excess power added to the system. The excess power results in the generation of heat, noise and vibration. Based on this case study, one could make the case that the savings in maintenance costs could be estimated as the same order of magnitude as the savings in power cost.
- If the equipment can run longer between forced shutdowns, more products can be made resulting in increased uptime and plant profitability.