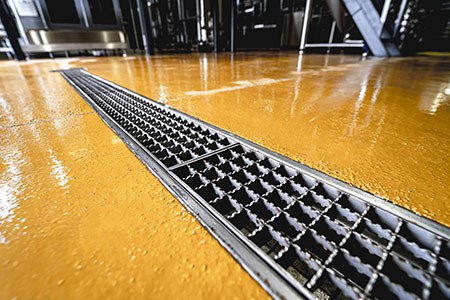
Beverage production involves complex processes, ranging from ingredient preparation and fermentation to filtration and packaging. While much focus is placed on ensuring the product’s quality, the importance of an efficient and reliable wastewater management system cannot be overstated. The solid waste produced in beverage manufacturing—from spent grains and fruit pulp to yeast and other residues—poses major challenges for wastewater treatment systems. An effective solids handling system is necessary to maintain smooth operations, prevent blockages and ensure compliance with environmental standards.
Submersible pumps are crucial in managing these solids and maintaining an efficient flow within wastewater systems. By understanding submersible pumps’ requirements and capabilities, beverage producers can optimize operations, reduce maintenance and increase system longevity.
The Role of Submersible Pumps in Beverage Wastewater Systems
Submersible pumps are designed to operate while fully submerged in liquid, making them ideal for handling large volumes of wastewater and solids in various industries, including beverage production. Unlike traditional pumps that draw water from the surface, submersible pumps push water or wastewater upward from the submerged pump, providing a more compact and efficient solution in confined spaces.
In beverage production, wastewater often contains a mixture of solids such as spent grains, fruit pulp, seeds and yeast. The challenge of managing these solids lies in their size, consistency and abrasive nature, which can cause significant wear and clogging in traditional pumping systems. Submersible pumps, particularly those designed for solids handling, are engineered to cope with these demands, offering continuous, reliable operation under harsh conditions.
Technical Features of Submersible Pumps for Solids Handling
1. Solids-handling capabilities
Submersible pumps in beverage production are typically designed with high solids-handling capacities to manage the dense, viscous materials often found in wastewater streams. These pumps are equipped with specially designed impellers, typically open or semi-open configurations, which prevent solids from blocking the flow. The design of these impellers allows large, abrasive solids like spent grains, fruit pulp and yeast to pass through without causing damage to the pump.
Submersible pumps with hardened or wear-resistant impellers can efficiently process solids without the risk of clogging. Handling a range of particle sizes and densities is crucial in beverage production, where solids can vary from soft grains to fibrous fruit pulp and seeds.
2. Solid construction and material selection
Submersible pumps used in the beverage industry must be constructed from durable materials capable of withstanding the abrasiveness and corrosiveness of the wastewater they handle. Stainless steel, cast iron and other corrosion-resistant materials are commonly used for the pump casing, impeller and other critical components.
Submersible pumps are often coated with protective layers, such as abrasion-resistant coatings, to enhance longevity in aggressive environments. For example, in juice processing, where acidity levels can be high, pumps with corrosion-resistant properties are essential for ensuring consistent performance over time.
3. No loss of priming
When a pump loses prime, it takes time and effort to send a technician to re-prime it. During the lost pumping time, there is potential for a spill to take place. Submersible pumps eliminate this concern by operating with a flooded suction, and they never need to be manually primed. The flooded suction also provides an advantage when operating on liquids with high solids contents and in applications with low net positive suction head available (NPSHa), such as high temperature applications or those at high elevation.
4. Motor protection and thermal management
Submersible pump motors are often housed in a sealed casing to prevent water loss. Advanced submersible pumps in beverage production also include built-in thermal overload protection, ensuring the motor does not overheat under load conditions. This is especially critical when handling viscous liquids or high solids content. This protection allows the pump to run efficiently in continuous operations and reduces the likelihood of failure due to motor burnout.
In high-temperature applications, such as juice processing, where the wastewater may be elevated in temperature, submersible pumps with special thermal insulation or heat-resistant components are used to maintain reliable performance without damaging the internal motor components.
5. Flow regulation and variable speed drives
Some submersible pumps are paired with variable speed drives (VSDs), which allow precise control over the flow rate and pump speed. Flow regulation can be achieved by adjusting the speed to change where the pump operates along the system curve.
Sometimes, a reduction in pump speed is necessary to maintain the amperage drawn below the pump nameplate full load amps (FLA). For instance, in juice production, the solids content can fluctuate depending on the fruit being processed. Having a pump that can adjust to handle these variations ensures smoother operations.
VSDs also improve energy efficiency by adjusting the motor speed to match the system’s specific demand rather than continuously running the pump at full capacity. This reduces energy consumption and operational costs, especially in large-scale beverage production facilities.
Applications for Submersible Pumps in Beverage Wastewater Systems
1. Juice production
Submersible pumps are vital for handling the wastewater from processing fruits and vegetables in juice manufacturing. The wastewater may contain large quantities of fibrous materials, seeds and pulp, which can be difficult to process without the right equipment. Submersible pumps with solids-handling capabilities transport this wastewater to treatment facilities, where the solids can be filtered, and the liquid can undergo further treatment. The durable, flooded suction design of submersible pumps allows them to operate continuously, reducing the risk of downtime and increasing overall system efficiency.
2. Brewery wastewater management
In breweries, the wastewater generated during brewing often contains spent grains, hops and yeast residues. These materials can clog traditional pumps and filtration systems if not properly handled. Submersible pumps designed for solids handling can efficiently move this wastewater through the system, preventing clogging and ensuring consistent flow. In addition, submersible pumps’ high wear resistance and robustness allow them to endure the abrasive nature of spent grains and hops over long operational periods.
3. Distillery and fermentation applications:
In distilleries or fermentation facilities, submersible pumps are crucial for managing fermentation byproducts, which often consist of thick, slurry-like wastewater with suspended solids. The ability of submersible pumps to handle these challenging materials ensures production can continue smoothly without interruptions caused by clogging or failure.
Key Benefits
Efficiency and continuous operation: Submersible pumps are built to operate continuously without overheating, ensuring a constant wastewater flow through treatment systems, which is essential in high-volume beverage production.
Improved solids handling: With robust impeller designs and self-cleaning features, submersible pumps can process large solids, preventing blockages and reducing the need for manual intervention.
Durability and longevity: Submersible pumps constructed from corrosion-resistant materials can withstand the harsh conditions found in beverage production, extending their lifespan and reducing the frequency of maintenance.
Energy efficiency: Advanced submersible pumps with VSDs optimize energy consumption by adjusting motor speeds based on system demands, offering savings on operational costs.
Managing wastewater and solids in beverage production is a complex yet essential task. Submersible pumps offer a reliable, efficient solution to handle the challenging byproducts produced during the various stages of beverage manufacturing.
By selecting the right submersible pump for their specific needs, beverage producers can ensure optimal performance, minimize operational disruptions and improve the overall efficiency of their wastewater treatment systems. As the beverage industry continues to grow, the role of submersible pumps in managing wastewater efficiently and sustainably will only become more crucial.
For more on food and beverage, visit pumpsandsystems.com/tags/food-and-beverage