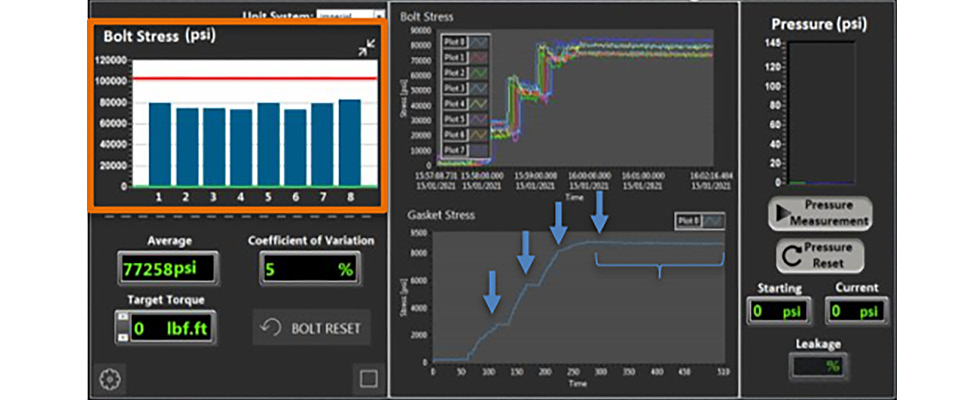
Bolted flange joint assemblies (BFJA) serve as critical pressure boundary connections in piping, pressure vessels and heat exchangers. The reliability of these joints is contingent not only on engineering design but also on how well materials are selected, assembled and maintained. Gasket and bolt relaxation is a critical component of that reliability. If unmanaged, relaxation leads to compromised sealing performance and long-term joint integrity.
To improve BFJA reliability, it is vital to have an understanding of how gasket materials behave under load, how bolt stress changes over time and when to apply retorque procedures.
When Does Relaxation Occur?
Sheet gaskets (e.g., skived polytetrafluoroethylene [PTFE]) will typically relax at ambient temperatures. However, semimetallic gaskets (e.g., spiral wound gaskets [SWG]) are not as susceptible to gasket relaxation.
Semimetallic gaskets do get blamed for relaxation, yet when the bolt sees higher temperatures, roughly 500 F (260 C), it will relax and that will decrease the gasket stress.
Gasket Material Considerations
For polymer-based gaskets, particularly those made from PTFE, the mechanical behavior under load varies depending on material type and processing quality. Skived or molded virgin PTFE offers excellent chemical resistance but can suffer from poor mechanical strength and high creep under load. This leads to greater gasket relaxation and a loss of sealing stress over time.
In contrast, restructured PTFE (rPTFE) and expanded PTFE (ePTFE) utilize higher quality resins and engineered microstructures, significantly reducing creep and enhancing strength. rPTFE can additionally have inorganic fillers, such as hollow glass microspheres, barium sulfate and silica, to enhance specific properties. These materials often offer better performance in flange joints and are useful in critical applications where dimensional stability is required.
When higher compressive strength is required, semimetallic gaskets, such as SWG and kammprofile gaskets, can offer better load retention and minimal relaxation under dynamic conditions.
Selecting Gasket Material
Given the differences in material behavior, selecting the appropriate gasket material must be guided by application-specific requirements, including:
- Operating temperature and pressure
- Chemical compatibility
- Expected flange movement, vibration or thermal cycling
- Long-term stress retention
Following the selection of gasket materials, ensuring long-term joint integrity requires adherence to established assembly protocols, particularly those governing bolt load application and dwell time as outlined in standards such as the American Society of Mechanical Engineers (ASME) PCC-1 Pressure Boundary Bolted Flange Joint Assembly.
ASME’s subcommittee responsible for PCC-1 is currently working on expanding the standard to address both gasket and bolt relaxation. The next edition will be published in 2026.
Since it is not currently published, it is not possible to include the material in this article but below is a list of good practices the update will be based on.
Assembly Best Practices
1. Dwell time
Dwell time for sheet gasket materials allows the gaskets to relax after initial loading. This pause helps ensure that any early loss in bolt preload is addressed before applying a “relaxation pass” to regain any gasket stress that might have been lost to relaxation.
Please note that a relaxation pass uses the final torque value in a circular pass around the flange at ambient temperature. A startup retorque (PCC-1) is a relaxation pass but when there is temperature or process in the vessel.
According to standard industry belief, it is advisable to wait multiple hours or days before applying a relaxation pass. Research has shown, however, that shorter dwell times, as brief as 15 minutes, for instance, offer a practical compromise between the time required to perform the retorque and the gasket’s ability to retain stress. The optimal dwell time depends on factors such as gasket type and specific operating conditions. Therefore, it should be validated through field experience or by following manufacturer guidelines.
2. Torque application techniques
A controlled, consistent torque pattern (often the star pattern) is essential for uniform gasket compression. Application guidelines emphasize applying torque in a multipass star pattern and final circular pattern, using calibrated tools to ensure accurate load. The relaxation pass after dwell time is to restore preload lost to relaxation. Some end users are starting to record bolt stress values using ultrasonic or digital torque verification tools where possible.
While proper assembly establishes the foundation for joint integrity, maintaining that integrity over time requires proactive monitoring and follow-up procedures.
Maintenance & Monitoring
To address bolt stress loss and gasket creep over time, two critical procedures are employed: relaxation passes and startup retorque.
Relaxation passes: A relaxation pass is the process of reapplying torque to all bolts at the same initial value, typically at ambient temperature, after allowing a short dwell period for the gasket to settle and any initial bolt preload loss to occur. This restores preload lost to initial gasket seating and short-term creep.
Startup retorque (previously known as “hot torquing”): All bolted flange joints experience some degree of gasket relaxation after initial tightening, regardless of whether the system operates in elevated temperatures or not. This is why a standard retorque is always recommended as part of the installation process.
However, for systems that heat up during operation, additional relaxation occurs during thermal expansion and gasket deformation. In these cases, a startup retorque is advised to restore proper bolt load and ensure long-term sealing performance.
For high-temperature systems, it is ideal to perform this retorque while the assembly is still below 450 F (232 C). Above this threshold, lubricant degradation and changes in the friction coefficient (K-factor) can significantly affect torque accuracy, making stress calculations unreliable. Therefore, if the flange is expected to reach high temperatures, the retorque should be planned during the warm-up phase before these adverse effects set in.1
It is important to note that the term “hot torque” has been retired in favor of “startup retorque” by ASME PCC-1 to avoid confusion with hot bolting (single stud replacement). This is a planned maintenance procedure, not a live-line repair activity.
While these procedures are grounded in best practices and industry standards, their effectiveness can vary depending on gasket material and application conditions. Field testing and data-driven validation are essential to fine-tune retorque strategies and ensure long-term joint reliability.
Validation Through Field Testing
A controlled, multiweek testing was recently conducted on a range of gasket materials to better understand how different gasket classes respond to compressive load and stress relaxation over time. The study analyzed gaskets at room temperature and aimed to evaluate whether the commonly recommended four-hour dwell time before retorque is universally necessary across all gasket types, or whether shorter intervals could offer similar sealing performance with reduced downtime.2
Key findings include:
- Semimetallic gaskets, such as SWG and kammprofile styles, exhibited exceptionally low bolt stress loss across all dwell time intervals tested. Even without retorque, these gaskets retained most of their initial load. For example, stress loss for SWGs changed by only approximately 1.6% between no retorque and a full 24-hour period. This suggests that for semimetallic gaskets, the benefit of retorquing after several hours is marginal at best.
- PTFE-based gaskets, on the other hand, displayed much greater variation in relaxation behavior, reinforcing the need for material-specific bolting strategies:
- ePTFE showed early stress loss, with 12.6% relaxation after 20 hours when not retorqued. A retorque just 15 minutes after installation cut stress loss nearly in half to 7.5%, with only marginal improvement at one hour (7.0%), four hours (5.9%) and 24 hours (3.0%). This suggests that most of the benefit can be achieved with a short dwell time, while longer delays offer diminishing returns.
- rPTFE demonstrated similar relaxation trends. Stress loss dropped from 12.5% with no retorque to 7.8% at 15 minutes, 6.6% at one hour, 5.3% at four hours and 4.4% at 24 hours. Although some improvement was observed with extended dwell times, most of the benefit was realized within the first hour.
- Skived PTFE (sPTFE) performed significantly worse, exhibiting the highest stress loss of all tested materials: 20.0% when not retorqued. While it stabilized relatively early (dropping to 12.3% at 15 minutes), it remained at 11.7% at one hour and 11.3% at four hours, showing a consistently high residual loss. Even after 24 hours, it had a stress loss of 8.0%, markedly higher than ePTFE or rPTFE. This indicates that although sPTFE plateaus quickly, its absolute relaxation is substantially higher, making it less reliable for long-term sealing in demanding applications.
While it is always preferable to allow the longest possible dwell time before retorque, the study demonstrates that not all gasket materials require the same treatment. A one-size-fits-all approach does not reflect the true behavior of different gasket types.
If time constraints exist, semimetallic gaskets may not require retorquing at all in certain applications, given their minimal relaxation. In contrast, PTFE-based gaskets benefit from early retorque, often well before the standard four-hour mark. Depending on the material, much of the stress loss is recoverable in as little as 15 to 60 minutes.
These findings enable maintenance teams to make more informed, material-specific decisions, optimizing bolting procedures to improve sealing performance while minimizing unnecessary downtime.
The Effects of High Temperature
At elevated operating temperatures above 500 F (260 C), bolt relaxation can increase significantly. A study presented at the ASME Pressure Vessel and Piping Conference3 showed:
- American Society for Testing and Materials (ASTM) A193 Grade B7 bolts lost up to 60% of preload at 725 F (385 C).
- ASTM A193 Grade B16 bolts fared better with 25% relaxation.
- ASTM A193 Grade B8M stainless bolts even gained preload due to differential thermal expansion.
For high-temperature service applications, careful material selection is essential to maintain joint integrity under thermal stress. Bolting components should be upgraded to materials with proven performance at elevated temperatures, such as ASTM A193 B16, to mitigate the risk of significant bolt stress relaxation.
It is also critical to pair these studs with appropriately graded nuts. For example, B16 studs need to have Grade 4 or Grade 7 nuts to minimize relaxation in the nut.
The integrity of bolted flange joints depends on far more than torque values and gasket selection; it is rooted in a thorough understanding of material behavior under compressive and thermal load over time. Gasket relaxation, bolt stress loss and flange movement are not singular events but ongoing phenomena that require predictive maintenance strategies, material science insight and strict adherence to assembly protocols.
As field data continues to highlight the complex interplay between gasket types, load retention and temperature, it becomes clear that engineers must adopt a proactive, data-informed approach, leveraging material-specific testing, time optimization and validated retorque procedures to extend joint performance and reduce unplanned downtime.
By integrating high-quality gasket materials, disciplined assembly techniques and rigorous maintenance practices, industries can extend the service life of their flange joints and reduce the risk of unplanned shutdowns.
References
- hextechnology.com/articles/bolted-flange-joint-relaxation-pass
- Girão, C. D., Meira, I. & Veiga, J. C. (2021). Can the Four-Hour Installation Dwell Time Be Reduced? Volume 2: Computer Technology and Bolted Joints; Design and Analysis, V002T02A004. doi.org/10.1115/PVP2021-61833
- Brown, W, & Lim, T. “Quantifying Bolt Relaxation During High Temperature Operation.” Proceedings of the ASME 2017 Pressure Vessels and Piping Conference. Volume 3A: Design and Analysis. Waikoloa, Hawaii, USA. July 16-20, 2017. V03AT03A031. ASME. doi.org/10.1115/PVP2017-65550