Infrastructure has been a hot topic for years now, particularly in utility circles. In the wider public, Americans are aware of infrastructure because so many of us depend on having navigable roads and bridges to get from one place to another, and these days they are overcrowded and often in need of repair. Other people may have an appreciation of the importance of infrastructure if they work in an area where a broken water main has flooded homes and businesses or disrupted service. Typically, we think about infrastructure only when it is not working properly, and usually that is because it has caused an unexpected inconvenience. Utilities, whether public or private, and the infrastructure networks they maintain serve as the (often unseen) bones and skeleton of our cities and towns. Not only do utilities provide necessary services to residential areas, but they also service retail centers, manufacturing facilities, other utilities (water treatment facilities are some of the largest users of electricity) and business districts.
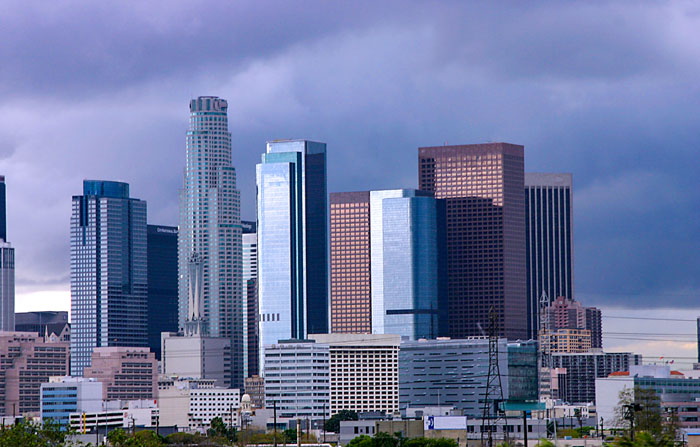
The Facility
In the past decade, a city in the American Midwest initiated a project to upgrade and expand its convention center. Today, that facility is one of the largest convention centers in the country. The distinction comes with significant demands on the various utilities that service the facility. Convention centers and other venues that host tens of thousands of people typically go from being virtually empty to the size of a small city in a matter of hours. One of the consequences of this quick transition is that the demands put on the infrastructure supporting the facility are nearly instantaneous and great. In the winter, it is cold in the Midwest, and if the convention center is in use, its vast halls and meeting rooms need to be heated. In this particular facility, heat generation is accomplished with steam.The Challenge
Depending on steam’s source and unique characteristics, the resulting condensate can be corrosive and hot. Accordingly, this expanded convention center has a number of sumps to collect condensate from the steam heating. One sump in particular was creating constant problems for maintenance crews because the vertical-style sump pumps were being damaged due to the hot, corrosive condensate..jpg)