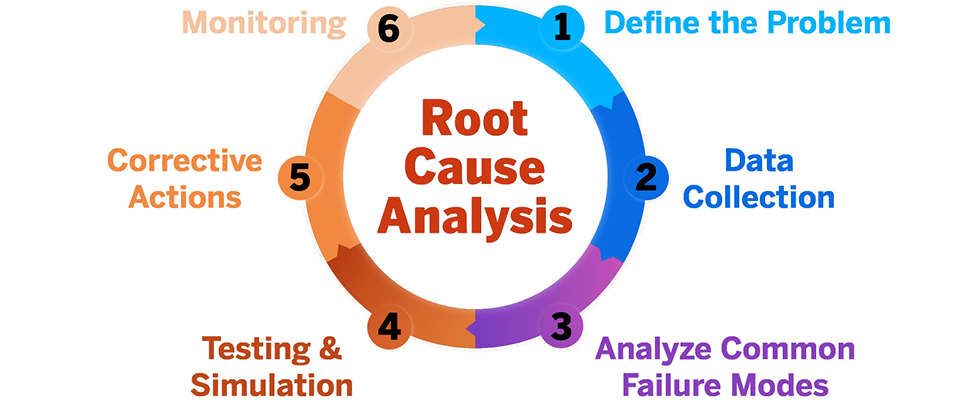
The global market for rotating equipment exceeds $100 billion1, with 60% of this spend dedicated to pumps and 40% to compressors. Approximately 10% of the total cost is committed to procuring equipment, while more than 80% of total life cycle cost is consumed by operating and maintenance expenses.
For these and other reasons, it is critical to run hydraulic equipment at its best efficiency point (BEP). It is also recommended to leverage today’s latest condition monitoring capabilities to streamline maintenance and to establish trends that can facilitate predictive maintenance.
The BEP for rotating equipment is a point on the curve where hydraulic efficiency is highest and pumps or compressors achieve maximum hydraulic efficiency with minimum energy loss. At BEP, energy input is best converted into useful output, such as flow, pressure or head. When a centrifugal pump or compressor operates at BEP, flow rate, head/pressure and power consumption are ideally balanced, hydraulic losses and vibration are minimized and the impeller avoids cavitation. Operating at BEP also reduces wear, ensures longer equipment life, lowers energy consumption and minimizes the risk of mechanical failure.
When rotating equipment drops below BEP, there is a greater risk of recirculation, vibration or overheating. Running equipment above BEP brings risks of cavitation, excessive power draw and mechanical stress.
There are several ways to ensure that hydraulic equipment is operating at BEP. Monitoring capabilities are readily available to measure flow, pressure, temperature, vibration and other metrics. Data analysis and diagnostic tools can also be leveraged to compare current and historical performance. This enables operators and maintenance personnel to establish trends for rotating equipment. If a deviation in performance is observed, it is important to identify the source of the issue and take quick steps to address it before it can escalate. Root cause analysis (RCA) is a helpful process to prevent issues from recurring.
RCA for rotating equipment looks beyond symptoms and seeks to understand the underlying reasons for equipment failure or underperformance. The goal of RCA is to prevent recurrence by addressing the source of the problem.
When it comes to pumps, the first step in RCA is to clearly define the problem—such as excessive vibration, bearing failure, seal leakage, reduced flow or head or unusual noise or temperature increases. Data collection provides evidence to document failure history and to establish historical trends for flow, pressure, temperature, vibration and power consumption. In order to determine how a failure has occurred, it is important to analyze common failure modes, looking for any misalignment or imbalances, lubrication issues, cavitation or overheating. It is also important to identify fatigue, wear or any manufacturing defects on critical parts. Testing and simulation are important steps to verify the identification of a root cause.
With these steps completed, corrective actions can be taken, such as improving alignment procedures, upgrading lubrication systems, replacing parts (or upgrading aging components), training operators and updating operating parameters. Post-repair inspections can be supported by monitoring programs that deliver feedback (and peace of mind) that equipment is functioning as it should.
Monitoring capabilities for hydraulic equipment are evolving. They give operators and maintenance personnel greater insight into the health of their equipment. A wide range of sensors (for temperature, pressure, vibration, etc.) are available to collect data. These connected sensors can transmit data to cloud-based systems via Bluetooth and Wi-Fi, or they can transmit to on-premise systems via highly secure and proprietary protocols.
Once the data is shared, it can be analyzed in real-time by rules-based systems that can trigger alerts when parameters are exceeded. Data can also be interpreted by machine-learning software that can analyze anomalies and establish long-term trends for each pump or compressor operating in a plant.
Monitoring tools are also becoming more mobile-friendly, with intuitive dashboards that bring operational status and anomalies to an operator’s phone. Monitoring and analysis capabilities are not just about creating reports—they also enable action to be taken immediately, from simple items like triggering a maintenance ticket (if a threshold has been exceeded) to automatically shutting down a pump (and activating a backup) when signs of overheating or other critical parameters have been breached.
Today’s data provides greater awareness that improves the best practices operators use to keep rotating equipment optimized. These best practices include items such as:
- Rerates: When process conditions change, hydraulic rerates should be done to bring equipment back to BEP. Some rerates can provide 30% additional head, with up to 10% power savings.
- Seal replacements: Modifications to seal housings can improve fluid flow-through and seal life.
- Bearing frame upgrades: Power-end replacements enhance reliability and ensure compliance with current American Petroleum Institute (API) requirements.
- Site surveys: These can be a quick and easy way to replenish spare parts inventories. Field service engineers often bring unique insights to troubleshooting “bad-actor” pumps or compressors. They can provide startup assistance with new and repaired units, and they can recommend upgrade options for items such as impellers, gearboxes or inlet guide vanes (for compressors).
All of these health checks reduce the time it takes to return rotating equipment to BEP. They also add years of service life to equipment, which helps to defer or eliminate the costs of installing a new pump or compressor. But the key to successful upgrades often lies in the quality of the parts used. Precise tolerances are key to the performance of rotating equipment. Even the smallest variance can generate inefficiencies within a process flow. Using non-OEM components can increase the risk of equipment failure, but these risks can be avoided by using genuine OEM parts.
Ensuring that rotating equipment operates at BEP is the first step in minimizing energy costs and increasing mean time between maintenance (MBTM) intervals. RCA is a helpful process to ensure that problems do not recur. Monitoring capabilities for rotating equipment have increased significantly, as have the machine learning analysis tools that help operators optimize their equipment. Rerates, upgrades and part replacements (with genuine OEM parts) can add years of service onto rotating equipment. All of these items seek to lower operating costs, decrease maintenance costs and ultimately, increase plant uptime—which is the true measure of all optimization efforts.
References
- Mordor Intelligence Report and Global Industry Analysts, Inc. USA