The costs associated with replacing and upgrading older pumps in vintage power plants and process facilities have often been an obstacle for life extension programs or service change projects such as going for low sulfur fuel oils. However, when regulatory and operational demands make new construction hard to economically justify, it may be the only way to go. When analyzing the total costs for upgrading and/or renewing pump installations, the pump component itself is not the roadblock but merely the modification of piping and foundations including installation and commissioning. These costs have shown a significant increase due to absence of skilled labor and the necessity to rely on third-party installation and service contractors. It is especially challenging when the original pump is no longer available and replacement parts become excessively expensive with long lead times. The original manufacturer could have ceased production of a certain model and replaced it with a new one that does not fit the existing footprint. Also, the manufacturer could have been acquired or reorganized and nobody knows how to trace the original pump.
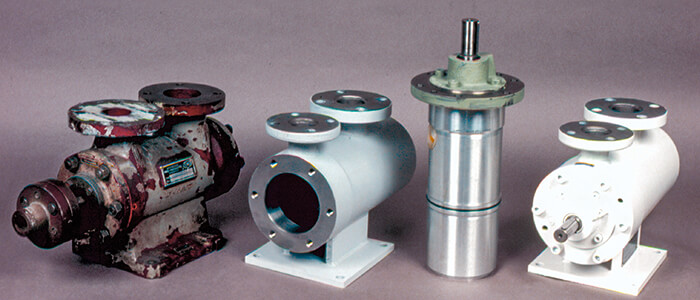

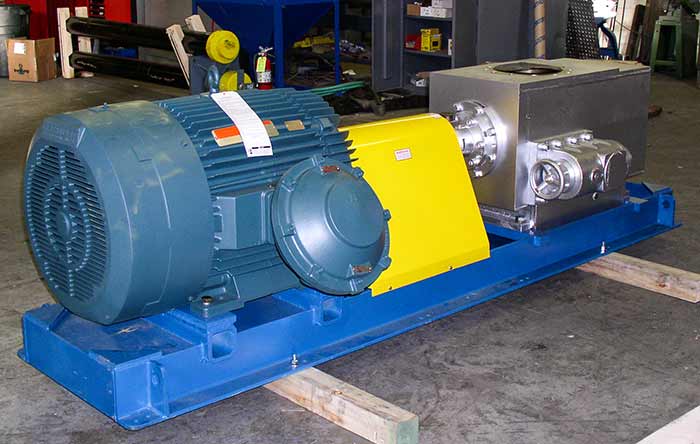
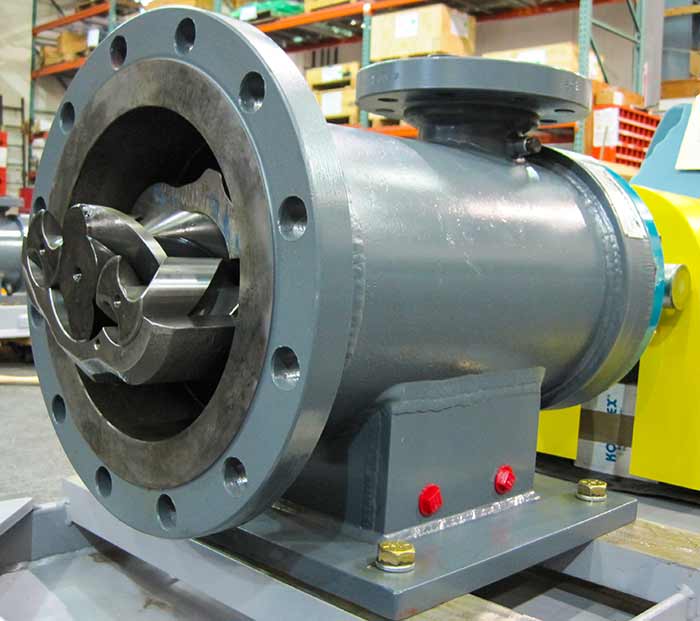