Extra precautions are needed in combustible environments such as grain handling and processing facilities.
Siemens Motors
06/08/2018
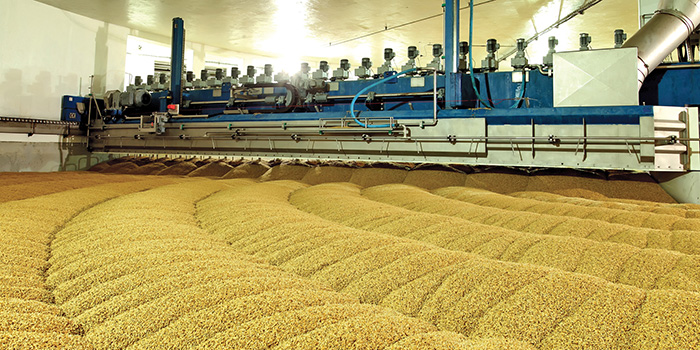
Understanding Dust Explosions
According to the Occupational Safety and Health Administration (OSHA), five elements must be present for a dust explosion to occur. These elements, which make up what is formally known as the “Dust Explosion Pentagon,” include³:- oxygen
- an ignition source (i.e., heat)
- a fuel source
- dispersion of dust particles in sufficient quantity and concentration
- confinement
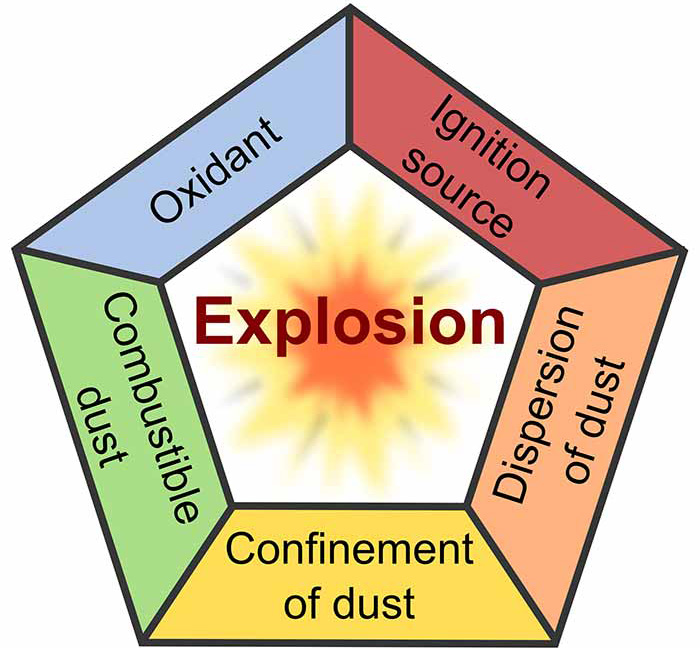
Classifying Hazardous Locations
A hazardous location is defined as “any area where fire or explosion hazards may exist due to flammable gases or vapors, flammable liquids, combustible dust or ignitable fibers or flyings.”⁴ Whenever an electric motor is to be installed in a location that meets the above description, it is the responsibility of the end user to ensure that it is qualified for operation given the level of risk posed by its surrounding environment. Even for experienced professionals, this can be a difficult task that requires a firm understanding of how to classify hazardous locations. In the U.S., classifications are defined by the National Fire Protection Association (NFPA) 70: National Electric Code (NEC), which designates locations according to Class, Group and Division.- Class I—Class I covers gases, vapors and liquids that are explosive or pose a threat as ignitable mixtures. Facilities and environments where Class I locations can typically be found include but are not limited to ethanol and petroleum refineries, spray finishing areas, gas plants and gasoline storage or dispensing areas.
- Class II—Class II covers electrically conductive metallic and nonmetallic dusts. This classification exists when combustible dust in the air is in sufficient concentration to be explosive or ignitable. Some examples of Class II locations include but are not limited to grain elevators, flour and feed mills and starch production plants.
- Class III—Class III covers easily ignitable fibers and combustible flyings. These materials are often heavier and settle more rapidly than fine particles, but they are flammable and have the potential to create hazardous conditions when in close proximity to electrical equipment. These locations do not normally require hazardous location motors. Some common Class III locations include textile mills, flax processing plants and any facilities where high quantities of sawdust are present.
- Group—Class I and II locations are further divided into groups, which are based on how the hazardous material behaves after it has been ignited. Class I locations encompass Groups A, B, C and D. Groups E, F and G fall under Class II areas. Acetylene is the only substance in Group A. Ethanol is designated Class I, Group D, while corn, wheat, wheat flour, soy and sugar are designated as Class II, Group G.
- Division—Hazardous locations are broken down further into Division 1 and Division 2. Division 1 environments exist when ignitable substances are likely to be present during normal operations. Division 2 environments exist when combustible materials are handled and/or stored in a manner that allows the substance to escape in the event of spill or failure of containment. As a simple rule of thumb, all Class I and Class II motors meet Division I requirements, which means they can be installed in both Division 1 and Division 2 locations.
Hazardous Location Temperature Codes
After a hazardous location has been classified, the next piece of information that is needed to determine if a motor is qualified is its temperature code (i.e., T-code). All motors manufactured after February 1975 possess a T-code designation, which is often listed on the nameplate. The T-code informs installing personnel of the maximum absolute motor surface temperature (i.e., skin temperature) that will develop when the motor is in operation. This includes its temperature under normal and abnormal operating conditions, including during overload and burnout. For the electric motor to be qualified for a location, its T-code must correlate with the autoignition temperature (AIT) of the substances that are present in the operating environment. In simple terms, AIT is the minimum temperature at which a substance can ignite. Take, for example, a Class II, Division 1 location where wheat flour is present. Wheat flour is a Group G material and has an AIT of approximately 716 F. For a motor to be used in this environment, it must have a T-code rating of at least T2, which correlates with a maximum motor surface temperature of 572 F. Use of a motor with a T1 designation, which correlates with a maximum motor surface temperature of 842 F, introduces the risk of combustion if the wheat flour comes in contact with the motor enclosure. While AIT values for most substances can be found in literature, they do not always translate to the operating environment. This is primarily due to the fact that AIT can change depending on atmospheric variables. Additionally, many hazardous location environments contain a mixture of different substances, which makes determining AIT virtually impossible. In these situations, it is common practice to use the lowest AIT of all the known substances. In every case, published AIT values should serve as a useful aid for hazardous duty motor selection and not a defining parameter.Considerations for Variable Frequency Drives
In recent decades, the use of electric motors operated with variable frequency drives (VFDs) has increased substantially. These systems offer higher efficiencies and enable better control; however, they also pose an added risk in the presence of combustible materials due to potential excessive heating. Operating motors with VFDs contributes to heat rise on the surface of the motor in two ways. First, since most motors in grain facilities are totally enclosed fan cooled (TEFC) motors, the fan that cools the motor is attached to the shaft of the motor and turns at the same speed as the output shaft of the motor. When the motor is operated at slow speeds, there could be insufficient airflow over the motor, and the motor surface could get too hot. Second, the electrical wave from most VFDs is not a smooth sine wave. It is a pulse width modulated wave form that switches voltage on and off thousands of times per second to approximate a sine wave of varying frequency to change the speed of the motor (hence the name). This rapid cycling of the voltage onto the motor windings, which is electrically an inductor, causes voltage spikes much higher than the line voltage. These spikes cause the windings to heat up. Inverter-duty motors are designed and built to withstand the higher voltage spikes produced by VFDs and can run at slow speeds without overheating and are labeled accordingly. Many electric motors in use today are marked as “inverter duty.” However, this does not necessarily mean that the motor has been certified for use with a VFD in a hazardous location by a third-party like the Federal Motor Carrier Safety Administration (CSA) or Underwriters Laboratory (UL). Putting a noncertified motor into a VFD application can cause a temperature rise that is outside the limits of the T-code rating for the location. As a result, motors must include labeling that indicates they can be used with VFDs. They must also be operated within the speed limits specified on the labeling. Some motors may be approved for use in hazardous locations and have VFD ratings on the nameplate but still not be certified to do both (variable speed and hazardous location). Operating these motors with a VFD may void the hazardous location certification. Bottom line: be certain the motor shows certification for the location and the VFD ratings (CT or VT).Explosion-Proof and Ignition-Proof Motors
Motors designed for use in Class I, Division 1 environments must be labeled as “explosion proof.” A misconception regarding “explosion-proof” motors is that they are designed to prevent an explosion. This is not accurate—these motors are built to simply contain an explosion internally without rupturing. This is achieved through a number of different design measures, one of which includes using high-strength materials for both the motor hardware and its enclosure. Additionally, in the event of ignition and pressure buildup inside the casing, explosion-proof motors must be able to sufficiently cool hot gases as they escape through long, tight passageways known as flame paths. This reduces the temperature of gas to a value that is less than the AIT of the atmosphere so that ignition cannot occur. Another common misconception with hazardous duty motors is that Class I, explosion-proof motors will always satisfy Class II requirements. However, the design principles behind the two types of motors focus on the prevention of entirely different scenarios. A Class II motor’s design, for instance, assumes that eventually, as the motor takes in air from the surrounding atmosphere, its internal temperature will equalize with the operating environment. As a result, an internal fault can cause an explosion, which (ideally) will be contained. The design of a Class I motor, on the other hand, focuses on keeping the motor’s skin temperature below the AIT of the surrounding atmosphere. This type of motor is often referred to as “dust ignition-proof.” For both Class I, Division 2 and Class II, Division 2 locations, the use of dust ignition-proof motors is permissible, but it is not mandatory. Overall, it is important for operators and facility managers to understand that all explosion- and dust ignition-proof motors are not created equal. For instance, two motors may include the same explosion-proof rating, but it does not mean they are identical (or even similar). As a result, operators should approach hazardous duty motor selection comprehensively by examining the unique design and construction of the motor. This should include consideration of elements such as ingress protection (is the motor IP65 vs. IP56), preventative flame paths, ruggedness of components, etc. Since a hazardous duty motor is a critical safety investment, installing a product that simply meets the minimum requirements for “explosion-proof” is not a sound strategy.Simplifying Hazardous Duty Motor Selection
Even with a grasp on the principles of motor design and hazardous location classifications, it is easy to see how an error can be made when selecting a motor for use in a combustible environment. Because such an error can have wide-ranging impacts—from lost production to fines to worker fatalities—facilities will often go to great lengths to ensure that their motors are qualified for specific environments. Some facilities will go so far as to segregate and label motor inventory. Others color code motors so that installers have visual verification of location approvals. Both of these methods are cost prohibitive, particularly in larger facilities, since they often result in the need for a large amount of excess inventory. Stocking multiple motors with the same power and speed rating but different location approvals ultimately increases the likelihood of human error and introduces added complexity to motor selection. To eliminate these issues, many industrial facilities have turned to standardization as a means of ensuring that motors are qualified for use in hazardous locations. In such cases, the facility stocks one single motor that is rated for all possible environments. Motors designed to keep all dust out of the motor are a good idea, as are those that meet or exceed National Electrical Manufacturers Association (NEMA) premium efficiency levels and the efficiency requirements of the U.S. Department of Energy. It is also important that motors are suitable for processes in a wide range of facilities—from storage and transport of grains, to distilling ethanol, DOL or in constant or variable torque applications on drives. Aside from ensuring safety, which should be the top priority in hazardous duty motor selection, specifying a single model motor for an entire facility enables optimization of inventory. In many cases, savings generated by eliminating excess inventory can offset the higher cost associated with purchasing a motor that is “over-designed” for its location. Additionally, standardization allows electricians and plant personnel to better familiarize themselves with a single product, leading to quicker installations and streamlined maintenance.Standardization Helps Ensure Safety
In facilities where combustible dusts are handled or stored, the misapplication of electric motors can have repercussions. Unfortunately, mitigating the risk associated with this common problem is something that requires both a firm understanding of hazardous location classifications and the principles of motor design. In some facilities, this depth of expertise simply does not exist. The responsibility of motor selection is passed down the line, which increases the likelihood that an error will be made. Standardization has emerged as a cost-effective method of simplifying this arduous task, providing facility managers with assurance that their operations are safe, efficient and in compliance with applicable regulations. References- Cowell, B., (2016, June 6). Grain Dust Explosions Explained. Agri-City Insurance.
- Vallero, D., Letcher, T. (2013). Unraveling Environmental Disasters. Elsevier.
- Combustible Dust in Industry: Preventing and Mitigating the Effects of Fire and Explosions. (2014, November 12). Occupational Safety and Health Administration (OSHA).
- Hazardous Classifed Locations. Workplace Safety Awareness Council. Occupational Safety and Health Administration (OSHA).