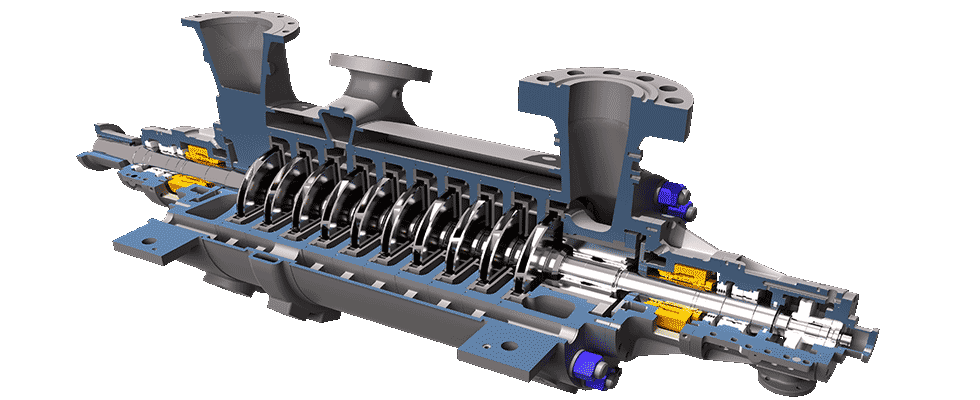
A manufacturer that produces pumps in power generation has supplied the main pumps for the first two combined cycle power plants (CCPPs) equipped with last-generation gas turbines in Italy, and a third supply is underway.
The first CCPP will have a total electricity generation capacity of 780 megawatts (MW) and an energy performance of 63%. This will translate into a 40% reduction of specific carbon emissions compared to the average of the current Italian thermoelectric installed base and a more than 70% reduction of emissions of nitrogen oxides (NOX).
The OEM was asked by both the end user and turbine supplier to get involved in the project during the concept and design phase to contribute to the definition of the requirements of the main pumps. The supply related to the new high-pressure boiler feed water pumps (American Petroleum Institute [API] 610 BB4 type) was the most challenging from a technological standpoint. A pump matching the stringent requirements of the latest generation H-Class gas turbine was custom-developed, making use of finite element method (FEM) and computational fluid dynamics (CFD) analysis. FEM analysis of the pump and baseplate allowed the optimization of the dynamic behavior of the skid within the full design speed range. FEM analysis also contributed to designing casings and tie bolts for the worst operating conditions in terms of temperatures and pressures. Impellers, diffusers and casings were developed through a CFD analysis and in-house prototype testing. The pump skid was developed with customized auxiliary equipment with a mechanical variable speed coupling allowing speed variation from 25% to 100% of the nominal speed with a high level of reliability. The mechanical seals were also coupled with an API Plan 23 System. The supply was validated through high-temperature testing.
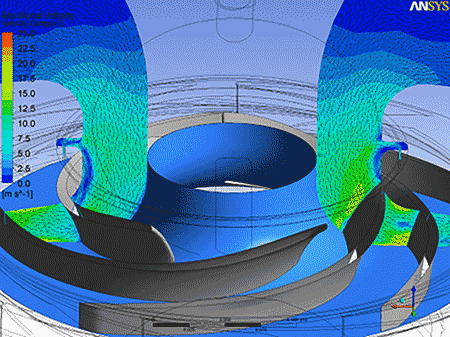
Preparing for the Clean Plants of the Future
The International Thermonuclear Experimental Reactor (ITER) is a project that aims to build and test the world’s largest tokamak, a magnetic fusion device designed to prove the feasibility of fusion as a large-scale and carbon-free source of energy based on the same principle that powers the sun and stars.
Power plants generate electricity by converting mechanical power, such as the rotation of a turbine, into electrical power. In a coal-fired steam station, coal combustion turns water into steam and the steam drives turbine generators to produce electricity. Just like a conventional power plant, a fusion power plant will use the heat from the energy generated through the fusion of atoms inside a tokamak to produce steam and then electricity through turbines and generators.
The between bearings radially split pump (API 610 BB2-type) for the refrigerating system of the plant was designed according to the required American Society of Mechanical Engineers (ASME) Boiler & Pressure Vessel Code, Section VIII, Division 2, Part 5. This adheres to the stringent design by analysis requirements related to safety and structural resistance, such as protection against plastic collapse, local failure and collapse from buckling and failure from cyclic loading.
There were three possible alternative analysis methods to evaluate the pump design: elastic stress analysis, limit load and elastic plastic stress analysis. The elastic plastic stress analysis method was chosen as the safest and most advanced approach. The nonlinear plastic behavior of the pump’s constitutive materials was included in the numerical model, and a contact analysis was also performed to ensure that no leakage should occur during testing/operating conditions. The pump’s behavior was analyzed with a nonlinear, thermo-structural decoupled analysis to include the influence of both structural and thermal loads. All the analyses confirmed the pump fulfilled all the necessary requirements and was adequate to withstand the severe test and operating conditions of ITER’s refrigerating system.
References
iter.org