"We knew our biggest problem was [our] lift stations, we just didn't know exactly what to do about it." The words of Jon Brown, sewer system supervisor for Idaho’s Fremont County Public Works Department, no doubt resonates with many of his peers. Lift stations—or pump stations—operate as critical components in a collection system as they keep water flowing. For Brown and his staff, a litany of issues gradually emerged over time as their collection system expanded, including the number of lift stations. The county operates a wastewater collection system in the Island Park region of rural Idaho, near Yellowstone National Park. The area is made up of a vast expanse of accessible forest comprised of private and public lands. Because the region is a popular vacation destination for outdoor enthusiasts, many of the county’s lift stations operate in forested locales and other remote areas only accessible by off-road-type vehicles. A network of 47 lift stations conveys more than 175,000 gallons per day to two treatment plants. Despite being spread over an actual area of more than 24 square miles, only five public works technicians cover the entirety of the wastewater system including the treatment plants. Therefore, conducting preventative operation and maintenance (O&M) or emergency repairs for lift stations became both time-consuming and difficult.
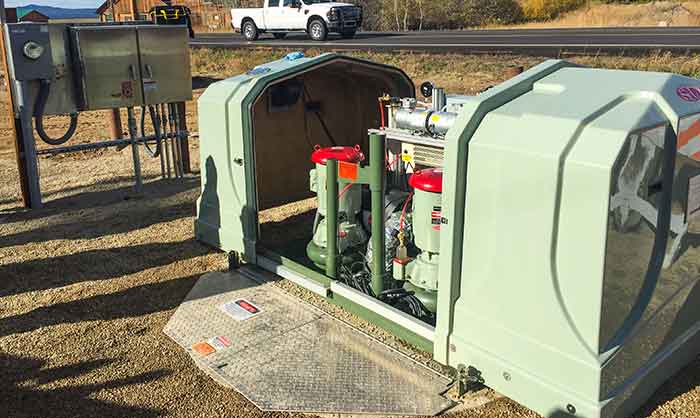
Developing Tiers & Templates
The county contacted consulting engineering firm Keller Associates to seek solutions to improve operational efficiency. Keller Associates proposed a tiered standardization program that would reduce the number of lift station types and manufacturer brands to three standard types based on size and capacity: (1) shallow, household-type pumping systems with less than 5-horsepower (hp) motors; (2) mid-range lift stations with 5- to 50-hp motors; and (3) large regional and/or influent lift stations with 50-hp motors or larger and typically deeper wet wells. Fremont County selected preferred manufacturers based on extensive experience with a variety of systems: a grinder pump manufacturer was selected for the small household pumping systems; a packaged above-ground pump stations manufacturer for the mid-range lift stations; and a submersible manufacturer for the large lift stations.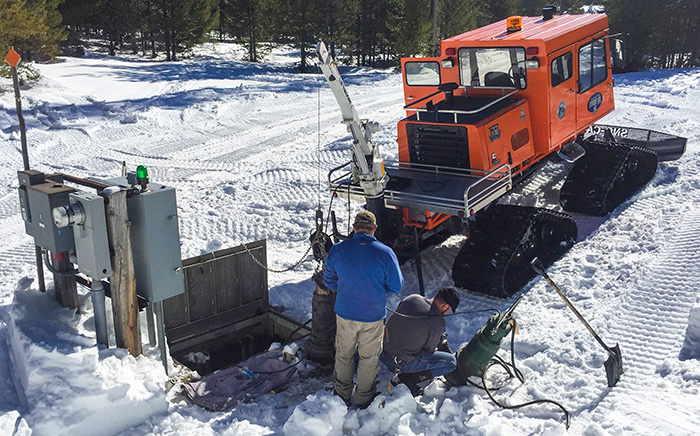