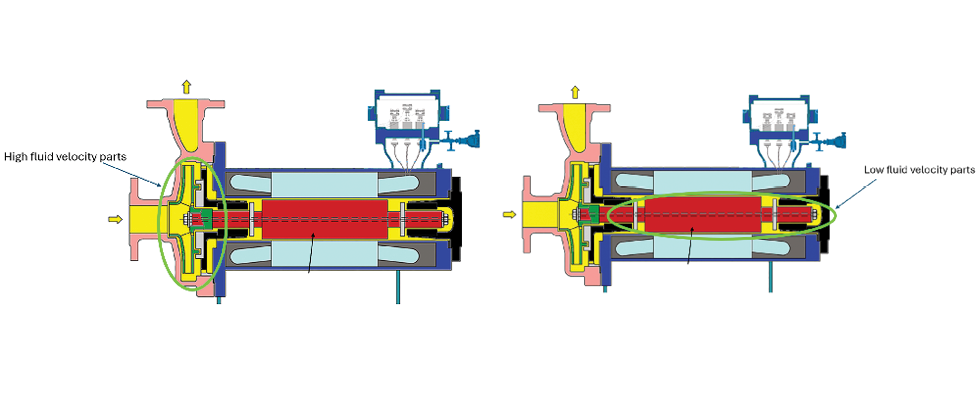
The chemical industry is full of corrosive and hazardous chemicals. While vital to the industries they serve, they can create challenges for the pumps that handle them. The more corrosive a process fluid is, the more it will wear on the mechanical parts it encounters. This increases the frequency of maintenance and cost of ownership and can even create a safety hazard. For these reasons, it is critical to inform manufacturers of the characteristics of the specific fluid to ensure proper material selection for the pump.
This article will highlight critical aspects of fluid that affect its corrosivity, describing how these factors affect material selection and evaluating scenarios to demonstrate the importance of these fluid aspects. This evaluation will be done in the context of a canned motor pump.
The first thing to know is what the fluid is. This one may seem obvious but is often overlooked, as some fluids are far more corrosive than others (for example, if users are pumping water, they will not need to invest in the same materials as if they were pumping hydrochloric acid). The second thing to know is whether or not there are solids present in the fluid, as these can increase the corrosion rate. The third consideration is the fluid concentration. This parameter has a massive effect on corrosivity. Again, take hydrochloric acid for example. One hundred percent hydrochloric acid can be much less corrosive than 36% hydrochloric acid due to the higher rate of reaction observed in lower concentrations. The fourth and final consideration is fluid temperature. Different temperatures can drastically vary the rate of reaction within a fluid and can increase the rate of corrosion. Understanding these characteristics and communicating them to the manufacturer will ensure users get the right canned motor pump for their application and do not invest in any unnecessary materials. Three examples that encompass the potential range of corrosivity are shown in Table 1.
Once these parameters have been established, the end user can hand the baton off to the manufacturer, who must now make some critical material selections. The most intensive selection will be the “wet end” parts. The wet end of a canned motor pump consists of parts that are engulfed in the process fluid. Certain wet end parts will have a higher corrosion rate than others due to the fluid velocity they encounter (such as the impeller, as it is the component imparting rotational energy into the fluid and will see a higher fluid velocity than the bearings and the rotor). The wet end material selection is the most intensive, as it will change based on the process fluid’s corrosivity.
One other critical selection manufacturers must make is the “can.” The can is the primary pressure boundary that contains the process fluid. It needs to be strong enough to retain the fluid at operating pressure while allowing electromagnetic field transmission from the stator into the rotor. The electromagnetic field developed in the stator and transmitting to the rotor is how all induction motors rotate. For these reasons, an extremely robust and corrosion-resistant nickel-chromium-molybdenum alloy (also known as alloy C-276) is often the material of choice for this part. While highly critical, this is not as intensive of a selection since in most cases, the same material is used.
Now that what the end user needs to know about their fluid and why the manufacturer needs this information has been established, it is time to utilize the fluids in Table 1 to outline real-life examples. The first example is water at ambient temperature (75 F) and no solids present. This is a fluid with minimal corrosive properties and allows for many possible wet end materials to be selected. The most common selection in a canned motor pump would be 304 stainless steel, which is a durable yet economic metal. Some manufacturers may even suggest plastics like nitrile or polypropylene. As mentioned previously, the can would be made of alloy C-276, which comes standard in most canned motor pumps regardless of the corrosivity of the fluid.
The next example is 100% anhydrous hydrochloric acid with a wide temperature range (-18 F to 68 F). Hydrochloric acid itself is a corrosive fluid, so some anticorrosive measures must be taken in the selection. However, because the concentration is so high and the temperature is relatively low, its corrosivity is low enough where 316 SS is a good solution for corrosion resistance.
The most corrosive fluid mentioned in Table 1 is 37% hydrochloric acid at 200 F. This is a highly corrosive fluid at a low concentration and a high temperature; therefore, a very robust material selection must be made. Against most alloys, a fluid like this has a twofold effect. The high temperature hydrochloric acid eats through the anticorrosive metals, which then introduces the other metals to further corrosion from water.
It is difficult to find a standard metal with the necessary anticorrosion properties to fit this application. The manufacturer will likely resort to a specialty material with highly anticorrosive properties like zirconium. In this case, to protect the motor’s materials, a clean water flush circulation plan was opted for to prevent damage to the alloy C-276 can and bearing material. These applications will require more costly materials, but this is necessary to ensure performance and safety with the pump.
Material selection can seem complicated, but it is an important thing to get right to maximize pump performance. For end users, their job may be simple, but it is the most important. Know the application and communicate it well to the manufacturer. If this step is not done correctly and fluid properties are misrepresented, then the pump design will be incorrect out of the gate.
As a manufacturer, it is important to understand the needs of the users’ applications and to know how they interact with available materials. It is critical to ensure selections can endure the worst-case scenario for the application but are designed with cost in mind.