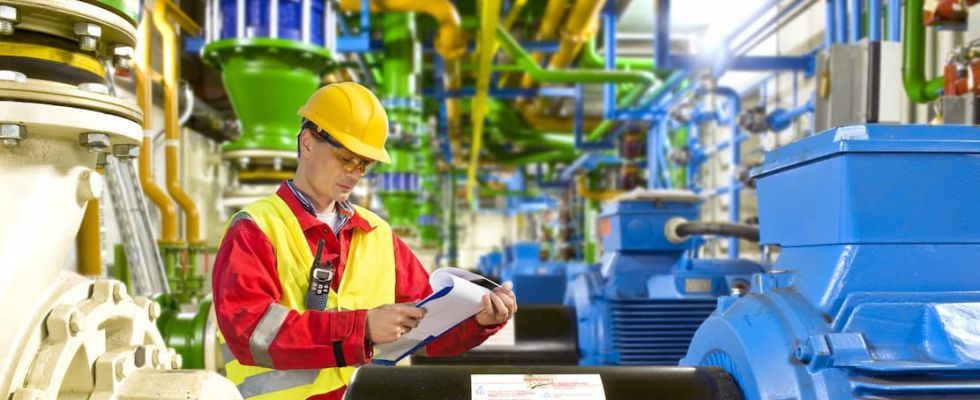
There has been a long-held belief that plastic-based goods are cheaper to import than manufacture locally. But a recent study from Shale Crescent USA dispels that. It revealed that the low-cost gas and natural gas liquids flowing from the U.S. shale gas revolution have the potential to turn the $53 billion U.S. plastics importing industry on its head.
In his State of the Union address, President Joe Biden touted the growth of the manufacturing sector under his administration, noting “too many good-paying manufacturing jobs moved overseas” in recent years. He asked: “Where is it written that America can’t lead the world in manufacturing again?”
The Midwest and Northeast are uniquely positioned to fuel further growth in U.S. manufacturing. Of the $53 billion in imports, nearly half originate in Asia, with China alone accounting for $25 billion, according to Nathan Lord, President of Shale Crescent USA, a nonprofit research, economic development and marketing organization focused on creating jobs by promoting the abundant natural resources available in Ohio, Pennsylvania, and West Virginia.
“Since the COVID-19 pandemic spotlighted the financial benefits of shorter supply chains, Ohio has surpassed China as the world’s low-cost center for plastics manufacturing, thanks to advantages in cost, economic climate, and market access,” Lord says.
“From a transportation standpoint, a standard container of finished goods originating in China will travel anywhere from 6,500 to 20,000 nautical miles to reach a U.S. port before being processed for national distribution.”
The pandemic showed how dependent we were on China for essential products. U.S. companies responded. Companies aren’t coming here just to be patriotic or to help consumers. We are seeing reshoring of manufacturing. Companies are moving production to or increasing production in the U.S. Why?
Cost Efficiency in Production & Labor
No longer known as the Rust Belt, the Ohio River Valley states of Ohio, Pennsylvania and West Virginia form a region that is unique for manufacturers. It is the only place in the world at scale where a company can build on top of its energy and feedstock and in the middle of its customers, thus eliminating unnecessary transportation.
Ohio businesses and manufacturing facilities are located within a day’s drive of 50% of the U.S. population and over 70% of the end-to-end plastics industry supply chain. That same radius also captures over one-third of the country’s natural gas production, creating substantial environmental advantages by eliminating the need for lengthy, fragile global supply chains and their associated greenhouse gas emissions.
The Shale Crescent USA study also found that forces of supply and demand are positioned to positively impact U.S. resin prices. The U.S. is a net exporter of polyethylene and China is a net importer. The U.S. uses low-cost natural gas to produce resin while China uses more expensive oil-based Naphtha.
“More than 80% of polyethylene production costs are dependent on the type of feedstock and energy used,” says Joe Eddy, a co-author of the study and executive committee member for Shale Crescent USA. “The study revealed that U.S. resin producers experience greater margins and higher overall profits compared to overseas producers.”
Ohio, West Virginia, and Pennsylvania combined (the region comprising Shale Crescent USA) now produce over one-third of U.S. natural gas supply and over one and a half times more natural gas and natural gas liquids than the entire country of China.
“China is energy deficient and is reliant on global supply chains to either import plastic resin or produce resin from much costlier oil-based Naphtha,” Lord says.
The study shows that in addition to these significant cost drivers, Ohio also holds an edge on China in terms of average electricity rates (35% lower) and manufacturing lease rates (28% lower).
“These fundamental advantages are expected to remain intact for decades as they position Ohio to capture a significant share of the $25 billion worth of plastic products currently imported from China annually,” Lord says.
Another revealing aspect of the study is Ohio’s advantage in the realm of workforce demands and labor rates. There has been a tenfold increase in China’s manufacturing wages over the past 25 years and China’s manufacturing industry averages annual wage rate increases of 10 percent. By contrast, increased automation and productivity enhancements in the U.S. decreased labor cost inputs and eroded China’s historical labor cost advantage. Meanwhile, Ohio was recently ranked as the No. 1 state in the U.S. for plastics employment by Plastics Industry Association, boasting 75,000-plus of the nearly 1 million plastics industry workers across the U.S.
What most countries don’t have is an abundant dependable fuel like natural gas available 24/7, 365 days a year that can come on line quickly. This is the USA’s greatest competitive advantage and why companies are interested in the USA. Companies are coming here and expanding here because it is more profitable.