Motor systems that are designed as entire packages are more reliable and affordable.
02/27/2015
Electric motor systems with variable frequency drives (VFDs) are becoming more common in large industrial systems because VFDs provide higher system efficiency, greater operational flexibility, improved reliability and lower carbon emissions capabilities. When the requirements and functionality of the drive system are well-defined, component design can be optimized to achieve the highest reliability and lowest cost of the entire system package. The total cost of system ownership can also be reduced when drive train components such as motors and VFDs are designed and sized to work together as systems.
What is Integrated Drive Systems Engineering?
A typical drive system is made up of a VFD, a motor, a coupling, the driven load and often a gear box. Some or all of these components may be mounted on a common foundation base. Each one has potential failure modes, and evaluating and designing the components to avoid faults can prevent system failures. For the cost optimization of system packages, the cost drivers of each component and their sub-components must be evaluated. Based on the relative cost differential between the components and the design parameters that influence them, the optimized sizing of components for the lowest cost and greatest reliability could be achieved for the system requirements. While each component is commonly called a product, the integration of these components can be referred to as an integrated drive system. However, if the products are not properly integrated into a system, effects may range from a delay in project startup to total system failure. The integration of components requires product, application and system level expertise.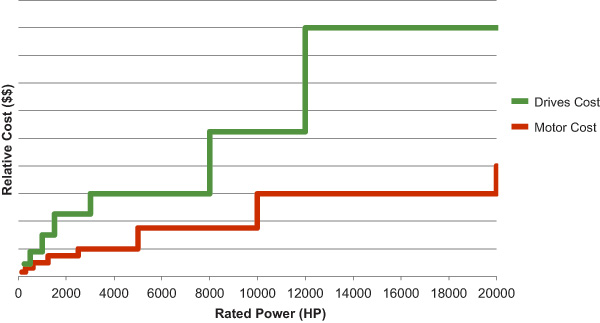
Benefits of Integrated Drive Systems Engineering
Total cost of ownership has two major parts: the initial product cost and the total operational cost during the life of the system. Creative integrated drive system engineering can substantially improve both of these parts. Figure 1 shows the variation of relative cost of motors and drives with power. Operators could reduce the overall system cost by lowering the cost of the more expensive component and allowing a minor increase in the cost of the less expensive component. The motor’s cost is normally power-limited. However, the drive’s cost is related to its voltage and current limits and not necessarily to its power output. In the common application of products over several power ranges, the cost per horsepower can be minimized when the ratings are at the maximum available potential for each component. As Figure 1 shows, the relative costs of motors and drives jump significantly at certain horsepower thresholds. This situation is common when producing somewhat standardized components with discrete frame brakes. However, optimization can also be harnessed when cost breakpoints are aligned with particular care. Significant cost benefits can be seen in the initial capital investment. This may be further applied to the driven load and the power system in the facility. To be more specific, Figure 1 shows that at certain cost breakpoints or power ratings, increasing the operating voltage becomes more advantageous. To illustrate this, consider an application where it is beneficial to look at the maximum output voltage and current capability of the drive when sizing the motor and drive together. By evaluating the total cost of the motor and drive together, their respective costs can be further minimized.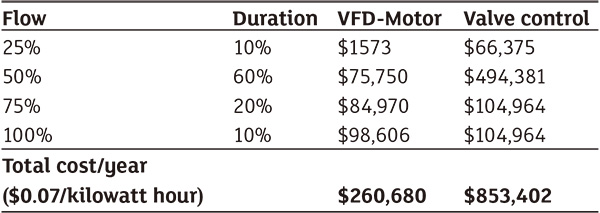