Increased cost, competitive prices, the demand for rapid project completion and highest quality, and safety requirements are affecting the development strategies for new products from suppliers in the oil and gas industry, as well as the petrochemical and power industries. In order to derive concrete action strategies for product development, the differing visions of customers and the various disciplines of the company’s own organization in the field of special machine and plant engineering must be understood. Customers—both original equipment manufacturers (OEMs) and end users—usually demand maximum flexibility with regard to equipment, short delivery times and low prices at maximum quality. Their suppliers strive for simplicity, cost reduction and optimized processes to achieve maximum profit with as few resources as possible. The supplier’s sales team represents the interface between the organization and customer and requires appropriate sales tools in order to make the products palatable to the customer.
Project vs. Process Machines
In principle, these products can be categorized as either project machines or process machines. Project machines fulfill the customer’s maximum requirements, leading to the highest level of customer satisfaction. In contrast, process machines can be processed in the supplier’s organization optimally within existing capacities and existing know-how, reducing costs and thereby increasing profits.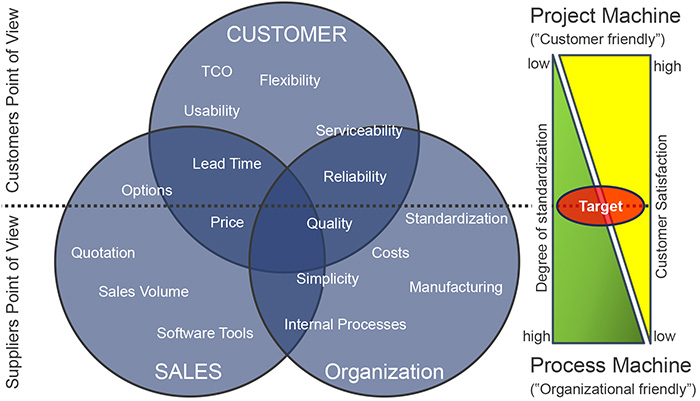
Gearbox Example
This gearbox is often used in the oil and gas industry as a variable speed drive for pumps and compressors and connects a constantly rotating electric motor to a working machine. An actuator is used for the variation of the rotational speed—in this case, adjustable pump vanes of a torque converter. The hydrodynamic geared variable speed drive combines a counter-rotational torque converter (a), with a mechanical planetary gear (b) and a parallel shaft gear (c). The geared variable speed drive connects a driving machine, such as an electric motor, and a working machine, such as a pump or a compressor.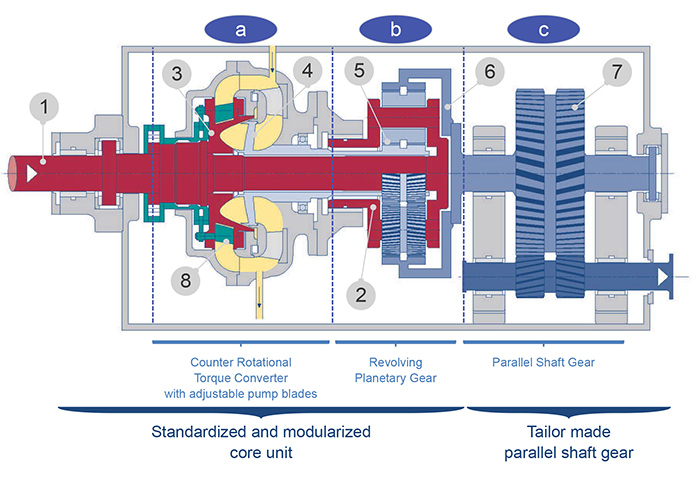
Advantages & Disadvantages
There is a strong trend towards standardization and modularization in industry, resulting in numerous advantages. The communication between suppliers, in the case of the hydrodynamic, speed-controlled power transmission, is a conglomerate of engineering, procurement and construction (EPC); OEM; end user; motor- and transmission-suppliers is clearly simplified. This can reduce errors and misunderstandings in order processing. Documents such as piping and instrumentation diagrams, installation plans, instrument lists, price lists and equipment standards can be standardized as well as computational documents, resulting in further advantages for feasibility studies in early project phases and the bidding process. Shortened delivery times and continually increasing price pressure force suppliers and customers to take appropriate measures.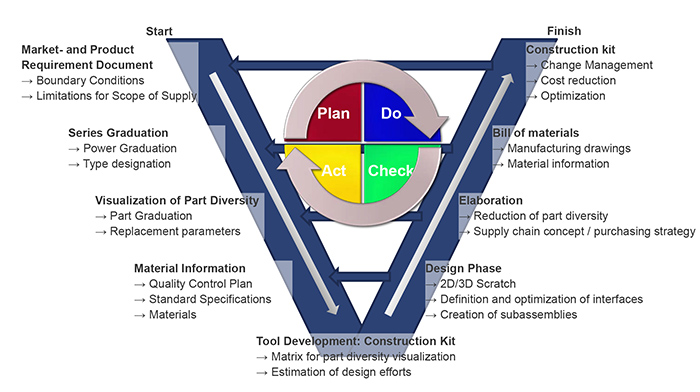