For decades, piston pumps have been used to meet a wide variety of transfer, extrusion, coating and dispensing requirements across many industrial and commercial applications. The versatility of piston pumps makes them a workhorse in everything from pressure washing, abrasive blasting, bonding, chemical dosing, potting, paint spraying, lubrication and pavement marking to sanitary dispensing, to name a few. With this versatility in mind, the fluid type and viscosity of the material being transferred—and the associated flow rate and output pressure for those materials—must be considered to ensure that the correct pump is selected for the application. A piston pump is classified as a reciprocating positive displacement pump that uses a piston or plunger to draw and move fluid through a sealed cylinder. The fluid inlet of the piston pump is often immersed directly into fluid, which is then drawn into the pump via negative pressure as the plunger reciprocates. The combination of check valve timing and plunger motion allows fluid to be dispensed on both the up and down stroke, delivering output pressures up to 15,000 per square inch (psi) and flow rates up to 60 gallons per minute (gpm).
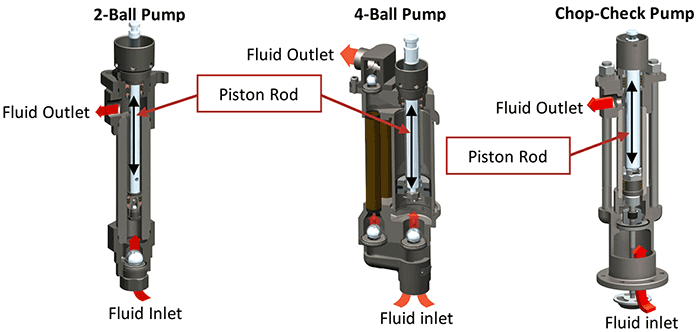
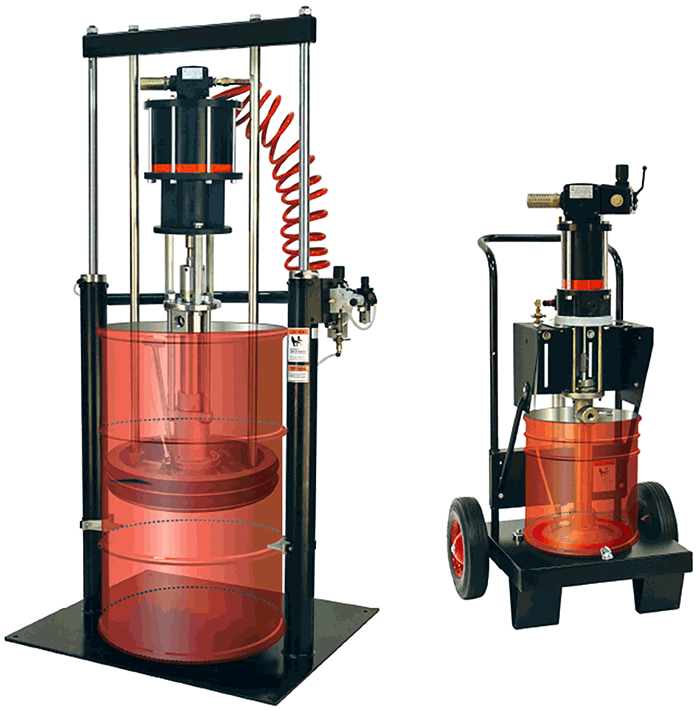
Application Pump Types
Multiple pump ends are available for piston pumps to successfully handle a range of fluid properties. These are called lower-ends and they are available in two-ball, four-ball and chop-check types. Two-ball and four-ball style piston pumps are designed for low- to medium- viscosity fluids typically found in transferring, washing and coating applications. For extrusion applications involving high-viscosity materials up to and beyond 1 million centipoises (CPS), both heavy-duty chop-check and two-ball pump packages can be used. Demanding extrusion tasks often require additional accessories such as a pneumatic ram assembly and a follower plate to provide additional force to move the fluid into the pump, thermal blankets to reduce material viscosity or fluid regulators to ensure accurate dispense control. Although there is a measure of capability crossover, each piston pump type has limits. It is advisable to consult the manufacturer or dealer when sizing or selecting a pump for a specific application.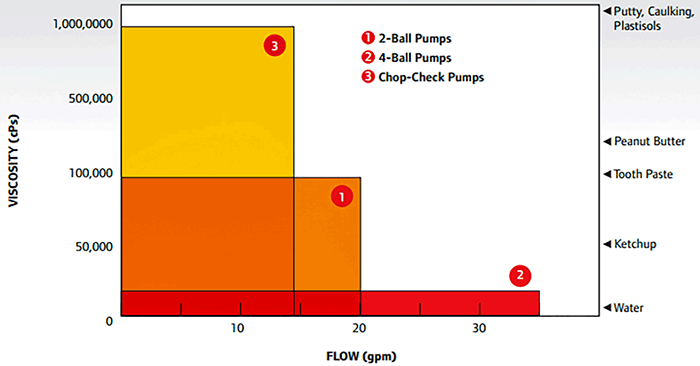
Handling Sticky Situations
When using a piston pump to transfer challenging media such as shear sensitive ultraviolet (UV) inks or adhesives with suspended solids, special tubes and plunger coatings and packing seal materials are used. These minimize shear and thermal energy, as well as provide resistance to any abrasion that can occur. A stainless steel pump combined with ceramic-coated cylinders and piston rods offer waterborne benefits and abrasion resistance for more endurance and reduced wear when working with harsh materials. All of these features combined help prevent premature pump failure. Understanding the fluid and the ultimate goal of the application is essential to maintaining product integrity. Some fluids require shear control or thermal assistance to get them to a viscosity at which they can be transferred easily while minimizing the risk of irreversible fluid damage. Shear-sensitive materials are diverse and cover everything from lotions and soaps to pastes, cornstarch, inks, some adhesives and certain paints. Such materials require low internal velocities and gentle pumping action to limit damage and maintain their properties during transfer applications. In the microelectronics industry, many sealing compounds include the addition of fillers for enhanced performance. This results in a mix of solid and viscous properties that can present challenges in effectively managing the application without damaging the pump or material.Piston Packages
With so many variables at play, application packages preconfigured with the right motor, piston pump, mount, controls and accessories offer operators the greatest flexibility. For end users, pre-assembled and validated application packages eliminate much of the guesswork that comes with choosing the right pump for the job. Challenging adhesives such as multiple component or glass-filled sealers require stainless or carbon steel piston package options with coated tubes and plunger rods to tackle difficult extrusion and transferring applications. When it comes to new or unique applications, it is recommended to refer to the pump manufacturer’s viscosity and chemical compatibility resources or consult with an expert to properly configure the package.What’s On the Inside Counts
The way a piston pump is designed and engineered impacts its functionality and performance when in use. With a simple motor design, universal valve blocks and pump connections, piston pump operators can easily move between motor sizes, create new pump ratios and even upgrade their system without buying a new pump. Other features include:- a progressive exhaust motor design to minimize icing
- adjustable packing seals and optional component coatings to improve pump life
- quick disassembly for easy maintenance
- thermal relief kits to prevent over pressurization