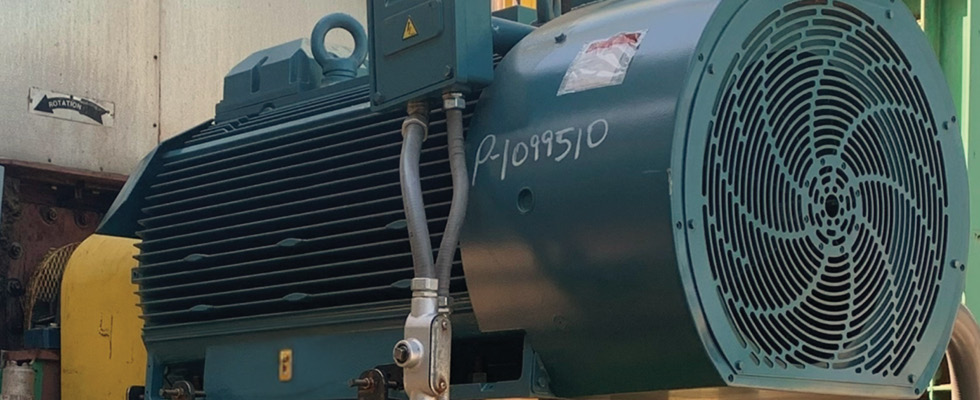
Large electric motors are essential in industrial operations. They power the pumps that move water and the conveyors that keep manufacturing lines in motion. While their mechanical output is easy to see, what often goes unnoticed is how efficiently they use energy.
In Part 101 of this series, we explored why energy efficiency in large motors is so important. From reducing operational costs to meeting environmental targets, the benefits are clear. Now, in 201, we turn our attention to the inner workings of these machines. What exactly makes a large motor energy efficient? And how can organizations ensure they are getting the most out of every motor?
Understanding Motor Efficiency
Motor efficiency tells us how well a motor turns electrical energy into mechanical energy. No motor is perfect—some energy is always lost as heat, noise or other effects. Energy-efficient motors are designed to reduce these losses as much as possible.
For large motors, even a small boost in efficiency can save energy and money. For example, improving the efficiency of a 600-horsepower motor by just 1% can save thousands of dollars each year.
The Role of Materials
One of the primary factors influencing motor efficiency is the quality of materials used in its construction. High-efficiency motors often utilize premium-grade electrical steel in both the stator and rotor cores. This advanced material reduces core losses—such as hysteresis and eddy current losses—by enhancing magnetic flux conduction. As a result, it minimizes thermal losses and improves overall energy efficiency within the motor.
Additionally, these motors utilize high-conductivity copper windings and rotor bars that are often larger in cross-sectional area and precision wound. This design minimizes electrical resistance and reduces I²R losses, which is the heat generated due to current flow through the winding and rotor conductors.
While these enhancements may increase the initial capital cost, they deliver long-term benefits through reduced energy consumption, lower operating costs and an extended motor lifespan.
Precision Engineering
Motor efficiency is influenced by material quality and manufacturing precision. High-efficiency motors are built with tighter mechanical tolerances and precise alignment of internal components. This reduces mechanical vibration and sound and ensures optimal electromagnetic performance.
A critical design parameter is the air gap—the narrow space between the stator and rotor. An oversized air gap reduces magnetic coupling and efficiency, while an undersized gap risks physical contact, leading to wear and energy loss. Precision engineering
ensures the air gap is maintained within optimal limits for maximum performance.
Thermal management is another essential factor. Efficient motors incorporate advanced cooling features, such as enlarged cooling fins and optimized airflow channels, to dissipate heat effectively. Improved heat dissipation not only enhances efficiency but also contributes to longer motor life and greater reliability under continuous operation.
Advanced Motor Designs
While traditional induction motors are still widely used, newer motor designs are pushing the boundaries of efficiency. One example is the permanent magnet synchronous motor (PMSM), which uses permanent magnets embedded in the rotor. These magnets create a constant magnetic field, which can eliminate the need for rotor current and reduce energy losses.
PMSMs are particularly effective in applications that require variable speed and/or high torque, such as pumps, fans, heating, ventilation and air conditioning (HVAC) systems and electric vehicles. Although they tend to be more expensive upfront, their efficiency and performance often justify the investment.
Variable Frequency Drives (VFDs)
One of the most impactful ways to improve motor efficiency is not in the motor itself but in how it is controlled. VFDs allow motors to operate at variable speeds, adjusting output to match the load requirements in real time.
Without a VFD, induction motors run at a near-constant full speed regardless of load demand, resulting in energy waste when operating under throated loading. With a VFD, the motor can slow down when less work is needed, dramatically reducing energy consumption. This is especially beneficial in applications like pumps and fans, where the power required is proportional to the cube of the speed.
System-Level Considerations
A motor does not operate in isolation. Its efficiency is influenced by the entire system it is part of, from the power supply to the mechanical load. That is why a holistic approach is essential.
Proper motor sizing is critical. Oversized motors operate inefficiently at partial loads, while undersized motors
can overheat and fail prematurely. Conducting a load analysis helps ensure the motor is appropriately matched to its application.
Regular maintenance is another key factor. Dirty filters, misaligned shafts and worn bearings can all degrade motor efficiency. Implementing a preventive maintenance program helps keep motors running at peak performance.
Higher efficiency motors usually operate at a slightly faster speed than lower efficiency motors. System performance must be considered when replacing low-efficiency motors.
Smart Monitoring & Predictive Maintenance
Thanks to advances in digital technology, it is now possible to monitor motor performance in real time. Smart sensors can track temperature, vibration, current draw and other parameters, providing early warning of potential issues.
This data can be used for predictive maintenance, allowing technicians to address problems before they lead to failure. It can also help identify inefficiencies, such as motors running under light load or operating outside their optimal range.
By integrating motor data into a broader energy management system, organizations can gain valuable insights and continuously optimize their operations.
Engineering a Smarter Future
Energy-efficient large motors are more than just a technological upgrade; they are a strategic investment in sustainability, reliability and profitability. By focusing on high-quality materials, precision engineering, advanced designs and intelligent controls, organizations can unlock significant value from their motor systems.