There are numerous factors to consider to ensure the best performance with this technology.
12/10/2015
One of the greatest advantages of a progressive cavity (PC) pump is that its flow rate is determined solely from the pump speed. The PC pump exhibits pump flow that is linear and repeatable, like an ideal metering pump. These pumps are unique because their starting torque is often greater than the operating torque during operation, but this characteristic creates a challenge when using variable frequency drives (VFDs) with PC pumps. This article will help with better selection of VFDs for most PC applications.
VFD Characteristics
Constant torque (CT) VFDs are used in applications where there is a linear relationship between power required and equipment speed. Variable torque (VT) VFDs are used when the required equipment power is not linear with respect to speed, like centrifugal pumps and fans. Sensorless vector drives are becoming the preferred option for drives. This technology recognizes many factors that influence drive/motor performance, and it monitors them continuously to optimize performance and minimize power requirements. For drive selection, note the VFD is a purely electrical device. Therefore, the selection is determined solely by voltage and current capability. The advertised horsepower (HP) is stated for the convenience of being similar to motors. The continuous rating should always be compared to the motor’s maximum amperage. The VFD’s overload capability in percent is a multiple of its maximum continuous current and not the motor’s full-load amperage. Only CT or sensorless vector CT should be used with PC pumps.Electric Motor Theory
For the purpose of simplicity, assume that an electric motor is constructed of three electromagnets (stator) and the rotor—a metal that is attracted or repelled by the electromagnets. The magnetic field created by voltage and subsequent current causes the rotor to chase the magnetic field. When the rotor cannot keep up with the magnetic field, the motor draws high current. The motor draws the most current when it is starting. The peak current the motor produces is often referred to as locked-rotor current. This locked-rotor current determines the maximum starting torque the motor will produce. It is usually a multiple of full-load current that ranges between 1.5 to 6 times the motor’s full load amps (FLA). This surge of current is what a PC pump relies on to be able to overcome the pump’s starting torque. Factors that have the potential to limit the motor starting torque include a conductor that is too small or too long, a circuit breaker that is too small, or minimal VFD overload capability. A motor’s maximum starting torque is directly proportional to the current that it can absorb for a short period of time. The more it can absorb, the more torque the motor can produce. When starting a motor across-the-line, this is only limited by conductor sizing. The VFD acts like a filter between the line and the motor. The filtering limits the amount of current based on the VFD’s design. Most modern-day VFDs have this overload capability of 150 percent for 30 seconds and 180 percent for 5 seconds. Some can even handle 200 percent for short periods. The percentages are in relation to the maximum continuous current rating of the VFD, which is found on the nameplate.Preparing VFD Operation
Selecting the PC pump involves experience and knowledge of the product and application. After selection, the starting torque, running torque and pump revolutions per minute (rpm) range are known entities. Considerable thought should be given to selecting the gearbox ratio with respect to the rpm range of operation when using a VFD. It is beneficial to choose a gear ratio that is as high as possible and places your maximum VFD frequency close to 85 hertz (Hz) because a PC pump requires greater starting torque than running torque.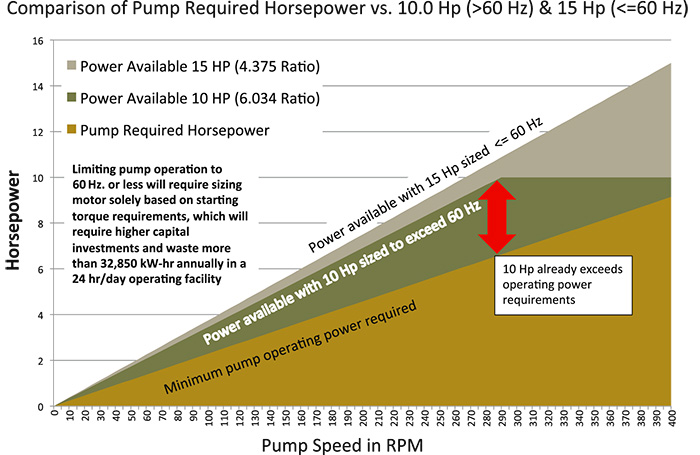
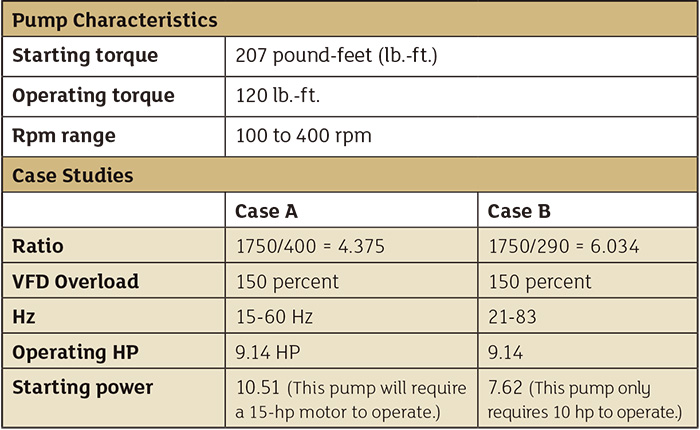
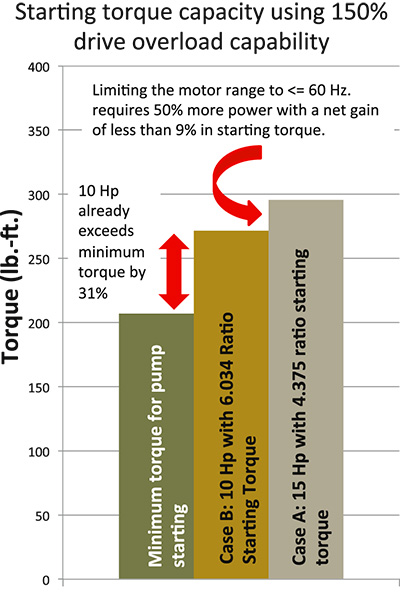