Understanding the causes and effects of minimum flow damage in centrifugal pumps is critical for knowing how to prevent it. End users should also be familiar with the advantages and disadvantages of common minimum flow protection systems in order to select the best ones for their applications. A common cause of premature wear in centrifugal pumps is oversizing or using too many pumps for a service. Operating a centrifugal pump below its allowable operating range as a result of oversizing or operating more pumps than necessary for an extended period of time is one of the most common causes of premature wear or failure of pump internals. These conditions can also damage seals and bearings. In addition to affecting the pump, oversizing or operating too many pumps can impact other system components and overall energy.
Improving Efficiencies
For example, a boiler feed system was designed with three pumps—two for parallel operation and one standby spare. The automatic recirculation valves used to protect the pumps were wearing prematurely compared with earlier plant history. A review of the process flow rate showed that a single pump would support the current demand. With two pumps running, the process flow requirement was less than the minimum flow the pumps needed. Both minimum flow valves were partially open to bypass continuously. Once the system changed to operating one pump rather than two, the system operated slightly above its best efficiency point (BEP), which stopped the rapid valve wear and decreased power consumption. Another plant had two 100 percent pumps with continuous flow orifices to provide minimum safe flow. During startup and some low-load cases, however, the pumps experienced excessive vibration. Changing the orifices to increase bypass flow solved the vibration problem, but now the combined flow of the orifices and the process flow ran out too far on the curve and was below the needed pressure to sustain the process. The solution was to run both pumps in parallel, which negated the standby pump concept and drastically increased the power cost of pump operation. To address this issue, personnel replaced the orifices with automatic recirculation valves that only opened when the process flow dropped to minimum flow. As a result, the plant was able to support the process by operating a single pump as originally intended.Minimum Continuous Safe Flow
Minimum continuous safe flow (MCSF) is the flow at which a pump can operate continuously without excessive wear from hydraulic anomalies and temperature rise associated with low-flow conditions. If the answer is yes to any of the following questions, a pump is probably operating below the safe minimum flow:- Are the impeller vanes (first-stage impeller if a multistage pump) pitted or worn through?
- Are the wear rings or journal bearing bushings worn more on one side even though the pump shaft appears to be centered when in a static condition?
- Does pump noise and/or vibration increase more than expected at low process flow demands?
- Has the pump experienced shaft breakage that could not be explained?
- Has the pump casing and/or bearings shown signs of overheating?
Thermal Damage
Since the 1940s, it has been common practice to hold the temperature rise of the product being pumped to at most 15 F. On hydrocarbon applications, it is best to keep temperature rise under 10 F (and under 5 F when net positive suction head [NPSH] is critical). The temperature rise is the result of hydraulic power losses within the pump. The difference between brake horsepower consumed and the water horsepower developed is converted into heat and transferred to the liquid being pumped. If the pump operates against a completely closed valve, the power loss becomes equal to the brake horsepower generated at shutoff. All of the horsepower is used to heat the volume of liquid within the pump casing, which results in a temperature rise.High Radial Thrust
High radial thrust is often the common root cause of a single-stage pump failure. The pressure distribution around the pump casing is rarely uniform and leads to a radial force that deflects the shaft. The radial force is lowest at the BEP and increases at capacities away from BEP to a maximum at shutoff. High radial load causes vibration, which can shorten seal and bearing life and, in extreme cases, can fatigue shafts. Industry standards limit radial deflection for single-stage pumps to 0.002 inches. This level of deflection is low enough to prevent most shaft failures, but seal life can be shortened if operated at low flow for extended periods of time.Pump Surging
If a pump does not have adequate flow, it can build up discharge pressure. When this pressure reaches a certain level, the pump cannot overcome it and the fluid starts to reverse flow. The reverse momentum causes the pump speed to slow down and the impeller slips backward, building pressure again. The fluid shifts back and forth. This cycle will repeat and could cause premature wear of thrust bearings.Rotor Vibration
Low-flow operation results in a mismatch of flow incidence angles in the impeller and diffuser vanes. This can lead to the formation of vortices that shake the rotor assembly at sub-synchronous frequencies. Long-term vibration can result in fatigue of impeller shrouds or diffuser plates.Internal Recirculation
At reduced flow, centrifugal pumps can experience a flow reversal where the fluid turns and flows back upstream. This results in internal recirculation, which is often referred to as suction recirculation. Internal recirculation is often a difficult problem to understand. It occurs at reduced flow rates when more liquid approaches the eye of the impeller than can pass through the pump. Every pump has a point where recirculation begins—a point inherent to the impeller’s design. Internal recirculation causes the formation of vortices with high velocities at their core and a lowering of the static pressure at that location. This leads to cavitation, pressure pulsations and noise that can interfere with the pump’s operation and damage the impeller. The location of the cavitation damage indicates that the problem is either internal recirculation or classic cavitation resulting from low NPSH. If the damage is on the inlet side of the impeller vanes, the cause is classic cavitation. If the damage is in the hidden pressure side of the vanes, the cause is internal suction recirculation.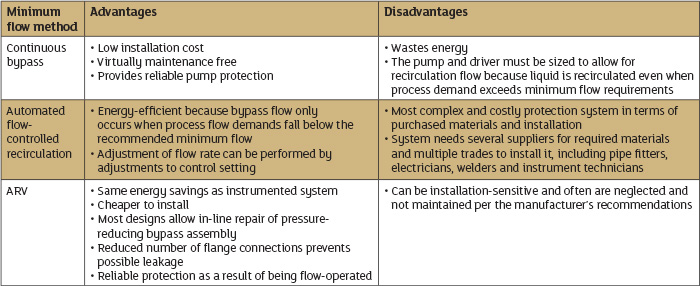
Minimum Flow Protection Systems
End users can employ three main methods of minimum flow protection: continuous bypass, automated flow-controlled recirculation and self-contained automatic recirculation valves (ARVs). Each has its advantages and disadvantages, which are outlined in Table 1.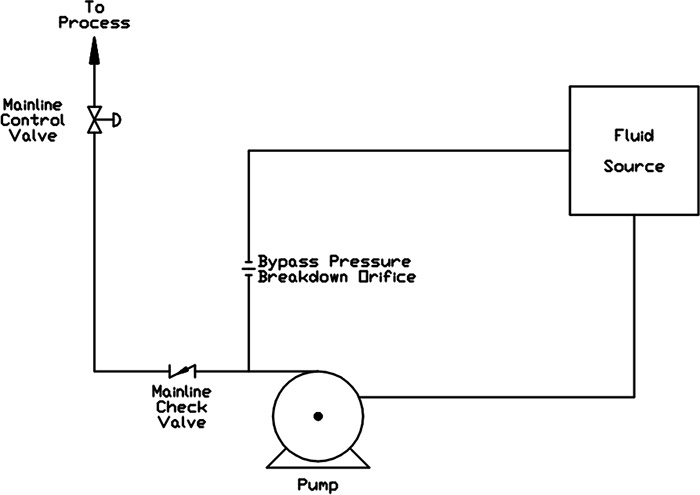
Continuous Bypass
A continuous bypass system circulates liquid continuously regardless of the system demands for fluid. A fixed orifice in the bypass piping reduces the pressure and is sized to bypass adequate liquid to protect the pump. The required NPSH increases as the pump operates further out on its performance curve, so the addition of a continuous flow volume will often require a larger pump/driver. Because of the economic disadvantage during operation, continuous recirculation should be confined to small-volume, low-head pump applications. When the energy to bypass minimum flow exceeds 10 brake horsepower, an alternate method can often be justified.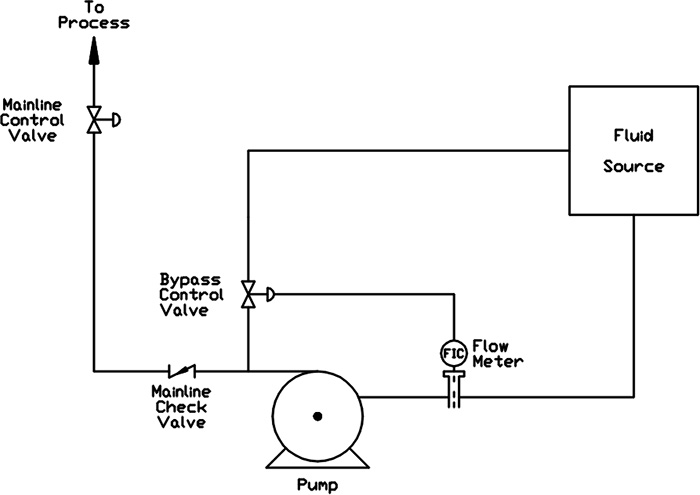
Automated Flow-Controlled Recirculation
Another approach is to install an instrumented flow-control loop, which opens (bypasses) liquid at low flows and closes when process demand exceeds pump minimum flow. A typical system includes a flow meter, bypass control valve with its related automation, and mainline check valve. An orifice or other backpressure-creating device may be required to prevent flashing in the bypass valve and return pipe.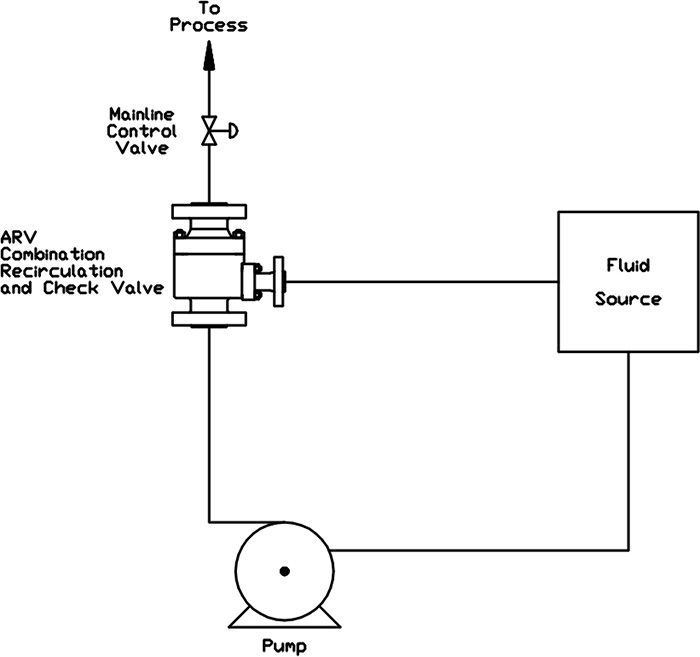
ARVs
These valves have multi-purpose built-in functions, including mainline check valve, flow-sensing elements, bypass flow-control valve and bypass pressure-reducing valve. The ARV operates without air or electric power and can be installed with three piping connections, on or near the pump discharge, just as an ordinary check valve would be. On pump startup and without process demand, the bypass is completely open, recirculating the necessary minimum flow. Once process demand begins, the spring-loaded disc is lifted and held in position by flow demand. Until main flow demand exceeds recommended minimum flow, the valve will bypass enough flow so the sum of the process flow and the bypass flow equals or exceeds minimum flow. As the main flow demand increases beyond recommended minimum flow, the bypass will close, and all flow will go to the process. When using ARVs, operators must follow the manufacturer’s instructions regarding flow direction, spacing from pump discharge and straight pipe requirements. Once ARVs are installed and insulated, they should not be forgotten. To prevent untimely failures, users should follow the manufacturer’s inspection and maintenance procedures.Recommendations for a Reliable System
Determination of a pump’s minimum flow must be taken seriously, and a reliable system should be incorporated with every new pump installation. Users should review installed pumps with higher-than-expected failure rates and/or maintenance requirements for proper minimum flow protection. When investigating minimum flow equipment needs, end users should consider doing the following steps:- Head off problems by making sure the conditions of service that end users provide to their suppliers are as accurate and complete as possible.
- Check out a supplier’s experience with similar applications and be sure to ask about their reliability and service.
- Demand that the valve or orifice you purchase be tested to assure proper performance. Documentation of the “as-tested Cv” should be available for review at your convenience.