Today, maintenance professionals are looking for better ways to evaluate machine conditions. One critical task for plant management is making the decision of whether to stop a machine for unplanned maintenance or run until the next planned plant outage. These evaluations and decisions are often based on expert experience alone, and therefore subjective. Software can support and assist end users in making critical decisions. One example is a new software platform used in high-pressure compression plants. It is based on the concept of quantitative evaluation of machine performance. Using the software, it has been possible to assess the centrifugal compressors’ health conditions through quantitative comparison of field operative parameters to conditions predicted from a machine-computer model.
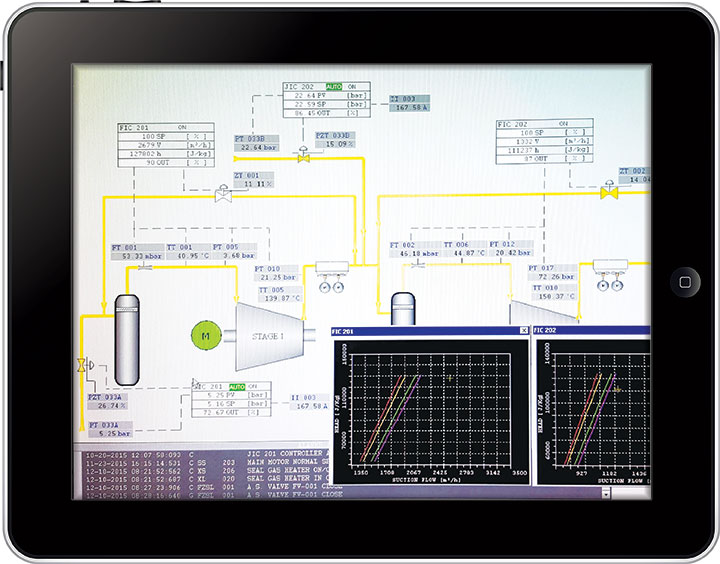
Method Description
Quantitative assessment of compressor performance and health status requires a comparison of measured performance to design, adjusted to actual operative conditions. Starting from OEM design or test performance maps, the software predicts expected compressor performance in the actual inlet conditions (actual suction temperature and pressure and gas mix composition). The software calculates, at the actual running speed, the following expected curves, valid for actual inlet conditions:- discharge pressure vs. suction flow
- discharge temperature vs. suction flow
- compressor efficiency vs. suction flow
- polytropic head vs. suction flow
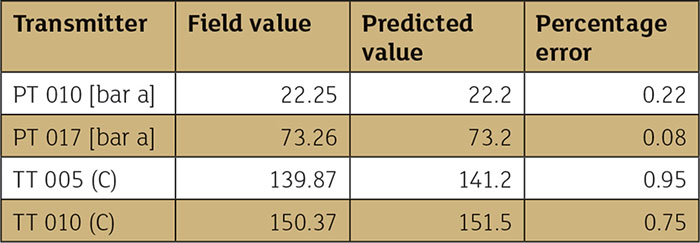
Conclusion
Numerical prediction of compressor performance allows a quantitative evaluation of compressor health status. The applied methods also allowed:- Prediction of the performance of a centrifugal compressor under varying thermodynamic conditions of the inlet gas. The prediction of compressor performance is accurate even at high pressures, where the ideal-gas-theory and simplified-formulas approach commonly used introduces considerable errors.
- Analysis of compressor performance during operation and comparison to expectations provided by the OEM
- Advanced protection from surge
- Indications of the health of the compressor (diagnostics) based on the capability to analyze the performance and efficiency of the machine in a simple and immediate way
- Reinforcement of decision making and maintenance planning along with specific recommendations for optimization of plant productivity