Pipeline operators are responsible for transporting billions of gallons of oil every year, and they are constantly looking at ways to improve efficiency and reduce costs. Depending on fluctuating network demands, this might require managing an increase or decrease in flow rate in the pipeline, a change in pressure or simply a pump upgrade to more efficient technology. So how do you change pipeline flow and pressure performance while maintaining efficiency and reliability? From an engineering perspective, the process performance required from a pipeline can seem to change all too frequently. Veering away from the original pipeline pump design criteria makes keeping the “right fitted” pump for the current set of conditions a challenge even for the most dedicated engineer. There can be many reasons for needing to rerate pipeline pumps: increasing throughput of deliveries is the most common requirement, but often the pipeline was overdesigned in the first place and now flow rates are less than the original design specification. Pipeline pressure derating can also be the catalyst behind a rerate or simply the need to improve or restore pump efficiencies and reliability in order to reduce power costs and improve run time.
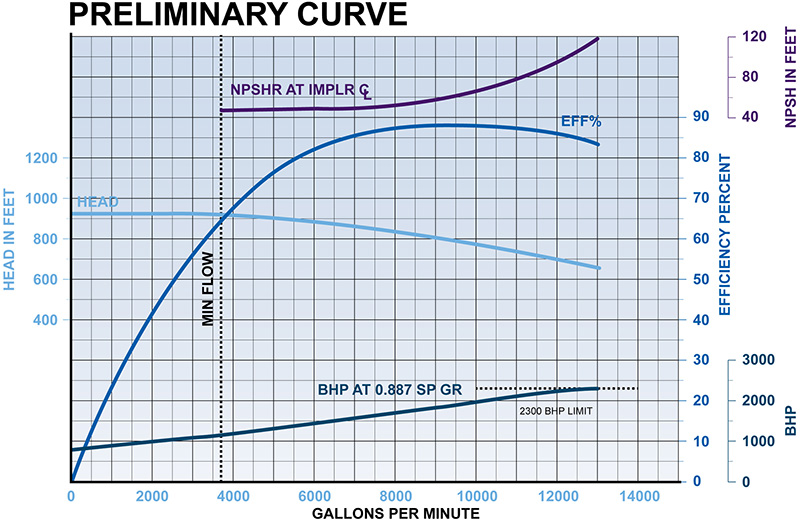
Project Request
A recent commission is a good example to illustrate how each project brings its own challenges and how good organization and resources are essential to stay on track and on budget. This project began with a phone call to a field engineer. The end user was contemplating a 20 percent increase in flow rates in his pipeline and wanted to make the change with the existing pumps and motors without exceeding or moving the existing station horsepower. The end user also wanted to deliver four different grades of crude oil.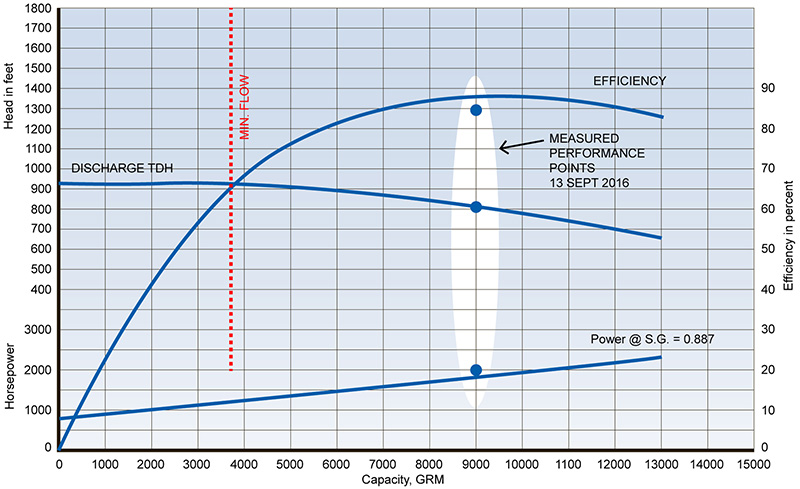
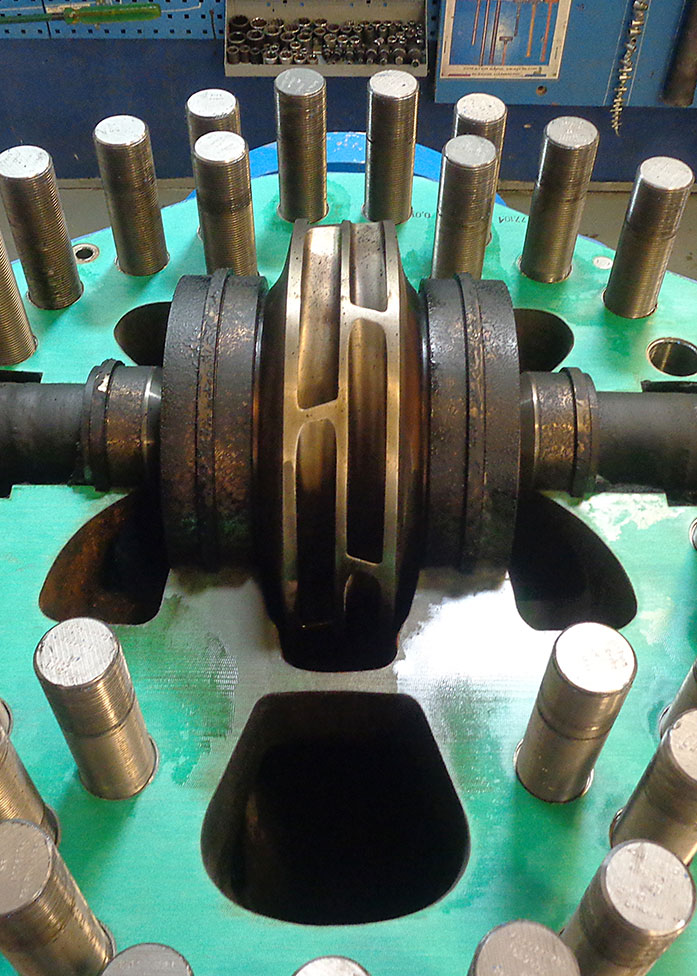
Design Strategies
Within a few weeks, the pump manufacturer’s advanced engineering group had developed options for the end user. After careful consideration and communication, a strategy was developed and the project was started. The key was the hydraulics, and designs were developed that modified the impeller and volute of the pump so that the specified flow rate and differential pressure could be achieved. Impeller and volute modifications also addressed concerns about vibration and cavitation at the increased flow rates.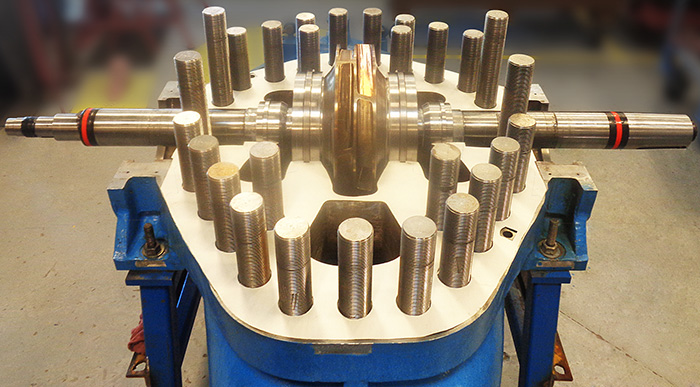
Rerating
Pipeline hydraulic pump rerates are a theoretical construct in most cases. Site variables make it very difficult to be precisely sure how the hydraulic design will perform once in service. A pump performance test at the factory to prove the modifications can be helpful. However, with rerates, it can add significant costs and time to a project schedule. A field performance test is often better and adds the benefit of testing the pump as installed and with the pipeline product. In the pump rerate example, field acceptance testing was provided in the form of a field performance evaluation. On three of the rerated pumps, actual field flow and pressure values along with vibration data and thermal images were all employed to confirm the pump rerate was performing as predicted and also provide baseline data for future trending.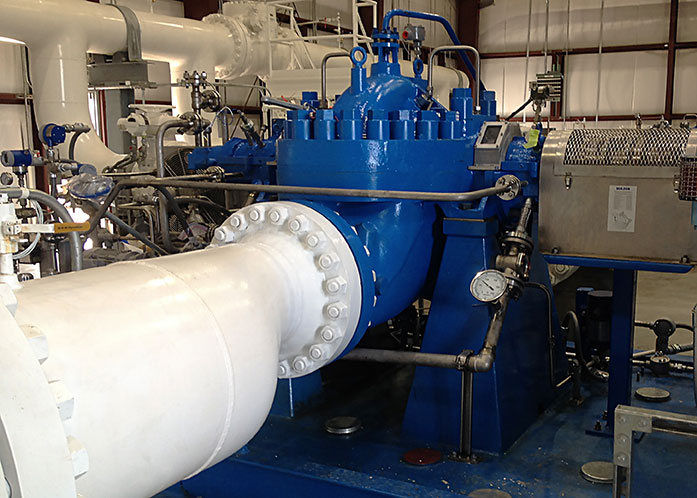
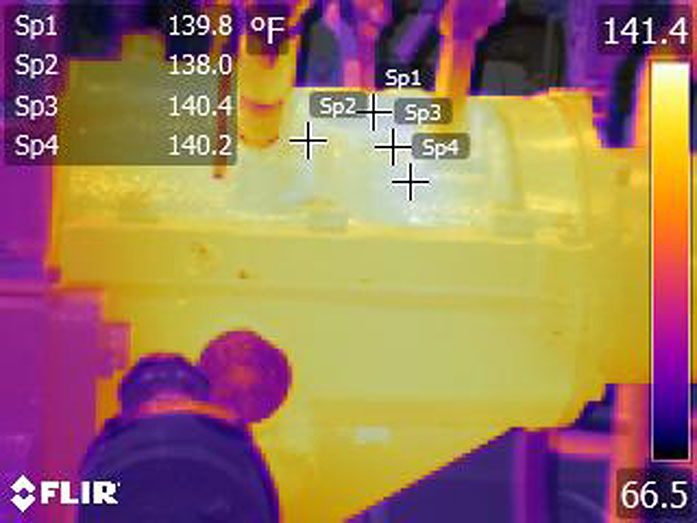
Improving Flexibility
Oil pipelines may be required to change the commodity that they carry, for example from heavy to light crude oil, or to vary the flow rate during a typical day. Essentially, changes in density, pressure or flow rate may be required, and if the OEM is made aware of these requirements, allowances can be made in the design that enable these changes to be implemented more cost effectively..jpg)