Nestled into the front range of the Rocky Mountains, right below Pikes Peak and about 80 miles south of Denver, is the home rule municipality of Colorado Springs. As of 2016, Colorado Springs claims the 40th largest city population in the United States and the second largest in Colorado. In addition, the city has grown by nearly 12 percent since 2010. Colorado Springs Utilities, the primary utility service for the its metropolitan area, is one of the largest utility services in the country and handles not only water, but waste treatment, gas and electricity. Colorado Springs constantly requires improved methods to supply fresh water and protect downstream users of treated water. Colorado Springs Utilities operates three wastewater treatment plants in the metropolitan area and includes laboratories on each site. Each lab analyzes thousands of wastewater samples per year for process control and regulatory compliance. Colorado Springs Utilities’ first wastewater plant was the Las Vegas Street plant, which is governed by the City Council Utilities Board. In 1984, the Hannah Ranch facility, now called “Clear Springs,” was built to further process plant product from Las Vegas Street. At first, biosolids were trucked across town, deposited in pits and covered. By 1985, an 18-mile pipeline was laid between the two facilities so biosolids could be more effectively transferred from Las Vegas Street to Hannah Ranch. Two pipelines were put down with the intention to transport reclaimed water back through the second pipe; however, this intention was never fulfilled, as other uses were found for the reclaimed water. The biological treatment used today involves standard processes of aerators, activated biosolids and clarifiers. Chlorination and sulfur dioxide are used to neutralize treated water before it is discharged. At peak capacity, the Las Vegas Street plant pumps 54 million gallons of biosolids per day (mgd).
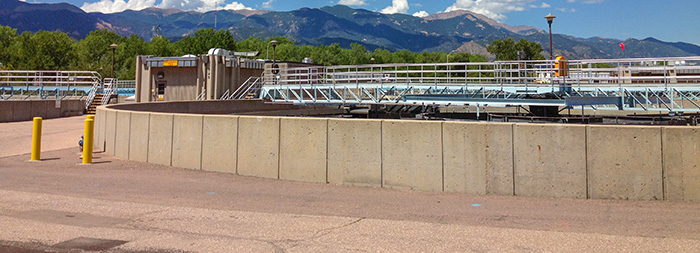
.jpg)