The oil and gas industry is a complicated business that covers the discovery of underground reserves to their recovery, gathering, refining, manufacturing, transport, storage and eventual marketing. Throughout this massive production and supply chain, pumps are required to move fluids and gases to and from numerous points. For many years, the pumping technology of choice in many fluid-transfer applications in oil and gas production has been centrifugal pumps, which have performed well in these situations. Their method of operation—fluid enters the pump impeller along or near to the rotating axis and is accelerated by the impeller, flowing radially outward into the volute discharge port—makes them well designed for the high-volume, severe-duty transfer applications that are common in the industry. The centrifugal pumps also work especially well with thin, water-like fluids that must be transported through networks of piping with variable flow rates.
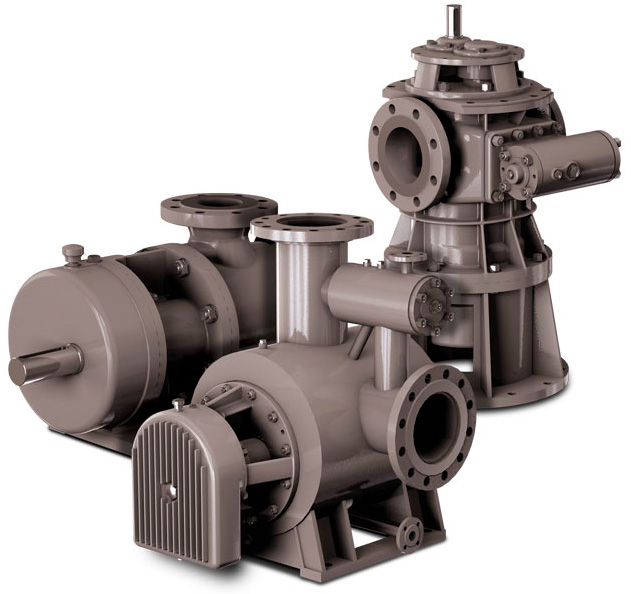
- Ability to handle a wide range of flows, pressures, liquid types and viscosities
- Constant flow, even in the presence of varying system backpressures due to viscosity changes
- High volumetric and overall operating efficiencies, resulting in reduced operational costs
- Controllable output via variable capacities
- Low internal velocities
- Self-priming operation and good suction characteristics
- High tolerance for entrained air and other gases—a prime consideration in oil production
- Low mechanical vibration lengthens service life
- Intrinsically smooth and quiet operation
- Extremely low pulsation reduces stress and prolongs life of associated fluid-transfer components (piping, hoses, etc.)
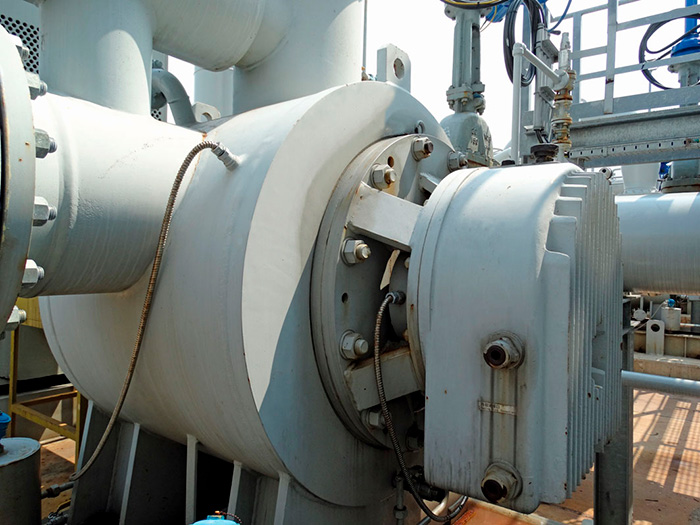