The positive displacement technology handles backpressure fluctuations, cavitation and air entrainment.
12/21/2015
Rotary positive displacement screw pumps are used by a wide range of industries, including oil and gas production, pipelines, refineries, terminals, chemical processing, marine and power generation. Specifically in the power generation sector, screw pumps are commonly found in applications such as bearing and gear lubrication, high-pressure fuel injection, fuel forwarding, jacking oil and hydraulic power for hydro-plant control.
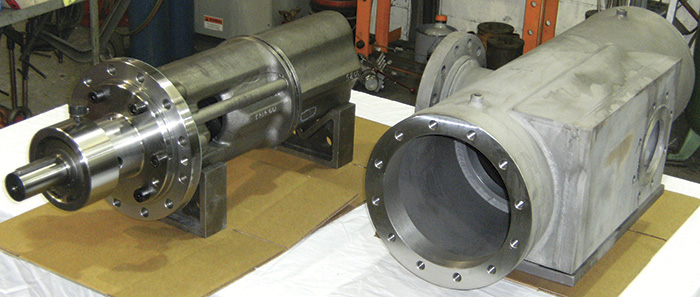
.jpg)
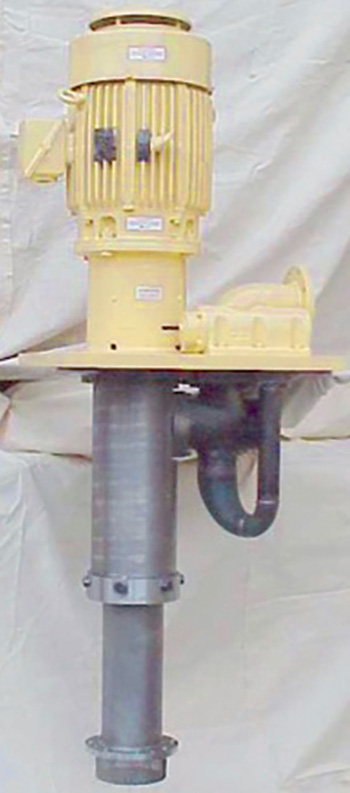
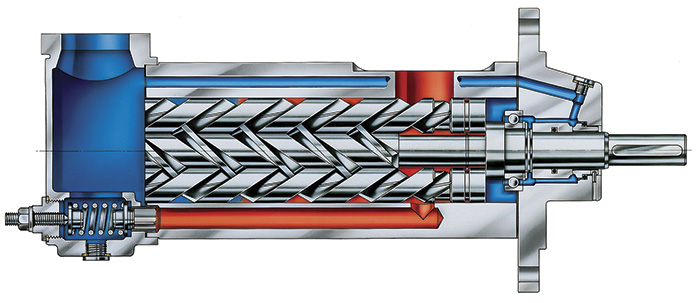
Three-screw Pump Benefits
The features of this design can be a natural fit for power generation applications.- Positive displacement to ensure critical capacity regardless of backpressure
- High efficiency across a broad range of pressure and viscosity
- Higher tolerance of entrained air and cavitation than centrifugal pumps
- Available deaeration features
- Versatility for pumping both low- and high-viscosity products to 15,000 centistokes (cSt)
- Operates at motor speeds, eliminating need for a speed reducer
- Low pulsations, vibration, shear and noise
- High reliability/low maintenance
- Self-priming/low-suction pressure requirement
- Capacity to more than 3,000 gallons per minute (gpm)
- Pressure capability over 2,500 pounds per square inch gauge (psig)
- Single mechanical seal/single bearing
- Available integral relief valve
- Several casing material options
- Horizontal and vertical tank or pedestal mount configurations
- Custom fabricated casings for drop-in replacements of older pumps