Q. We recently purchased several magnetically driven rotary pumps for our process and want to know if we need to be aware of any special operational considerations. A. The operation of magnetically driven rotary pumps is similar to the operation of standard rotary pumps. However, special considerations are required: Dry running—Magnetically driven pumps must not be run dry. Heat buildup is a major concern. Also, the bearings in most magnetic drive pumps must be lubricated by the pumped liquid. If run dry, these bearings can wear quickly or fail, depending on the design. Some manufacturers may make pumps that have dry run capability. Consult your supplier if this is a concern. Entrained air—Liquids with entrained air can also cause bearings to wear or fail because of heat buildup or lack of lubrication. If entrained air or gases are anticipated, this condition should be noted and discussed with the manufacturer. Special designs to operate within these conditions may entail special flush systems. However, specific determination depends on the type of entrainment, operating conditions and percent of gas/air entrainment. Priming—Air or gases trapped in the containment shell may cause the bearings to wear or be destroyed after a short period of operation. Most designs require that the pump casing and containment shell be fully primed and properly vented. The end user must follow the manufacturer’s recommendations on these procedures. This is one of the most common failures of this type pump at startup. Temperature—The magnet temperature can be significantly higher than the pump operating temperature or recommended practice for the pumped liquid. The pump user must carefully review the cautions and temperature limits from the manufacturer and consider the liquid properties. In addition to liquid considerations, excessive temperatures can cause damage to the magnet, containment shell or static seals and result in the failure of containment integrity. Magnet materials—Typical magnet materials used in these applications, in order of increasing temperature capability, are neodymium, samarium cobalt and alnico. Magnets retain most of their strength up to the manufacturer’s maximum temperature. Magnet temperature limits, as opposed to pump operating temperature limits, are established by the type and grade of the magnet material used and is defined as the temperature beyond which the materials become permanently demagnetized. As the temperature approaches its Curie temperature, the magnet will lose some force, possibly resulting in the decoupling of the pump. For magnet life and proper operation, the end user should establish a maximum operating temperature with an appropriate safety margin. Heat generation—In pumps with metallic containment shells, heat can develop in the shell during operation because of eddy currents that are generated by rotating a magnetic field around the conductive material of the shell. This heat is dissipated to the atmosphere and the pumped liquid. Caution must be taken to ensure that the liquid temperature stays within allowable limits. Liquid flashing—Certain liquids could ignite, flash or change properties because of temperature increases. All pumps should be applied in accordance with the manufacturer’s temperature recommendation and published liquid physical property data. Since liquid flow dissipates the generated heat, the liquid’s temperature and pressure profile in the coupling should be discussed with the manufacturer to ensure safe performance at all operating conditions. Ambient and pumping temperature—The manufacturer’s published temperature limits are normally based on the assumption that the liquid inlet temperature and ambient temperature are in the same range. If ambient and liquid inlet temperatures are substantially different, then the temperature rise of the shell may vary from the published data. This condition should be noted in application criteria provided to the manufacturer so that proper limits and temperature detection devices can be mutually discussed. Other factors that should be considered are condition monitoring of the pump, demagnetization of the magnetic coupling, which leads to slip or decoupling and humidity effects that can lead to corrosion of certain types of magnets. Additional information is available in ANSI/HI 4.1-4.6-2010, Sealless, Magnetically Driven Rotary Pumps for Nomenclature, Definitions, Application, Operation, and Test. Q. I am developing a purchase order for rotodynamic pumps and need guidance in determining what acceptance tests are appropriate for these pumps. A. ANSI/HI 14.6 mandates an acceptance test based on pump flow and head delivered. It also details several optional tests that a pump purchaser may want to have performed and provides a baseline recommendation for optional tests, shedding light on the consequences of specifying tighter test tolerances as well as optional tests. Clearly stating the costs of acceptance tests and special tests in the contract is recommended. It should be understood that specifying tighter acceptance tolerances generally leads to higher testing costs and longer lead times. When net positive suction head (NPSH) testing is specified, test costs will increase because the tested pump will have to undergo a different and more time-consuming testing program. This is often performed at a different test rig, requiring additional setup and tear-down time. To reduce the tolerance bandwidth, tighter manufacturing tolerances are required, which add cost and may increase delivery time. Sand-cast molds are the least expensive to make but typically have the widest tolerances. Investment casting will have the best finish and the most repeatable dimensions. The molding equipment cost for an investment casting may be two to four times that of a sand mold. It takes a high production volume to justify the cost of this casting equipment. To have a smaller bandwidth when sand casting may require many hours in hand labor to obtain the exact results from one pump to another. Reduction of the tolerance bandwidth for measuring the tolerances will add costs and may increase delivery time. This results from using more sophisticated test equipment and an extension of the actual test period to get a higher stability of the operation point.
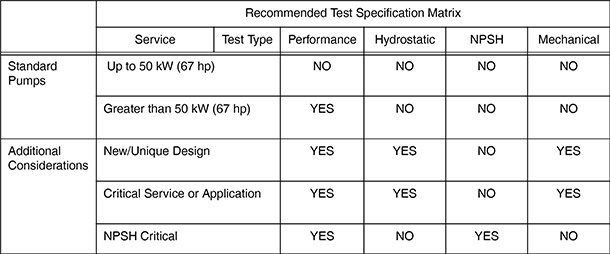