Many industrial processes use substances that are in an aqueous or “muddy” form, and the liquid portion must be removed. This may take place during production processes—for example, in the filtration of edible oils or yeast solutions—but more frequently it happens at the end of a process with waste sludge from various industries, including wastewater treatment. Because the disposal cost of such sludge is calculated using weight and volume, thickening and drying are particularly lucrative for the producer. During the process, sludge is treated using chemicals and/or physical processes so the substances in it form flake-like solids. After pH adjustment to neutral or alkaline using milk of lime, the dewatering process separates out water for disposal and significantly reduces the remaining sludge volume.
Chamber Filter Presses
The simplest technology for this process involves sludge collection and thickening via gravity. It is more effective to use technical drying methods with processes like centrifuges and evaporators, or more commonly, chamber filter presses (see Image 1).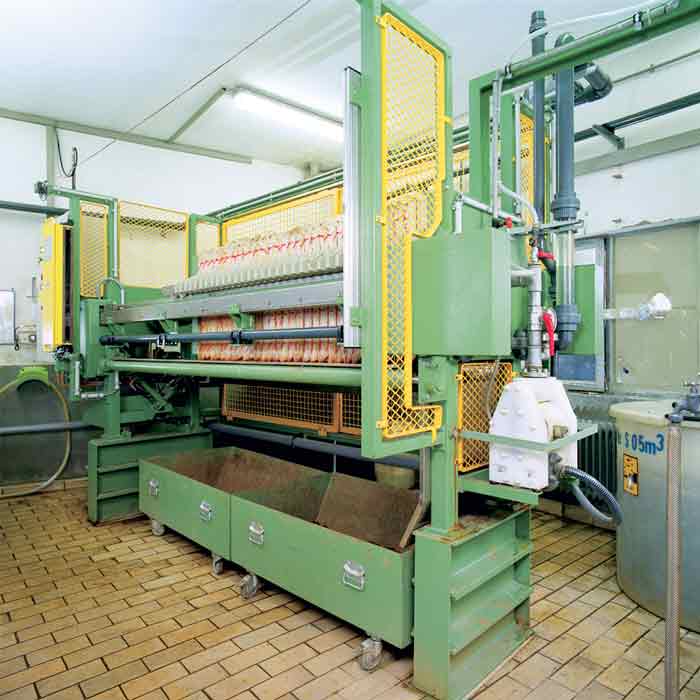
AODD Pumps
By comparison, an air-operated double-diaphragm (AODD) pump can be easier to use in these applications. These pumps are low-maintenance, self-priming, self-regulating, highly compact, and resistant to dry-running. Without the control or intervention of an operator or electronic system, the counterpressure of the chamber filter press regulates the feed rate automatically. The feed rate decreases continuously as counterpressure increases simultaneously to the degree of filling. This effect can be used to detect when the chamber filter press is full. When this is reached, the pump virtually stops—zero feed rate—or only occasionally makes a delivery stroke. In addition, the use of compressed air as drive power to move the diaphragms results in a highly efficient, regular and gentle cyclic drive that allows the medium to be fed smoothly. A standard AODD pump is typically limited to the pressure of the supplied air, which is often insufficient to fill the press. It is often necessary to increase the pressure, for which there are three very different technical solutions. The first variant uses one of the diaphragms on a standard pump to generate additional pressure. The force of this diaphragm, which is surrounded only by compressed air, is transferred to the feed diaphragm via the internal diaphragm connection, enabling the feed diaphragm to work with double the pressure. This method is rarely used because it leads to high pulsation, low feed rates and high air requirements. It also commands high service costs because the diaphragm on the air side is very sensitive and breaks quickly. Another variant is to operate a standard pump with an air pressure amplifier, which drives the pump with increased air pressure. This process is limited by the fact that a standard pump is often used. Although these pumps are equipped with external reinforcements, from a technical perspective, the standard pumps in question are designed and built for significantly lower pressures and have limited resistance to the increased strain. Additionally, the increased pressure resulting from these air pressure amplifiers, or “boosters,” pulsates strongly and can influence the product’s flow. Boosters also seem to reach their limits in maintaining pressure (for example, during repressing) because the devices are almost always too small. They yield the required end pressure but may require a longer filling time.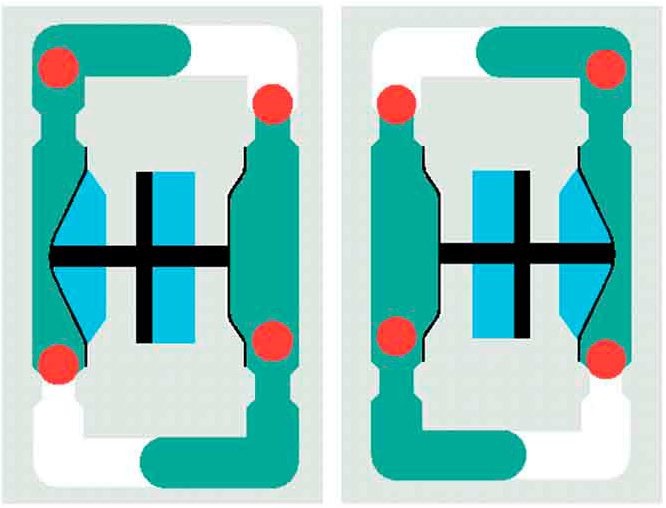
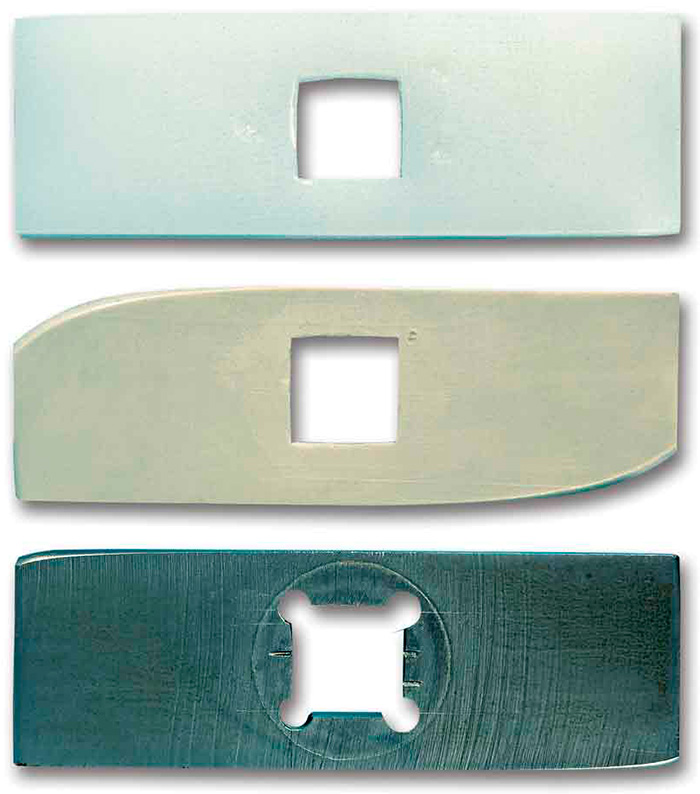