Flow measurement is an important aspect of operation in today’s industrial plants. Despite there being a wide range of possible instruments for any one flow metering requirement, the achievable performance of each one varies considerably depending on the operating conditions under which they are required to work. Each meter type has considerably different measuring ranges, sensitivity to process conditions, installation demands and media-quality requirements. This article examines common mistakes in the selection of flow measurement devices. Experience has shown it is wise to consult with a knowledgeable instrumentation supplier prior to making a flow meter purchase. The effort spent learning about basic flow measurement techniques and available meter options will help ensure a successful application once the equipment is installed.
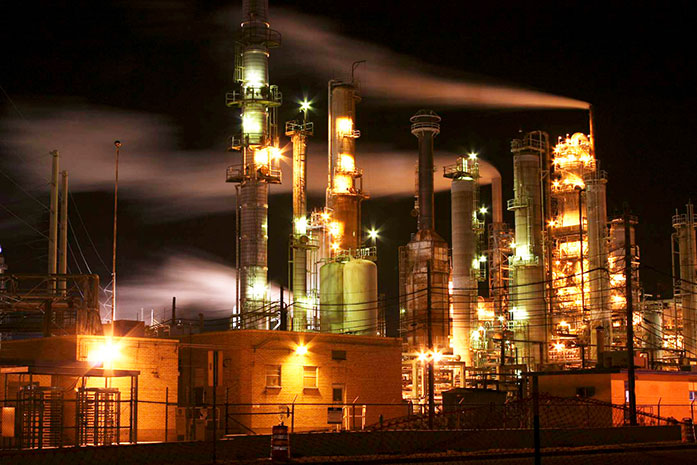
Introduction
In modern industrial plants, personnel need to make smarter decisions faster by capturing, managing and analyzing the right data at the right time. These facilities rely heavily on flow processes, and thus accurate and reliable measurement technology is vital to the efficiency and safety of their operations (see Image 1). Flow meters are an integral tool for measuring the flow of liquid, gas or a mixture of both in applications used in food and beverage processing, oil and gas plants, and chemical/pharmaceutical factories, among other industries. Inaccurate flow measurements lead to poor flow and related controls, poor quality products, and incorrect fiscal measurement, resulting in inadequate allocation of revenue among partners. In addition, an unsafe process due to wrong quantities could lead to facility damage and create an unsafe environment. When evaluating a flow measurement device, it is just as important to know what an instrument cannot do as it is to know what it can do before a final selection is made. Each flow meter has advantages and disadvantages, and the degree of performance satisfaction is directly related to how well its capabilities and shortcomings are matched to the application requirements. Often, users have expectations of a flow meter’s performance that are not consistent with what the supplier has provided. Experience has shown that a thorough evaluation should be done using a logical, step-by-step approach before making a decision on the type of flow meter. Because of the importance of meter selection, it is crucial to allocate sufficient time and resources for this evaluation.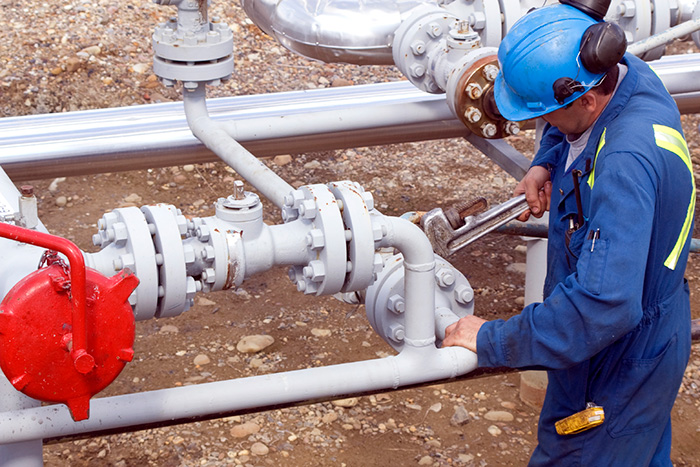
Typical Evaluation Errors
With countless flow measuring instruments currently available, making an optimal meter choice is often a challenging task. Industrial organizations have traditionally based their selection decision on price and published product specifications. However, users have also discovered:- Flow meter selection based on the lowest price often results in the highest installed cost.
- Choosing the highest accuracy meter based on product specifications often results in the least measurement accuracy in actual applications.
- Relying on a comparison of published product specifications alone may actually result in costly process downtime.
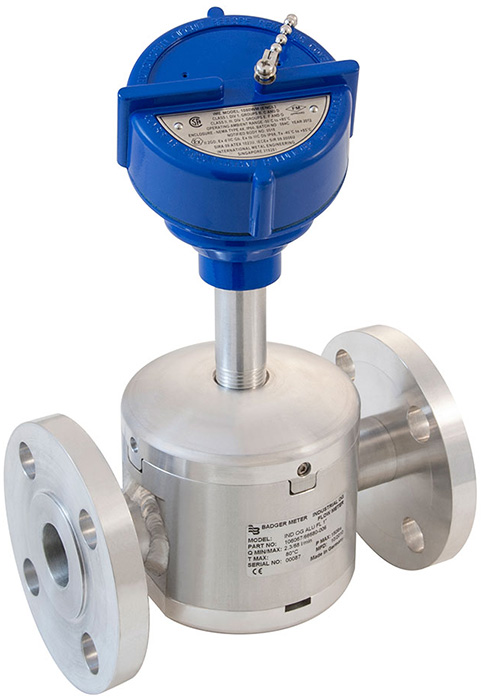