While the industrial sector struggles to survive in the U.S. market, the Environmental Protection Agency (EPA) continues to add regulations that further impact the already slim profit margins for many industries, especially those that are large power users. On Aug. 3, the EPA issued its Clean Power Plan for Existing Power Plants, which requires states to reduce carbon dioxide emissions by 32 percent (from 2016 levels) by 2030. Some call this Obama's "war on coal" because it will force power utilities to shut down coal-fired power plants, while supporters claim that the regulations help address environmental and health concerns. The fleet of coal-fired plants has already been reduced from a high of 55 percent to today's level of approximately 38 percent. While the U.S. government works to reduce emissions through increased regulations, it has not yet developed a national energy policy that will give investor-owned power generators—which make up 78 percent of utilities—some direction. Still, power utilities are required to deliver reliable power to the grid on demand.
Energy Efficiency Programs
As a result of this challenge, utilities are implementing energy efficiency programs. Many of the large progressive utilities, including Southern Company, Duke and Xcel Energy, have had programs in place for several years. A number of nongovernmental organizations (NGOs) have also stepped up to the plate. Given the potential impact on profits, the industrial sector would benefit greatly from more aggressively embracing energy efficiency. Energy efficiency, however, will only delay the inevitable. The U.S. industrial sector requires reliable power to meet production needs. Some industries have renewed their combined heat and power (CHP) plants to reduce their dependency on the grid. To meet electrical power requirements, power generators must add base load power plants. The path of least resistance is natural gas combined cycle (NGCC), which can provide the necessary base load power to meet grid requirements. The price of natural gas is low because fracking has reduced the price to almost historic levels. Will the price remain at this level? If history repeats itself—and it usually does—the answer is no. As fuel costs increase, power utilities will pass the cost on to consumers. Also note that as natural gas prices drop, utilities reciprocate and pass savings to their customers. This, however, does not address the issue of reliable power on demand. As power companies decommission coal-fired plants, by some estimates as much as 90 gigawatts by 2020, what will happen to the grid? How can industrial power consumers protect themselves from power pricing uncertainty? The following data, provided by the Wall Street Journal on Aug. 10, looks at power generation from a cost perspective. Coal-fired power plants: $38.00 per megawatt-hour Nuclear (existing): $29.00 per megawatt-hour Hydroelectric: $34.20 per megawatt-hour NGCC: $48.90 per megawatt-hour Wind: $106.00 per megawatt-hour Solar: $120.00 per megawatt-hour Cost per megawatt-hour for a new NGCC plant is approximately $73.40 because of the upfront capital costs. The cost per megawatt (MW) is affected by many factors but mostly by the facility's "capacity factor," which is the percentage of time it will produce its full-rated output. A typical condensing steam power plant such as coal or combined cycle will have a capacity factor of 85 percent or greater. By comparison, a typical wind generation facility will have a capacity factor of about 30 percent, while solar is about 18 percent.Pump System Optimization
In addition to implementing energy efficiency programs, the power industry can optimize existing plants—specifically pumping systems.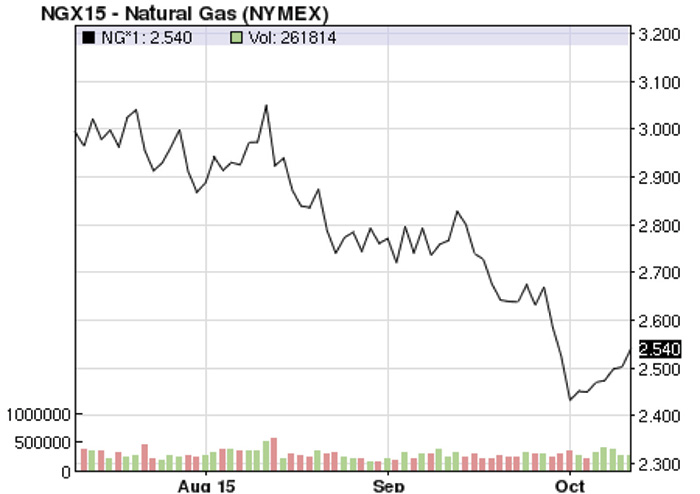