Their features and benefits make them ideal for the many liquid-transfer points in the soft drink production chain.
PSG
12/20/2016
Although per-capita consumption of carbonated soft drinks in the U.S. has been on a steady decline since peaking in the 1990s, the average American still consumes more than 41 gallons of the fizzy drinks annually—the equivalent of 437 12-ounce servings, or 1.2 cans a day. To address this decline, major soft drink conglomerates have been expanding their product portfolios to include beverages such as juice drinks and, to a greater extent, energy drinks that have become popular with millennials.
.jpg)
The Challenge
The U.S. landscape is dotted with soft drink production facilities, known as canning and bottling plants, that use ingredients such as high fructose corn syrup, various concentrates, flavorings and phosphoric acid (which adds acidity to the final beverage) to create products that are ready for consumption. In many instances, the large multinational corporations that dominate the global soft drink market contract with bottling companies to produce their beverages in accordance with their highly guarded, tried-and-true formulas. Mom and pop operations also produce, for example, small-batch root beers and ginger ales on a much smaller scale, but these operations still require canning and bottling companies.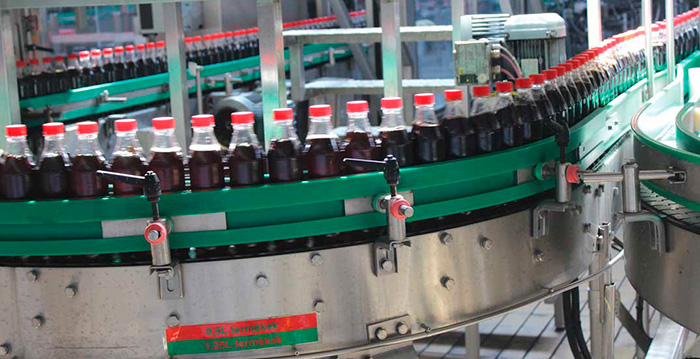
- Common tap water is treated at the production facility to remove any impurities that may affect the drink’s taste or color. The water’s alkalinity level also is adjusted to meet a regulated pH level.
- The treated water is sterilized to destroy any bacteria or organic compounds. A small amount of chlorine is used to complete the sterilization process.
- After the sterilized water “rests” in a storage tank for a few hours, it passes through an activated-carbon filter for dechlorination. From there, the completely sterilized water is transferred to a dosing station.
- Arriving at the facility in drums and totes, the pre-mixed concentrate that gives a soft drink its color, flavor and sugar content is pumped into the dosing station, where it combines with the water. The amounts of concentrate used at this stage are usually determined by weight, not volume, so the batch tank is placed on a load cell or scale, and the pump turns off when a pre-programmed weight is pumped into the tank.
- This concentrate/water mixture moves to the batch tank where it is blended to form the soft drink’s base. It is then flash pasteurized—a process that uses ultraviolet radiation to quickly heat and cool the mixture to remove impurities.
- At a precise temperature, the mixture is passed through a carbonator that adds carbonation to the product at predetermined levels according to the beverage’s recipe. Generally, juice drinks require far less carbonation than traditional soft drinks or carbonated energy drinks.
- The finished carbonated product is transferred to filling lines, where it is injected into bottles and cans of at high flow rates. When filled, the containers are sealed with pressure-resistant closures like aluminum caps or twist-off plastic tops.
- The cans and bottles (which must be labeled) are packed into cartons or trays before being placed on larger pallets for shipment to distributors.
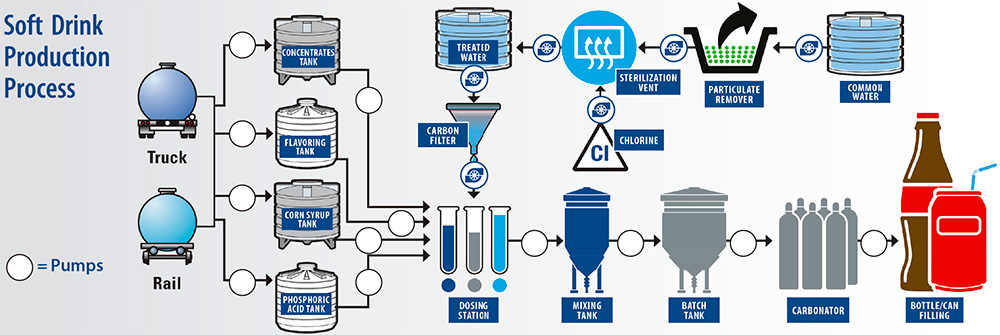
The Solution
Considering some of the potential shortcomings of centrifugal pump operation, AODD pumps may be a better choice for the numerous liquid-handling links in the carbonated soft drink production chain. Some AODD pumps have been engineered to meet the highest standards for operation in the manufacture of carbonated soft drinks. For example, one company’s AODD pumps possess the ability to safely and efficiently pump a wide range of viscosities and shear-sensitive products, and they work well with corn syrups, phosphoric acids, concentrates and flavorings that play a major role in soft drink production. The wetted-path material is 316L stainless steel with interior-polish levels that range from 0.8 to 1.3 micrometers (μm) (31.5 to 51.2 microinches [μin]) for ease of cleaning. Some of these are the only pumps in the industry to have earned certification by 3A Sanitary Standards Inc.—which is dedicated to advancing hygienic equipment design for the food, beverage and pharmaceutical industries—for both clean-in-place (CIP) and clean-out-of-place (COP) sanitizing operations. The free-draining flow path, wash-friendly clamp bands and CIP capability simplify cleaning and have enabled these models of AODD pumps to earn certifications from a number of regulatory agencies in the hygienic industry, including 3A, European Hygienic Engineering & Design Group (EHEDG), U.S. Food and Drug Administration (FDA) CFR 21.177, U.S. Pharmacopoeial Convention (USP) Class VI and European Commission (EC) regulation 1935/2004. Other features and benefits of these specific AODD pumps, which are available in sizes from 1/2 to 3 inches (13 millimeters [mm] to 76 mm), include:- availability of multiple sanitary elastomers
- sealless design for superior product containment
- delicate, shear-sensitive operation
- self-priming or dry-priming operation capabilities
- damage-free dry-run capability
- flow rates from 15 to 245 gallons per minute (gpm) (57 to 927 liters per minute)
- solids passage up to 3 inches (76 mm)
- high energy efficiency
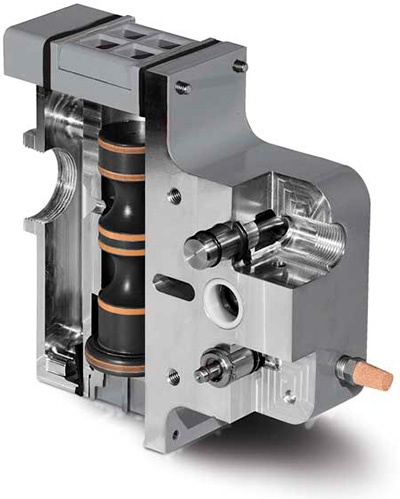
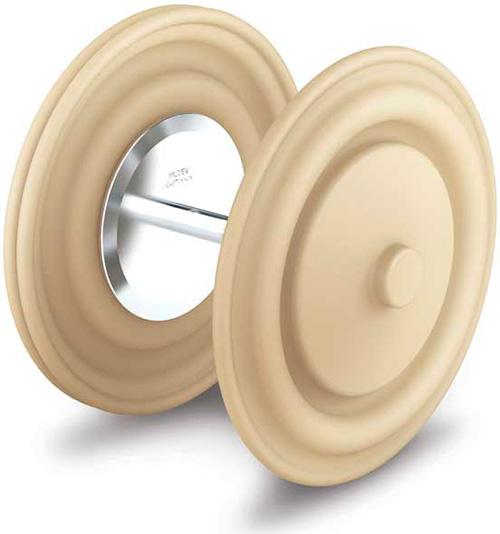
To read other Efficiency Matters articles, go here.