Best systems are constructed with components from same manufacturer
Neptune
12/20/2017
The reliable, safe and efficient feeding of chemicals into various critical stages of the steam-water cycle during power generation operations at power plants is an irreplaceable necessity for an industry that is one of the world’s most important.
Among the most significant stages are:
Pretreatment: The raw makeup water that passes through the power plant’s boilers that are used to create the steam that drives the turbines has to be as “perfect” as possible, or what is termed in the industry as “ultra-pure.” To get the water as pure as it can be, it passes through a series of filters, or clarifiers and demineralizers. To aid in the purification process, substances like ferric sulfate and sulfuric acid are injected in tightly controlled dosage amounts into the water.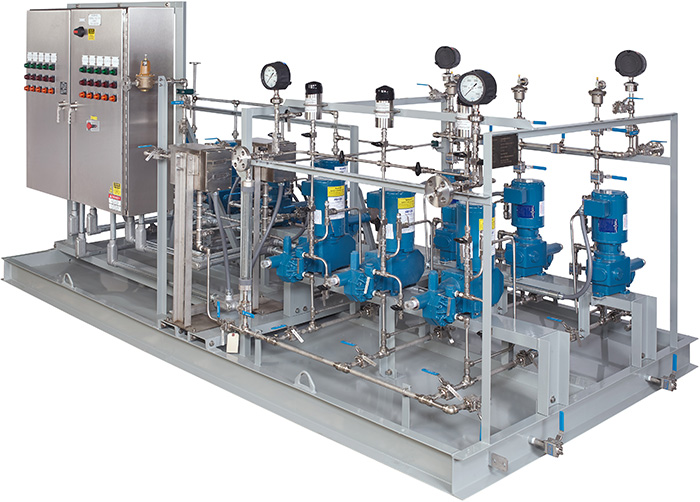
Assemble the Hardware
The challenge, then, for the operators of power generation facilities and their operations that require chemical feed is selecting the correct chemical-feed system. Too often, however, not enough thought goes into the components used in the construction of the system. Think of a person who chooses to buy an automobile. Would he purchase components that make up the automobile separately, or would he rely on a trusted manufacturer of a complete automobile to use vehicle components that are compatible with each other, with careful thought given to how they will interact during operation? Just opening a supply catalog and selecting the cheapest alternative, or choosing a brand that sounds familiar, is not enough to ensure a successfully operating chemical-feed system. Let’s take a quick look at the particular parts that make up a complete chemical-feed system. The pumps that are used to inject or dose chemicals into the process are critical components. Diaphragm-style metering pumps have been proven to be the most effective technology for use in chemical-feed applications, and there are generally three types of diaphragm pumps that can be used in these situations.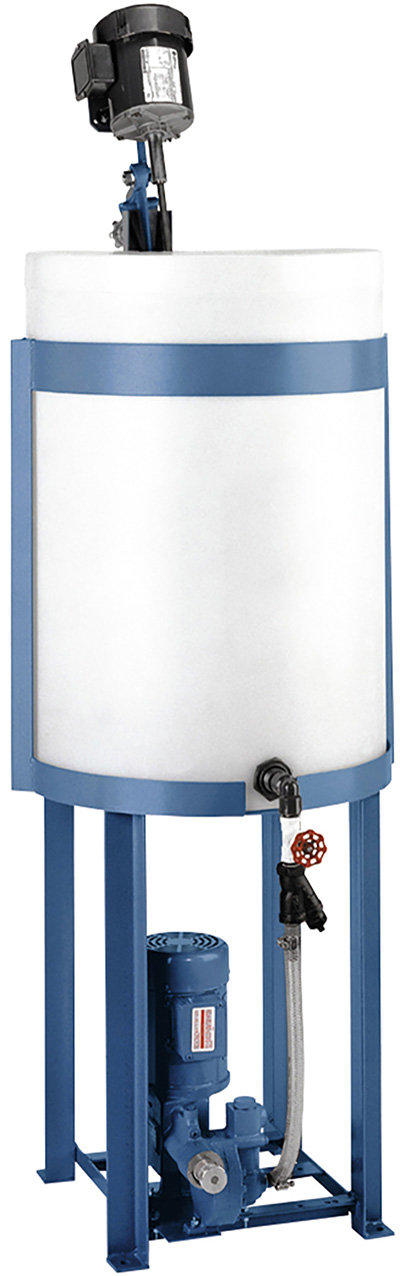
Take a Systems Approach
While selecting the proper pump and mixer style is the most important step in creating a successful chemical-feed system, finding the right ancillary components for that system is also critical. What many design engineers don’t realize is that many metering pump companies also develop and manufacture the components that make up a chemical-feed system. Many metering-pump manufacturers offer standard, semi-custom and custom chemical-feed systems. Planning the installation from the supply tank or liquid source to the injection point and determining the accessories required is critical. Some of the components that go into the chemical-feed system, along with their usage recommendations, are as follows. Flooded suction is always preferred since it is easier to prime the pump, plus there is less chance of a starved suction condition. Limiting the suction piping to 6 or 7 feet and making sure the suction piping is of adequate size for the metering pump is equally important. A suction strainer will trap any impurities in the chemical supply while preventing any dirt or debris from getting to the metering pump’s ball checks. Isolation valves can placed in both the suction and discharge piping of the metering pump in order to isolate it. A calibration column (drawdown cylinder) mounted in the suction line can be used to calibrate the metering pump. Many pumps are provided with internal relief valves, but external relief valves are always recommended to be mounted in the pump discharge and piped back to the supply tank. Back-pressure valves are necessary when the metering pump does not have a back-pressure device or the system does not have back pressure. Check valves in the discharge piping will prevent backflow. A pressure gauge can be placed in the discharge piping in order to view system pressure. A pulsation dampener will provide smooth, laminar flow and prevent water hammer. Injection quills make sure the chemical is adequately dispersed. A control panel with NEMA-rated enclosure (12, 3R, 4, 4X, 7) and a main disconnect that features Hand or Auto mode (HOA), or on/off switches with running lights will provide local control for the system. All of these recommendations and components need to be reviewed when the chemical feed system is being designed, and who better to be able to size and select them than the designer of the system and the manufacturer of the components? With all of this in mind, design engineers should realize that no one is better qualified to assist in and successfully integrate pumps and components into a chemical-feed system than the designer and manufacturer of those pumps, mixers and components. Because of their familiarity with the system and its components, the manufacturers are also able to remediate any maintenance and repair needs quickly—often with the ability to solve an operational problem with a single phone call.Conclusion
So, the overriding question for the facility operator becomes: what is the best way to construct a complete chemical-feed system for use in a power plant, using components that are acquired from a hodgepodge of suppliers, or creating one with components that come from a single-source manufacturer, the one that actually builds the system’s pumps, mixers and other equipment? The answer should be obvious. When building a chemical feed system for use in power generation—the reliable operation of which is imperative to the creation of indispensable electricity for use in the national power grid—it’s best to rely on the expertise and experience of the manufacturer of the actual equipment, someone who has the knowledge to build the system correctly and the ability to quickly solve any problems that may arise.
To read other Efficiency Matters articles, go here.