Plant operators can improve coagulation and flocculation applications to reduce water turbidity and increase purity.
Fluid Dynamics
02/24/2017
Some historians say one of the first recorded examples of water treatment occurred more than 4,000 years ago when ancient Egyptians used almonds to coat the inside of storage vessels to help clarify river water. Around 77 A.D., the Romans became the first to use alum (a colloquial name for “hydrated potassium aluminum sulfate”) as a coagulant during water treatment. By the mid-1700s, alum was regularly being used as a coagulant in municipal water treatment activities in England. Almost from the dawn of civilization, people have known the dangers of untreated water—and those concerns remain relevant. The challenge has been to implement treatment systems that result in water and wastewater that will not harm users.
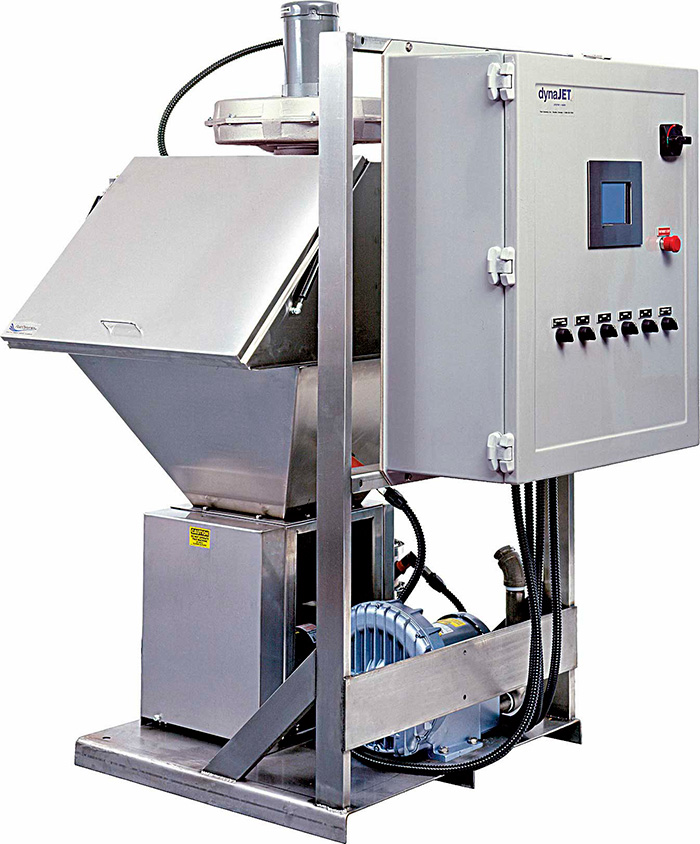
The Challenge
One of the main challenges in municipal water treatment is finding a way to reduce the water’s turbidity to acceptably low levels. Turbidity is a measurement that determines the amount of cloudiness or haziness that can be found in untreated water. Turbidity is caused by the presence of microscopic particles—usually bacteria, dirt, pathogens, metal ions, phosphates, plant materials or minuscule pieces of crushed rock or stone—that are generally invisible to the naked eye. Countries around the world set standards for turbidity levels in drinking water. In the U.S., systems that use conventional or direct-filtration methods for water treatment cannot produce water with turbidity levels at the plant outlet that are higher than 1.0 nephelometric turbidity units (NTU). The World Health Organization has determined that the turbidity level of drinking water should not be more than 5 NTU at any time and should ideally be below 1 NTU. The inherent problem in attempting to decrease the turbidity of municipal drinking or wastewater is that the microscopic particles are so light in weight that they either will settle very slowly over time (as measured in hours, days or weeks), or will not settle at all. This means the water treater must rely on different methods to remove the particles in a timely and efficient manner.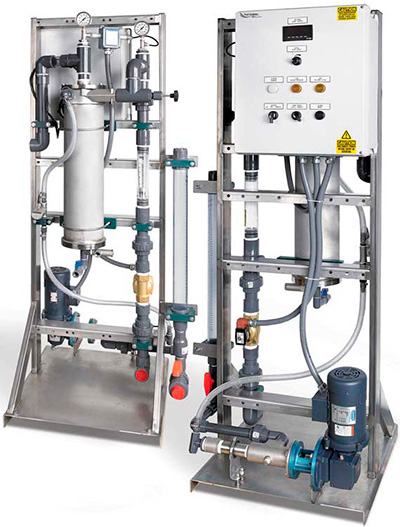
- Ferric chloride: Another name for iron(III) chloride, ferric chloride breaks down when dissolved in water, which gives it the ability to sufficiently form suspended solid particles into flocs.
- Alum: Alum is an astringent compound that allows the negatively charged suspended particles to clump together so they can be more easily removed from settling basins or trapped during filtration.
The Solution
The treatment plant operator has two polymer choices: wet or dry. In both cases, polymer preparation systems can deliver the injection rates that are required and handle the growing number of polymers that are now available, some of which are exceptionally delicate and must be handled with extreme care. Recognizing the needs in this critical area of municipal water treatment, a manufacturer of liquid and dry polymer preparation systems offers a patented liquid and dry polymer blending system. Both offer high-energy, non-mechanical liquid-polymer activation and blending technology designed to effectively activate all types of liquid polymers. The technology produces more than six times the mixing energy per unit volume than some others.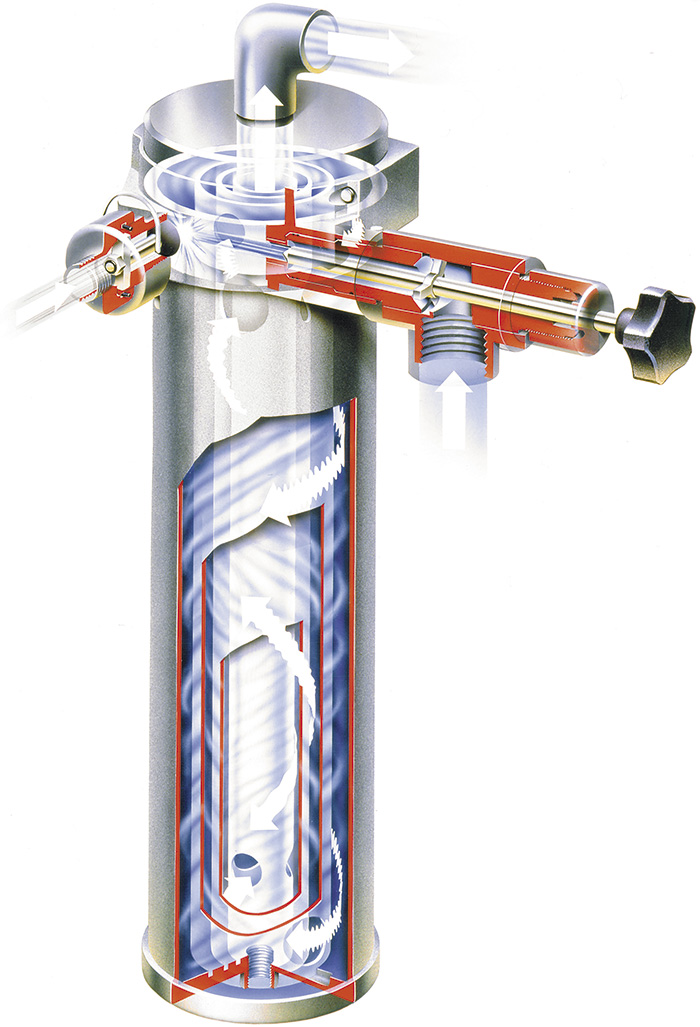
- Stage 1: Pressure drop across a specially designed variable-orifice water-control valve produces a high-velocity water jet, which travels at approximately 70 feet per second. The water jet is aimed directly at, and impinges on, the polymer as it enters the mixing chamber. At this point, the polymer coils up and is not susceptible to damage.
- Stage 2: In the concentric mixing chambers, the newly blended polymer recirculates multiple times for additional exposure to non-damaging turbulence, completing the blending process. The recirculation ensures that the polymer solution is present directly after the point of injection for an ideal activation and blending environment.
- Stage 3: The mixing energy then naturally diminishes in the concentric chambers, while the optimized flow path ensures optimum polymer performance by preventing the polymer from causing a disruption to the three-stage activation and blending process.
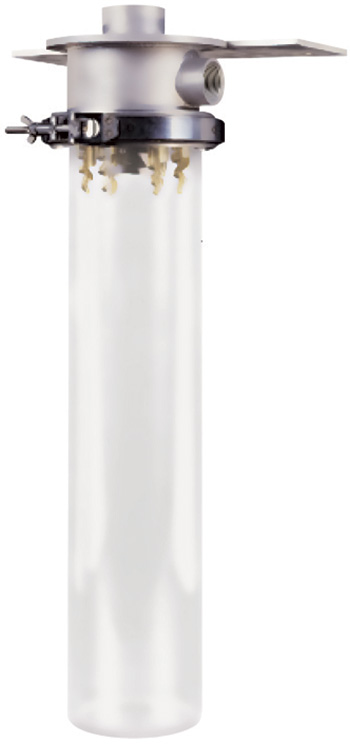
To read other Efficiency Matters articles, go here.