Properly sizing systems, utilizing well-trained operators and performing routine maintenance can help overcome day-to-day challenges.
03/22/2016
Some of the best mechanical systems are designed when engineers focus on efficiency. Parasitic losses in any mechanical system must be kept to a minimum if one desires to maintain an edge over the competition, keep pace with increasing environmental regulations or meet certain sustainability goals. Perhaps nowhere else in industry can efficiency be more appreciated than in pumping systems. Here are 10 tips to aid in improving pump efficiency.
1. Conduct an energy audit and life-cycle cost estimate of new or existing systems.
Before replacing a worn-out thickener underflow pump or a troubling absorber recycle pump with an exact make and model, perform an energy audit to find the true cost of operation. Do not be afraid to consider the use of new and alternate technologies. Though many require higher initial capital investments, the life-cycle cost may prove more beneficial to the cost center. For example, many air-operated pumps are being replaced with more energy-efficient electric diaphragm or electromechanical membrane type pumps. These newer pumps are not only great energy savers, but they also are controllable and provide regulated flow not possible with air-type pumps. Remember: greater energy efficiency, less downtime, less maintenance and lower operating costs all make their way to the balance sheet.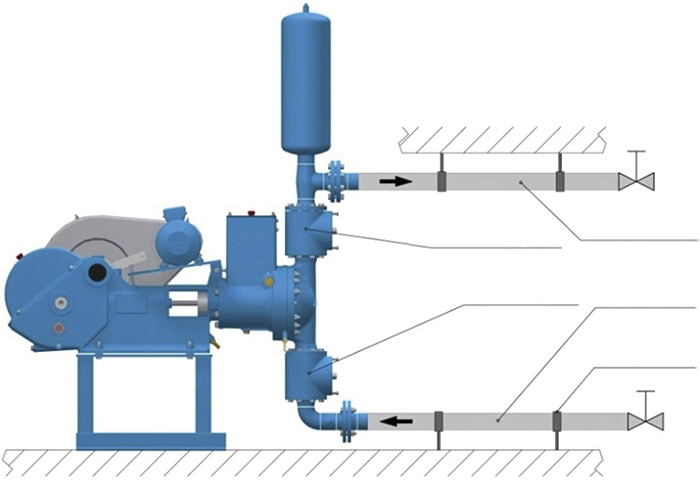
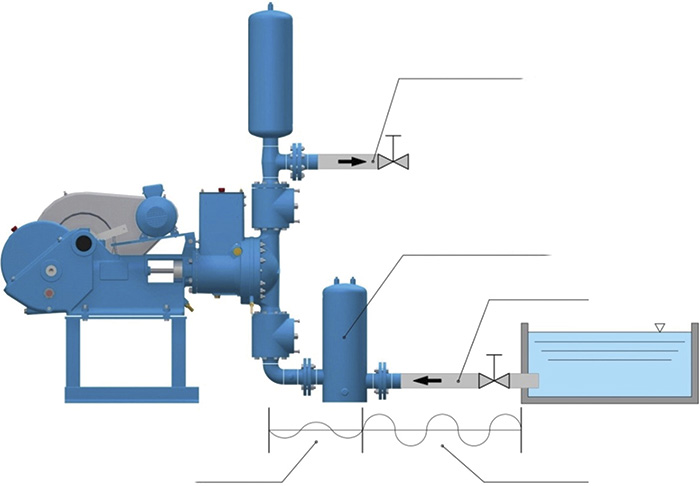
2. Use gauges to monitor pump performance.
Gauges can be used in both the suction and discharge side of the pump. These serve as the best early warning of wear or poor performance caused by blockage or system anomalies. A low discharge pressure could signify wear on internal pump components, leading to reduced efficiency. The gauges must be monitored and trigger maintenance or other remedial action when readings trend beyond the established control limits.3. Know the limits of the pump and materials of construction.
Abrasive wear of internal components such as valve seats, check balls, impellers, gears and pistons should be minimized by choosing the correct materials. When these internal components wear, efficiency is lost and, as is the case with some pump types, their operating point on a pump curve changes and does not necessarily match the optimal system curve.4. Properly size the pump for the application.
When faced with a new or unique application, it is often difficult to resist overdesign. No one wants to be the supplier that underperforms in a system. The tendency to overdesign—a little extra horsepower or a larger-than-necessary discharge pipe spool—can create waste and inefficiency. Look into pipe modeling software to help determine required flow rate and discharge pressure.5. Properly size the piping.
In addition to keeping costs at a minimum, proper pipe diameter can prevent sedimentation or settling of slurries. The velocity of the pumped medium depends on density, solids content and grain size of the particulate. For most sewage applications, a velocity of 1.8 meters per second (m/s) is sufficient to prevent sedimentation. Sludge with higher content of solids requires higher velocity. An optimally sized discharge line would be one that is large enough to control excess backpressure but small enough to prevent sedimentation in the pipeline (see Equations 1 and 2).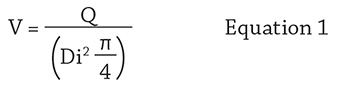
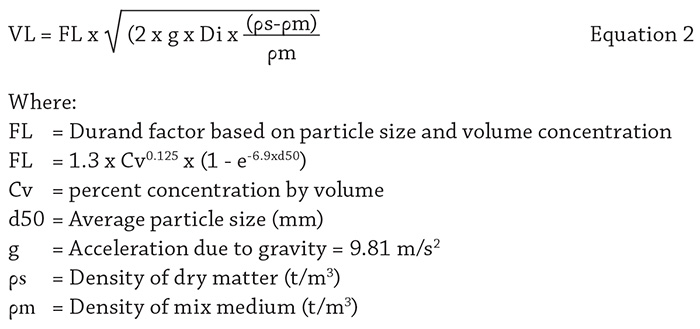
6. Properly design the suction piping.
Feed lines should be connected in a manner that prevents force from being applied to the pump. Use supports, hangers or other means to carry the pipe's weight. Use connections that can accommodate expansion forces or other forces created by minor misalignment. Use strainers to catch large particulate matter. Avoid air locks (air pockets) in the suction line created by elevation changes. Use a single diameter suction piping to promote stable fluid flow. Lay out the suction piping in such a way that minimizes the amount of 90-degree bends and allows for the shortest line possible. This will increase the net positive suction head available (NPSHA) and improve pump system efficiency.7. Use suction stabilizers and discharge pulsation dampeners.
The pulsation dampeners remove pulsating flows from reciprocating-type positive displacement pumps, ensuring a smooth and continuous fluid flow. The result is reduced pipe vibration and longer gasket and seal life. In the case of diaphragm pumps, suction stabilizers act as accumulators and reduce pressure fluctuations that can increase diaphragm and valve wear. Use suction stabilizers to increase the NPSH value, which will decrease the energy required to draw fluid into the pump.8. Isolate mechanical vibration
Construct a proper foundation to which the pump can be securely anchored. Install quality vibration-dampening mounts and anchoring hardware.9. Conduct routine maintenance.
Timely replacement of wear parts results in greater pump efficiency. Pumps work best when valves seat properly or when component clearance is within the manufacturer's specification. In the case of corrosive media, periodically flush pumps with clean water or other acceptable media per the manufacturer's guidelines.10. Train the operators.
A well-trained operator is vital for efficient operation. Train these key staff members to ensure that system performance is monitored and that routine maintenance is performed to keep the system operating at its most efficient levels. Discourage "knob turning" or ill-advised process control adjustment as a means of keeping a poor-performing system in operation. Instead, train operators to report issues with system pressure or flow rate, and organize the necessary maintenance or remedial action.
To read other Efficiency Matters articles, go here.