Last month’s column (Pumps & Systems, October 2014) described the collection of data when assessing a system with no control. In this column, the plant operating data will be used to determine a baseline of how much energy is used for the process. Personnel and outside experts can then look for ways to improve the system and minimize costs. Assessments are based on the idea that a system was originally designed to meet a specific set of requirements, but during the design process, several unknowns were incorporated. Once a plant is operating, the unknown design factors become known, and the system can be improved. This column explains how to perform the baseline calculations and develop the energy cost balance sheet to determine how energy is used by the system.
Energy Cost Balance Sheet
During the system walk-down, the assessment team discovered that the operators continually operate Pump BTP-01. Once the batch tank fills, a bypass to Supply Tank BTS-01 automatically opens when all fill valves close to ensure that minimum flow is maintained through Pump BPT-01. In previous columns, the energy cost balance sheet was discussed as a way to obtain the actual cost of operation for each item in the system. The energy cost balance sheet calculates the energy consumed by the pump to operate the system along with the energy consumed by the process and controls to make the product or provide the service. In this system, the system control consists of running the pump in the bypass mode when the tanks are not being filled.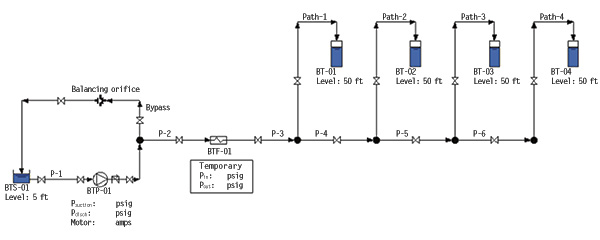
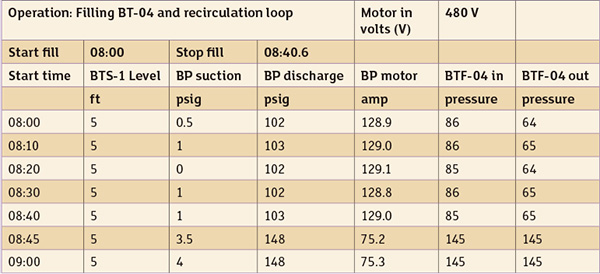
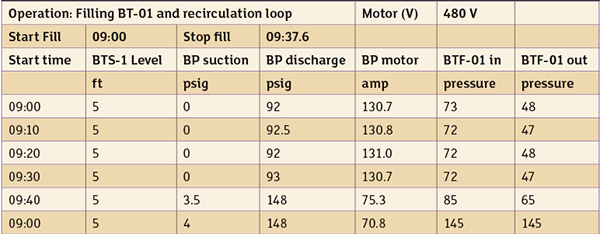
Pumping Elements
The pumping power is calculated using Equation 1. Using the assessment data for filling Batch Tank 4 and with the manufacturer’s supplied data, Equation 1 can be used to calculate the power consumed by the batch pump in each operating mode.

Calculating Pump & Motor Power Consumption
Using the operating data collected during the system assessment for filling Batch Tank 4 (Table 1) and Equation 1, one can determine the power requirement for the batch pump (see Equation 3).
