Depending on the type of material being handled, especially the amount of abrasives and solids, ePTFE could be the best diaphragm material.
Garlock Sealing Technologies
11/21/2017
Air operated diaphragm pumps are used in many applications requiring abrasive and chemical resistance. When both are needed, an elastomer with some chemical resistance, or a polytetrafluoroethylene (PTFE) diaphragm with an elastomer backing, is typically used.
.jpg)
_0.jpg)
Test Results
Internal testing was conducted to compare the performance of ePTFE composite diaphragms with two-piece, rubber-backed PTFE diaphragms (see Images 1-5). It involved two identical 1.5-inch inlet/outlet air operated double diaphragm (AODD) pumps at the same elevation and air inlet, media inlet and outlet pressures. One was fitted with an ePTFE composite diaphragm, and the other with a two-piece diaphragm with PTFE facing the media and a thermoplastic elastomer facing the air side.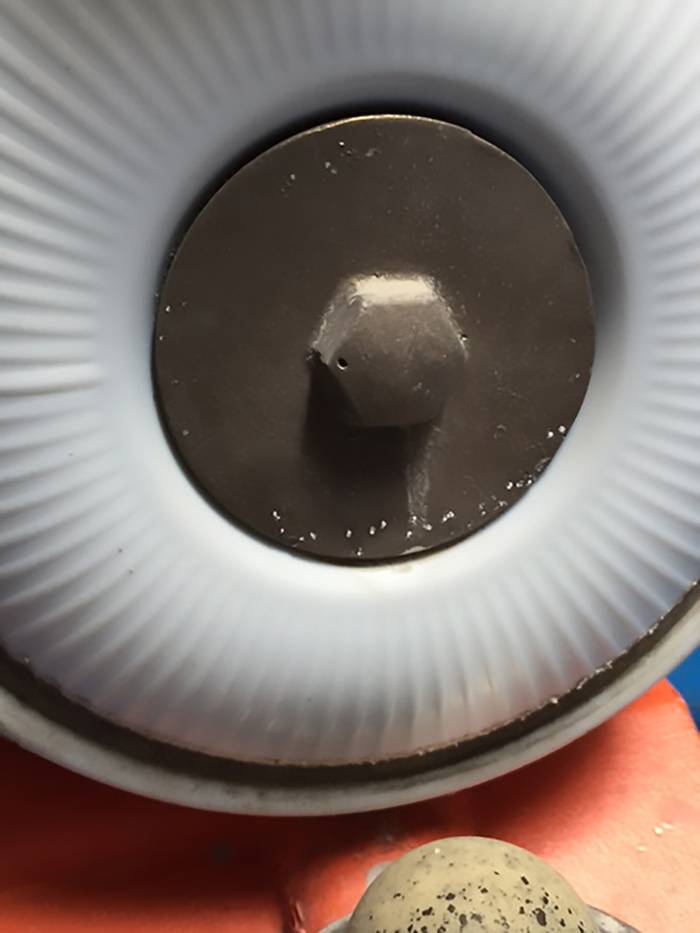
.jpg)
1. Chemical Cleaning Company
Delta Tech Service Inc. in Benicia, California, specializes in decontaminating oil refinery equipment. The company designs and fabricates skids that utilize two 3-inch AODD pumps joined at the manifolds, allowing users to simultaneously operate one or both pumps. One of the challenges in the field was the short life of the fluoroelastomer diaphragms that came with the pumps. Ethylene propylene diene monomer (EPDM) and conventional skived PTFE diaphragms with thermoplastic elastomer backings were used, but none lasted longer than a 30-day rental period (see Images 6-7)..jpg)
.jpg)
2. Zinc Refining Company
Extracting metals from a refining process requires pumps that can move various chemicals, metal fragments and dust particles. A U.S.-based company that specializes in the extraction of zinc uses 10 AODD pumps to move slurries of sulfuric acid (up to 90 percent concentration), hydrochloric acid (up to 36 percent concentration), Di-(2-ethylhexyl) phosphoric acid (D2EHPA), kerosene, metal powder and metal flakes. AODD pumps were used because of their ability to handle solids and move to different areas of the process.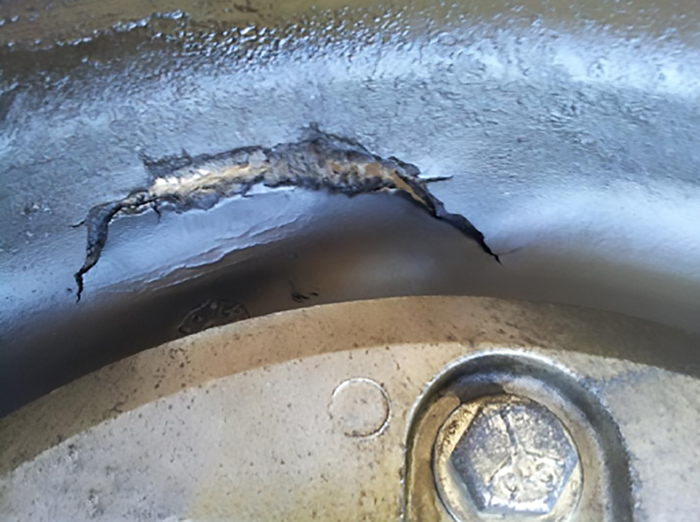
.jpg)
3. Mining Company
A precious metals mining company wanted to get better life out of the diaphragms in its vertical AOD pumps. These pumps operated outdoors at temperatures ranging from 15 to 100 F and inlet pressure of 40 pounds per square inch (psi) for more than 20 hours a week. The media typically consisted of 70 percent hydrofluoric acid concentration.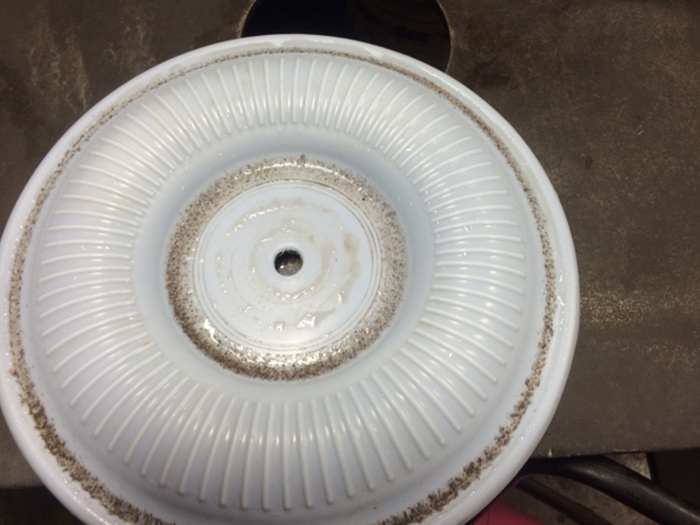