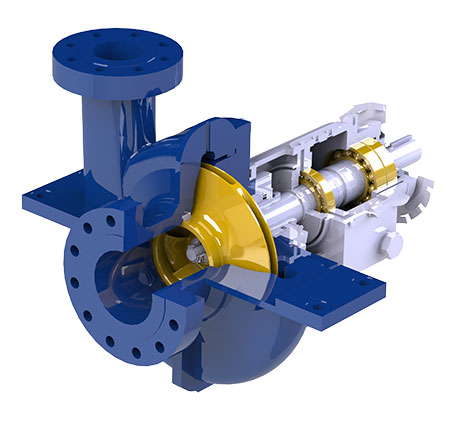
In 2008, a large oil refinery in Texas purchased more than 20 complete pump trains, including motor skids, pumps and all the components. They were ready to install and go directly into operation, but they were stored in a laydown yard awaiting a large decoking project that had been delayed. The pump trains included a variety of sizes for various applications.
The Wrath of Harvey & Imelda
While waiting on the delayed project, the storage yard suffered severe water damage when Hurricane Harvey, a category 4 storm, made landfall in Texas in August 2017, causing catastrophic flooding throughout the area. The pump trains had never been moved, and except for having the rotors turned occasionally, they had not had much preventive maintenance performed during those nine years sitting in the outdoor storage yard.
In 2019, Tropical Storm Imelda caused further damage, complicating the situation. In early 2020, the energy company sent the weather-damaged equipment to an aftermarket service provider in Beaumont, Texas, for complete evaluation, repair and performance testing.
Repair Challenges
All 20-plus pump trains had similar damage, but each one had its own repair scope (Header Image). It was not a copy and paste repair plan—each of the 20-plus pumps required a specific plan of action. The aftermarket service provider was able to create plans to appropriately refurbish all of the pumps. The plan ensured that all pumps would be tested to verify proper mechanical and hydraulic performance.
The aftermarket service provider initiated reverse engineering on all equipment and major components while sending the motors to a vendor in Baton Rouge, Louisiana. The vendor provided an archive of its library of parts and build materials and modeled all the repairs for further use, if needed, for the same type of equipment.
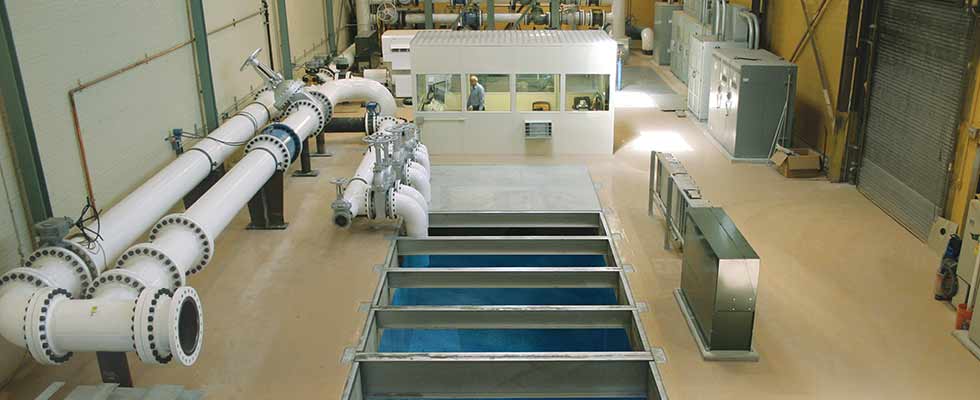
Performance Testing
Factory-run vibration tests, along with complete performance testing, were provided in-house at a Hydraulic Institute-approved pump test lab in Chicago (Image 2).
To verify the quality of each repair scope, the aftermarket service provider offered to include a mechanical run test of each pump. The mechanical run test would verify that the refurbished pump operated with minimal vibrations and expected thermal increases during operation. This test would provide assurances to the end user that when it comes time to install each pump, reliable performance and an extended life span can be expected.
In addition to a mechanical run test, the test facility provided a complete hydraulic performance test. This helped the end user confirm that the pumps would meet the process conditions necessary to perform when installed.
If the pump was found to not meet its performance criteria, subsequent action could be taken to correct the performance issue or manage the use of the pumps based on these findings.
The assurance of mechanical performance and hydraulic performance provided decision-making information to the end user, setting them up for long-term success with these pumps and building trust in the quality of the repair.
Protection From the Elements
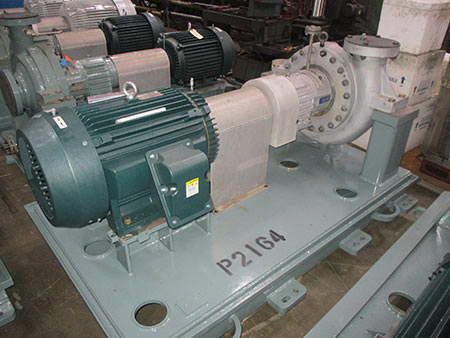
The fully refurbished and performance-tested equipment is now stored in an indoor storage facility rather than an open yard with exposure to the elements.
The 20-plus pump trains were prioritized into three sets. The aftermarket service provider was expected to deliver all the refurbished equipment in record time—less than one year (Image 3). Even with delays caused by a global pandemic, the aftermarket service provider was able to deliver the first priority set, with the second set delivered a month later, and the third set delivered within the following month. Each had to be individually assessed with specific plans of action and specific performance testing.
Some of the repairs required were more intricate and meticulous than others. These are complete pump trains and not an individual pump repair. The aftermarket service provider also repaired all the skids, all the seal changes, all couplings and coupling guards, the bases and the foundations.
Case Study: Batch of 21 Pumps Tested & Validated Under Expedited Conditions from Hydro, Inc. on Vimeo.