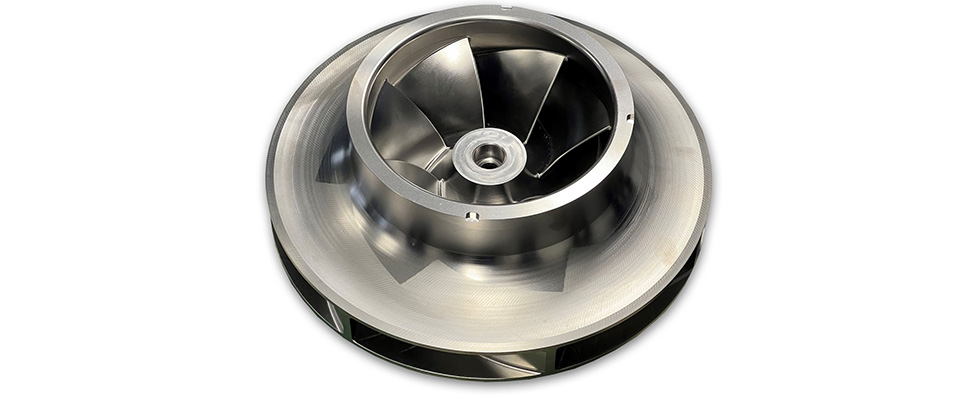
Mainstream industries are increasingly using 3D printing—or additive manufacturing (AM), as it is commonly termed—to create required components with a short lead time. The technologies included under the AM umbrella are used frequently in pumps and turbomachinery.
Additive manufacturing enables three key advantages: part customization, faster and better parts and enhanced performance, all contributing to sustainability. By enabling a pump or turbine to continue operating with just a few replacement AM parts, the service life of the equipment can be extended, eliminating the need for raw materials for a full replacement. This is especially true for legacy equipment, where parts stocks have been exhausted or when the OEM support may not be available. Coupled with 3D scanning and advanced reverse engineering tools, the use of AM is also significantly reducing the lead time for low volume parts when the original drawings are not available.
Exploring Different AM Processes
Laser powder bed fusion (LPBF), also known as selective laser melting (SLM), is used in the manufacture of spare parts, predominantly in gas turbines and pump parts such as impellers. This technology is especially suitable for working with metallic materials, resulting in high integrity, high strength and durable parts for corrosive and high-temperature environments. LPBF provides exceptional geometric freedom, enabling the precise production of complex parts required for high-speed turbomachinery in a toolless manner.
Laser metal deposition (LMD), or directed energy deposition (DED), which uses wire or powder as feedstock, is a technology increasingly used in parts manufacturing and repair. DED processes, including wire arc DED, offer higher deposition rates, enabling the rapid production of near-net shape geometries that are subsequently machined into finished parts. Unlike traditional machining from large blocks of forging, the near-net shape approach reduces material waste and minimizes the impact on natural resources. Additionally, combining DED capabilities with machining creates a hybrid solution that shortens production cycle times. This technology supports on-demand parts manufacturing for aftermarket needs, offering opportunities to reduce inventory.
Increasing Applications With New Materials
One of the challenges with AM is working in accordance with the list of materials that have been qualified and approved in industrial settings. Processes that use wire or powdered feedstock are continuously evolving to include new materials. For example, AM vanes made using IN738LC, a material complex by design, can withstand extreme temperatures in a gas turbine. As this process advances, the number of applications that can benefit from AM is increasing each year, and that trend is set to continue.
Using new materials to create parts that are better than the originals will most often improve reliability as well as efficiency, reducing energy costs and the carbon footprint of the business. Moreover, these parts can extend the periods between overhauls, further reducing the cost of ownership.
In addition to metals and ceramics, 3D printing of polymers is also being used to create patterns for casting new parts. This significantly speeds up the manufacturing process and enables changes to be made quickly if necessary. Polymers are also used in prototyping new components, and 3D printing is hastening this process and reducing lead times.
Faster Manufacturing & Improved Flexibility
The toolless nature of AM is enabling parts to be produced closer to where they are required. The knowledge and expertise required to create the design can be remote from the location making the new parts, improving sustainability as well as reducing lead times.
However, a significant challenge to rapid parts supply is the efficiency of global logistics, which has been highlighted by several incidents recently, so the ability to quickly move the manufacturing source for a component can have several benefits. AM offers greater supply chain flexibility, which again optimizes the on-time delivery of new parts to the end user.
Pushing Standards for Wider Acceptance
As a relatively new technology, standards and regulations are still catching up with the pace of the rapidly evolving AM landscape, which is holding back implementation in some areas. As more sectors appreciate the benefits of AM, the associated regulations will be updated to cover these processes.
This will be boosted further as more data becomes available for the long-term performance of parts in the field. While the uptake of AM technology is very positive, there are some markets that are skeptical, and this will only be overcome as more evidence is delivered to support the adoption of this technology.
To that end, there will continue to be a need for collaboration between the technology pioneers and the prospective end users who will drive demand. AM is a complimentary technology that can offer advantages to industry, especially for repairs and retrofits.