Pipe bursts due to transients and surges are common. Not only are the maintenance costs of these repairs high, but when adding possible litigation for third party damages combined with the potential cost of water loss, another pipe burst can have big consequences. Surges, or transients, are the result of a rapid change in liquid mass velocity within a pipeline. This kinetic energy, released as pressure, acts to expand the pipe diameter and can destroy fittings, pipes, valves, instrumentation and pumps. Pressure waves travel the length of the pipeline of the offending device, then reverse direction. The waves move at a constant speed until they meet a barrier. The reflected and incident waves may superimpose each other to produce a more compounded wave pattern that includes double peaks and double troughs. The consequence of improper protection from surges or transients could be a pipe burst or equipment failure and result in damage, water loss or litigation. Transients, surges and the resulting pipe bursts can be caused by numerous events: loss of power at a pump station, pump station programmable logic controller (PLC) malfunction, single-speed pump motors without adequate pump control valves or the rapid closure of isolation valves.
.jpg)
Pressure Relief Valves
A diaphragm actuated, hydraulic pilot operated pressure relief valve responds to opening only when a system is over pressured, typically 10 to 15 percent over the normal operating pressure. If an overpressure or surge pressure occurs, the relief valve opens quickly to dissipate the surge by discharging water to atmosphere. When the system pressure has stabilized, recovering below the surge pressure, the pressure relief valve closes at a controlled rate and normal operation of the system resumes. Rapid or uncontrolled closure of a relief valve may result in secondary surges in the system. Closure rate should not be too fast to create closing surges and not too slow to result in excessive relief water loss.Surge Anticipating Relief Valves
Standard or single pilot relief valves only open when the system pressure exceeds the relief pilot setting. In a pumping system, where an unexpected pump shutdown occurs, the mass velocity of the water moving away from the pump will initially create an excessively low pressure within the pumping system. This low pressure surge wave will occur prior to an eventual returning high pressure surge wave. The time to open and the capacity of the relief valve opening under this resultant high surge may not be sufficient to adequately dissipate the system surge, resulting in additional and repeated surge waves created within the system. The time, frequency and severity of these waves may become catastrophic and end in a pipe burst or other system failure, even in system where a relief valve was installed and satisfactorily sized. Having the ability to anticipate a surge event would allow the valve to respond and open more quickly and effectively to a surge event.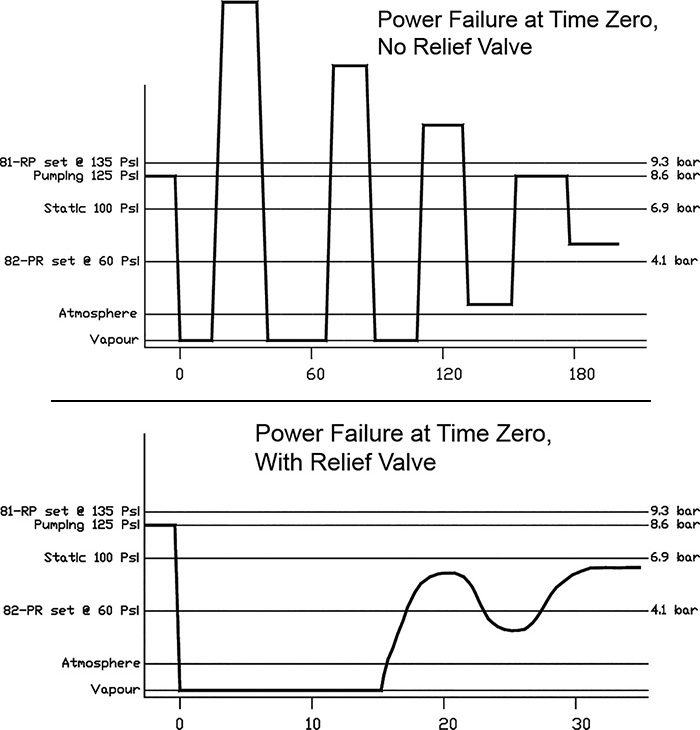
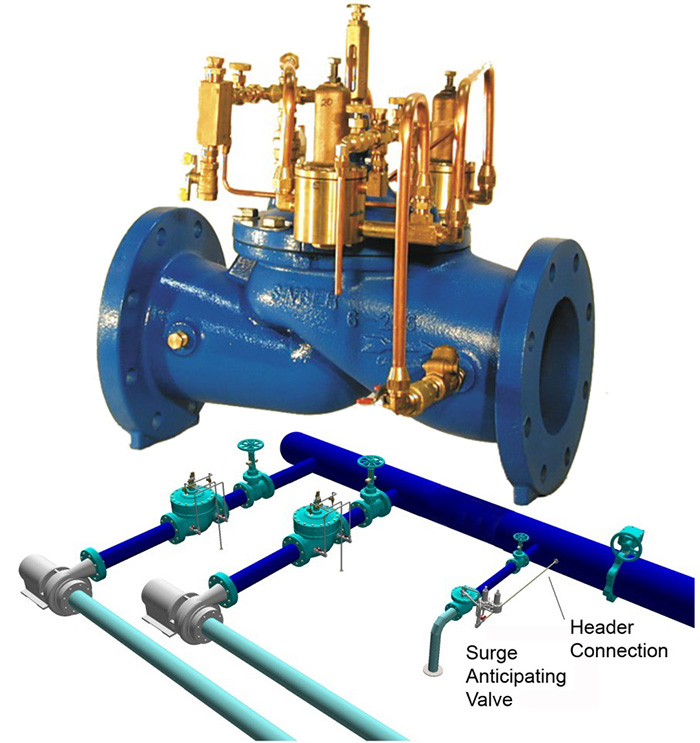
Electrically Timed Closure After Power Failure
This valve is similar to the surge anticipating relief valve, with the exception that the low pressure pilot is replaced with a solenoid valve. All other sizing protocol and design criteria remain the same. No static pressure is required as the valve closes on a timer. The valve opens because of either power loss or by way of the high pressure pilot. If power loss is the major concern, then this style of valve can be an excellent selection. Timing for the solenoid to close is normally coordinated with the critical period—the time it takes for the surge return. Always consult with a transient specialist for sizing and selection concerns.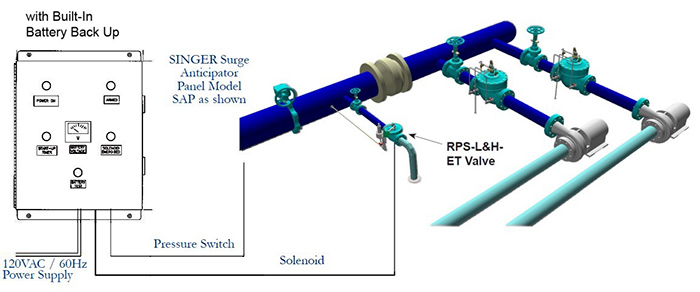
Rate of Rise Relief Valve
Surge anticipating valves based on the detection of a system pressure abnormality leads to another surge anticipating valve model, the rate of rise relief valve. Valve opening pressure relief on a rapid pressure rise system, even before a high pressure relief setting is reached, anticipates a surge event to allow the valve to respond and open more quickly and efficiently to a surge event. Rate of rise relief valves add another safety feature to standard relief valves. The valves open when they detect a sudden change in pressure.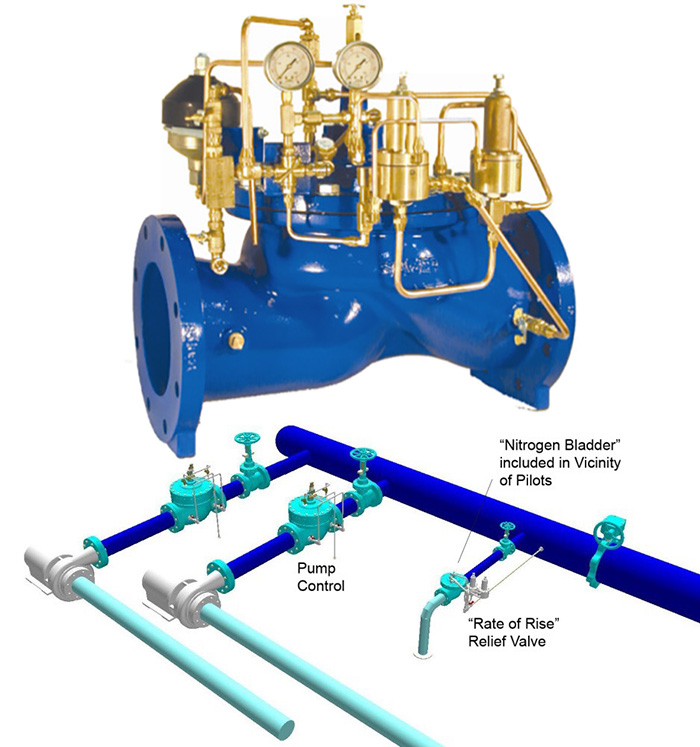
Booster Pump (Inline) Control
Booster pump control (BPC) valves are located in line, downstream of the pump. When started, the pumps start against a closed valve. The solenoid is then energized, opening the BPC. At pump shutdown, the solenoid valve is de-energized by the system control to put the valve into closing mode.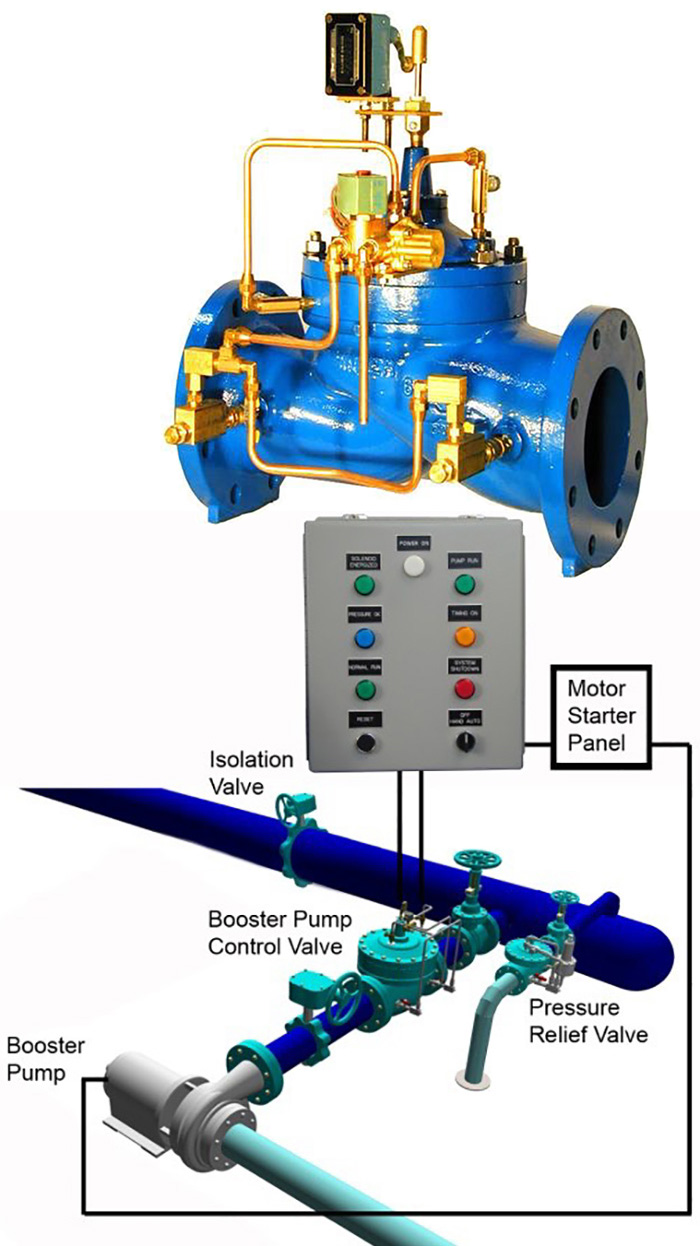
Deep Well (Bypass) Pump Control
If site conditions permit, deep well (DW) pump control valve solutions can be a very economical and practical solution to pump control. This type of valve requires some static pressure downstream to work effectively. Elevations are the best method to ensure the static condition, which should be a minimum of 100 feet. This static pressure applies pressure to an inline check valve until pump pressure overcomes this check valve and allows flow into the distribution pipe.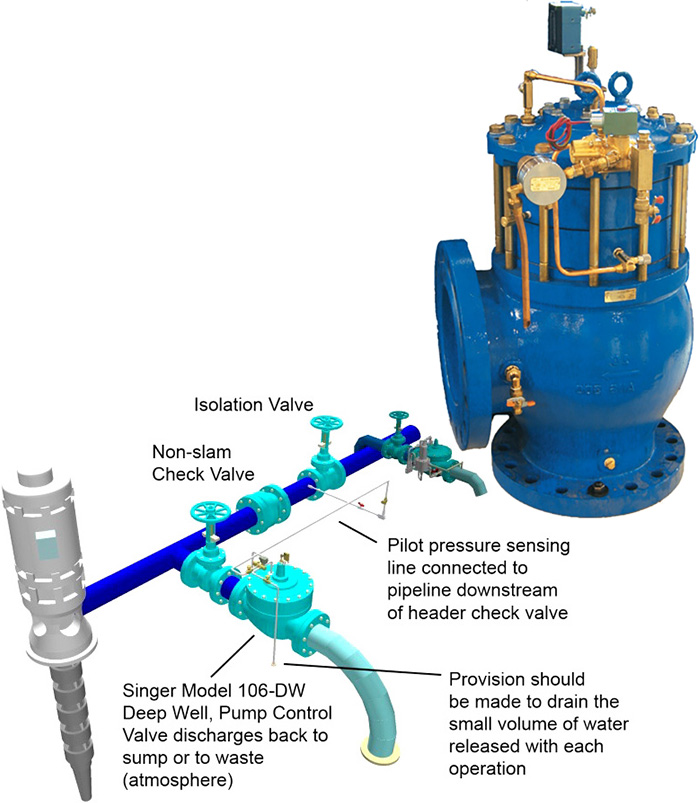