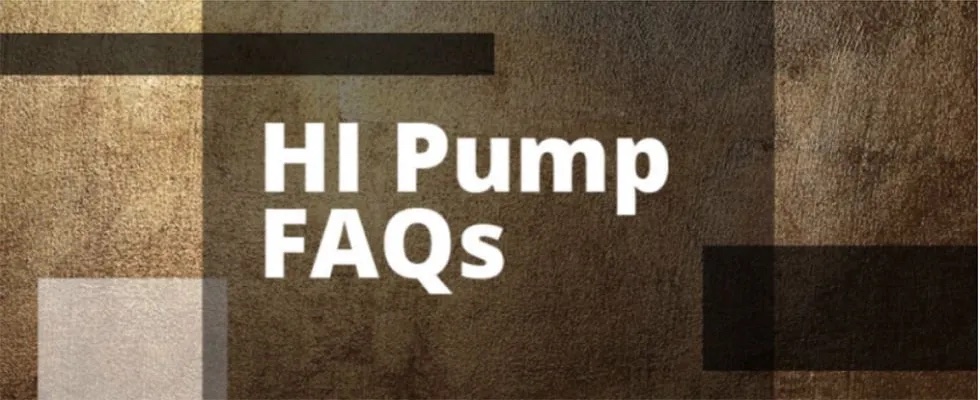
Electrically commutated motors (ECM) are synchronous motors that require a VFD to operate. Synchronous motors operate at the running speed of the frequency of the applied voltage. As a result, synchronous motors do not experience slip. There must be some excitation to start, though, as the speed difference between the stationary rotor and the rotating magnetic field (RMF) in the stator will not allow their poles to lock on startup. ECMs are nonexcited, synchronous motors, meaning they use ferromagnetic materials in the rotor to interact with the stator RMF.
In this type of motor, there is no induced current in the rotor, which eliminates the induction losses (compared to typical induction motors) and results in increased efficiency, higher power density and lower heat generation. However, the system requires a VFD. In pump applications, these motors are typically used in lower power applications, where they provide the greatest part load efficiency benefits, but the size and coverage are ever-growing.
Image 1 illustrates what an ECM generally looks like, and it does not look much different than an induction motor. There are many synchronous motor technologies that can fit under this umbrella term; for a more in-depth exploration, refer to the Hydraulic Institute’s article, Driver Technology for Variable Speed Applications, at pumps.org.