Because cavitation is unavoidable in pump operations, understanding how to reduce it using NPSH calculations is necessary to maintain pump functionality and health.
08/05/2015
Understanding net positive suction head (NPSH) and cavitation is essential for plant managers, pump manufacturers and operators. Proper NPSH calculations are vital for preventing cavitation and ensuring proper pump functionality. The following 10 facts about NPSH can help end users improve system operation and efficiency.
1. Analyzing NPSH margins can help reduce cavitation.
Cavitation is defined as the partial evaporation of a liquid in a system. Vapor forms when the static pressure in a liquid's flow drops below the vapor pressure of that liquid. A two-phase flow occurs when a vapor bubble appears and fluid evaporates. When these bubbles enter a region where static pressure exceeds vapor pressure, they will implode, causing cavitation. These bubbles can cause cavities that impair the head and efficiency of the pump, creating excessive noise and vibration. Cavitation erosion can be detrimental to the pump's head and efficiency. Damage to ancillary components, such as bearings and seals, from higher vibration is also likely. The region of the lowest pressure generally occurs around the leading edge of the vane, and this is where cavitation will most likely occur.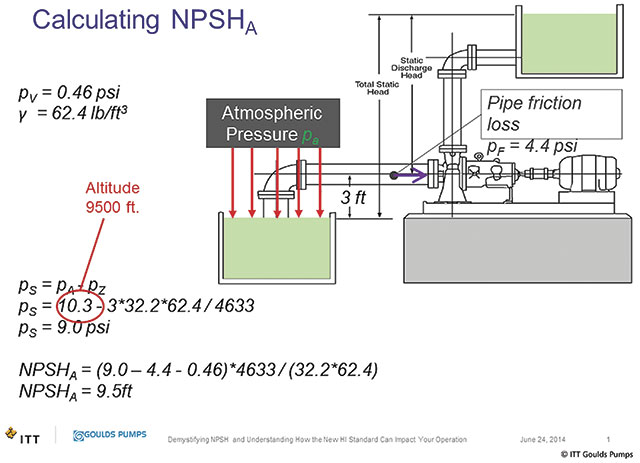
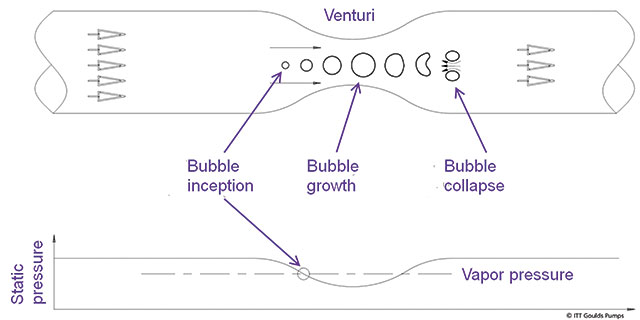
2. NPSH has two main components.
NPSH distinguishes between the pressure available to give to the pump (NPSHA) and the pressure required by the pump (NPSHR ) to limit the reduction of pump head to an acceptable level.3. NPSHA requires an in-depth calculation.
NPSHA is caused by atmospheric pressure, tank elevation or pressure inside a tank. This measurement must be calculated by the user. At sea level, the atmospheric pressure provided is 14.77 pounds per square inch (psi), or 1 bar, which fluctuates depending on elevation. Additionally, the fluid vapor pressure will vary with temperature. With this calculation, the manufacturer must convert pressure to feet or meters and consider the fluid temperature and elevation surrounding the pump.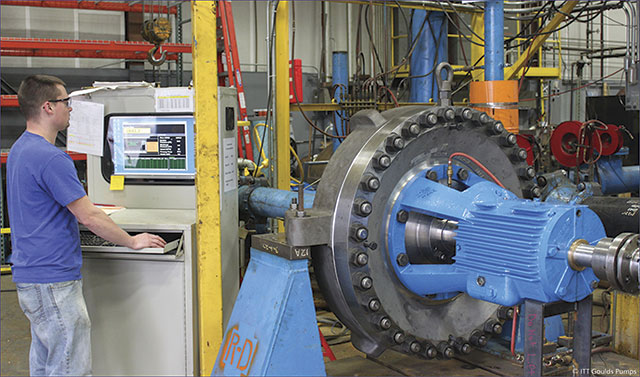