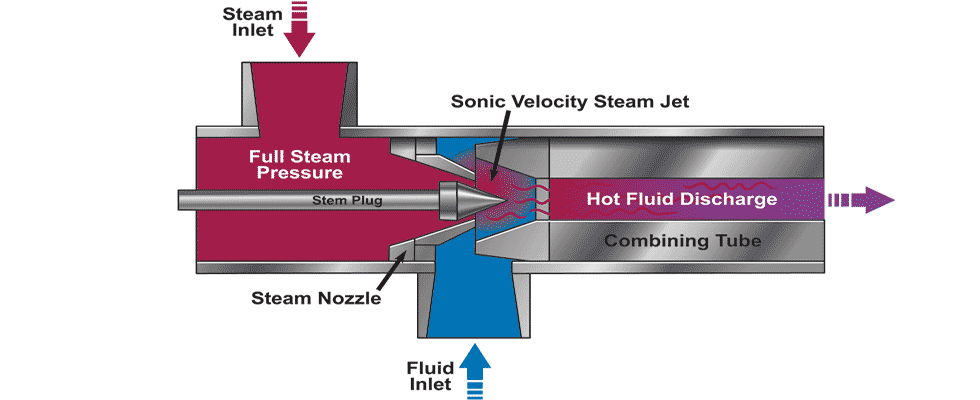
Chemical slurry production is critical in various industries, such as pulp and paper, water treatment and mining. It involves heating a mixture of solid particles and liquid to produce a high-quality product. However, chemical producers often face challenges, such as uniform heating, erosion, corrosion and fouling, which can affect the quality and efficiency of the production process, increase maintenance and lead to equipment replacement. Direct steam injection (DSI) technology is a method used to solve these challenges effectively.
What Is Direct Steam Injection?
DSI is a process that involves injecting steam (through a specially designed steam injector) directly into a liquid or slurry to heat it. This technology has become popular in the chemical, food and pharmaceutical industries, where precise temperature control and efficient heat transfer is critical.
The steam injector is a nozzle designed to create a high-velocity steam jet. As the steam jet enters the liquid or slurry, it creates a region of turbulence, which results in efficient heat transfer between the steam and the liquid.
One of the advantages of DSI technology is it provides rapid and uniform heat transfer throughout the liquid or slurry, resulting in consistent product quality. This is achieved by the high-velocity steam jet breaking up any lumps or agglomerates in the liquid or slurry, ensuring the heat is evenly distributed throughout the mixture.
1. Uniform Heating
Uniform heating is essential in chemical slurry production to ensure consistent product quality. However, traditional heating methods cannot produce a uniformly heated product. As a result, the slurry mixture can be complex, with varying viscosities, solid content and chemical properties, resulting in quality issues like product discoloration or inconsistency.
DSI technology solves this problem by injecting steam directly into the slurry. The amount of steam injected into the liquid or slurry can be precisely controlled to achieve the desired temperature. Steam is mixed with the slurry in a specially designed injector, which ensures the steam and slurry are mixed thoroughly and evenly. The direct injection of steam provides rapid and uniform heat transfer throughout the slurry mixture, resulting in consistent product quality.
DSI heaters also provide precise temperature control, which is essential for chemical slurry production. The temperature of the slurry can be precisely controlled by adjusting the steam flow rate to the slurry, ensuring the slurry is heated to the desired temperature without overheating or underheating.
2. Corrosion & Erosion
Chemical slurry production can be complex, as the mixture of harsh chemicals can compromise the integrity and reliability of equipment and pipelines, leading to equipment failure, leaks and safety hazards. One of the challenges in chemical slurry production is corrosion caused by the contact of harsh chemicals with metal surfaces.
However, chemical producers can overcome this challenge using DSI technology, which uses steam to heat the slurry mixture. This eliminates the need for external heat transfer options.
Erosion from suspended solids in a chemical slurry can also be a problem, which compounds the corrosion issue. The erosion sweeps away the corrosion byproduct that protects the cell, exposing new metal surfaces and leading to further corrosion. However, due to its metallurgy, DSI technology can help with erosion by mitigating the corrosion part of the heater’s erosion-corrosion process. DSI technology can also prevent corrosion caused by high-temperature steam and harsh chemicals, resulting in a longer equipment life span and reduced maintenance costs.
3. Fouling & Clogging
Fouling and clogging equipment and pipelines are common challenges in chemical slurry production. This can be caused by the buildup of solids or the precipitation of chemicals in the slurry, resulting in reduced production efficiency and increased maintenance costs.
DSI technology prevents fouling and clogging of equipment and pipelines in chemical slurry production by using steam to heat the slurry mixture. The rapid and uniform heat transfer throughout the slurry ensures no buildup of solids or the precipitation of chemicals. This reduces the risk of fouling and clogging caused by the buildup of solids in the slurry.
Furthermore, DSI heaters can be designed with self-cleaning mechanisms, such as high-velocity steam injection, which can prevent fouling and clogging of equipment and pipelines. These mechanisms ensure the heaters are continuously cleaned, reducing risk of downtime and maintenance costs.
DSI technology is an effective solution to common challenges in chemical slurry production. It provides uniform heating, prevents corrosion and prevents equipment and pipelines from fouling and clogging. These benefits result in higher quality products, longer equipment life spans, reduced maintenance costs and increased production efficiency.
DSI technology is one solution for producers facing challenges with chemical slurry production. Using DSI heaters, they can improve their production process and achieve a higher quality product while reducing maintenance costs and increasing production efficiency.