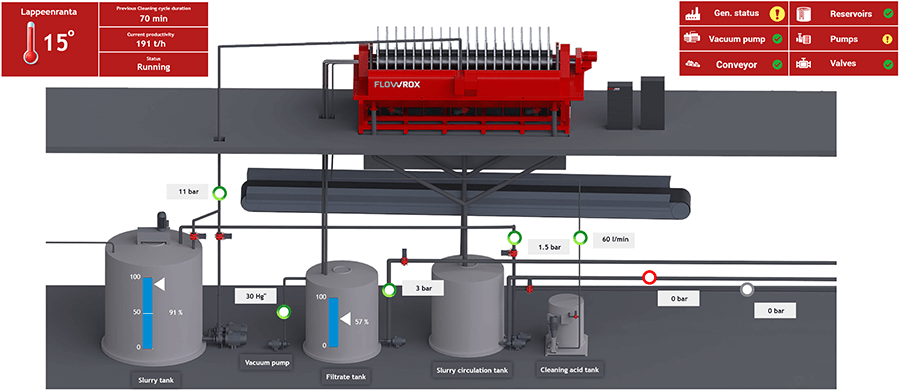
One of the best TV commercials right now is the tax software ad that takes place in a courtroom. The prosecutor’s cleverly crafted closing argument is replaced with the words “Free. Free, free, free, free, free, free. Free.” The defender objects, “Free!” The judge quickly overrules with, “Free… [motions to the prosecutor] free.” With passion, the attorney continues with a rousing string of “free, free, free,” all to the finale of a standing ovation from the spectators and jury. Can you guess what the company wanted to get across? The tax software—it’s free. That’s it. The marketing agency and company execs knew that the “free” message, a major differentiator and feature for the software’s basic tier, was the key message. What better way to enhance that message than to double-down, nay, triple-down, to the nth degree? It feels like the same thing is happening in our industry right now. There is a constant drum of words like: digitalize, intelligent, secure, convergence, open, M2M, scalable, AI and cloud. But in the middle of it all is one singular, convoluted word: smart. Smart this and smart that—but what does that really mean? With “free,” we know that nothing is truly free. It costs someone something, whether it is the company’s resources or a user’s data. So it is with smart. Does smart really mean, well, smart? And how smart? Like, fifth grader smart or Ph.D. smart? To bring some clarity to it all, here are three ways systems and industrial pumps can be smart to varying degrees.
Smart Like a Fifth Grader
For something to be smart, we are assuming that the item’s basic functionality is being intelligently improved in one way or another. A pump’s basic functionality includes turning it on and off, and perhaps modulating its speed. What I would deem next level (or what I am calling fifth grade status) is to use data directly related to the pump to change the way the pump operates. For instance, say you are running a peristaltic pump and metering the dosage flow of hydrochloric acid into a tank of water. This particular “smart pump” has a fluid contact sensor inside the cavity of the pump above the lubricant level. If the pump hose ruptures, the fluid level inside the cavity begins to increase, triggering the sensor. A signal is sent to the motor telling it to stop, an alarm is sent to the appropriate operators, and the pump is saved from unnecessary damage. Without this alert, the pump would continue to run, sending lubricant into the line, increased amounts of hydrochloric acid would spill into the environment, the overall process would be starved of resources, energy would be wasted, unnecessary labor spent, damage done, and on and on. I think we would all agree that adding this functionality would be considered smart, both strategically and technically.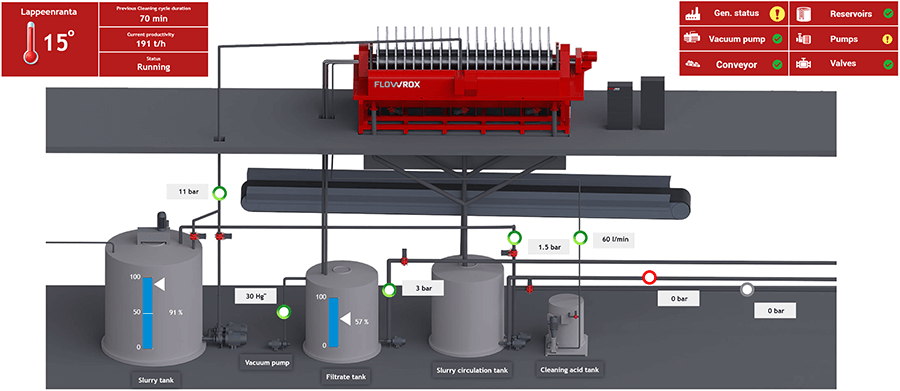
Smart Like a High School Grad
Industrial automation has been a key component for process control for decades, and for good reason. A computer-controlled system is a great way to visualize the process, keep everything running smoothly and change parameters on the fly. In many ways, the advancements in automation have used the principles of “smarts” as a foundation for as long as they have been around. Like the popular cloud-based IFTTT (If This Then That) service, you set up rules and they run automatically. You can try this at home with IFTTT by setting up your smart porch light to turn on automatically when your pizza app notifies you that delivery is imminent. (#ProTip—you are welcome.) What does this have to do with smart pumps? This rule-based approach has been the backbone of industrial automation. If the tank’s level is below 20 percent, then run the pump until the level is 100 percent. If a chemical pump stops, then stop feeding water into the tank, etc. Relationships and programming can then be added throughout the system to create a string of processes. With the advent of computer-operated machines, robots, high-speed optics and faster computers, industrial automation is making it more possible to increase production speeds, optimize efficiency and reduce relative energy usage. For pumps incorporated into an automation system, the smart aspect is related to two key components: the level of programming done for the pump (IFTTT) and the amount and kind of information the pump is providing to the system. Perform more programming, the smarter the system and pump operation will be. Provide more information from the pump to the automation system, the more granular process control programming can be. Often in automation systems, the amount and kind of information available is lacking, and because these are lacking, so are the smarts. Additionally, the programming itself is often limited to binary on/off controls, further limiting the capacity for smarts. Overall, is industrial automation smart? A resounding, “Yes!” But is it as smart as it could be in this technological age? Not by a long shot.Smart Like a Ph.D.
Remember those buzzwords from earlier? This is where it starts to get a lot more exciting. The cutting-edge technology that falls under the smart umbrella is where smart gets really smart—and where the future becomes a bit clearer. But first, a review of the components of these graduate-level smart solutions. In the industrial internet of things (IIoT), industry 4.0 or digital transformation (among many other terms), this higher-level tier of smart incorporates the latest in computing technology, connectivity, data gathering and integration. For the pump, it takes the concept of industrial automation and doubles down on programming and information. For example, say there is a series of pumps continually supplying a large arc furnace with huge amounts of water. The only measurements that exist are flow and pump status (on/off). The automation system can call for more flow and engage additional pumps to meet demand. However, there is no knowledge of the pumps’ efficiency, whether they are contributing appropriately to the process, what maintenance issues they are about to experience, and how to process data for insights in an efficient, intuitive way.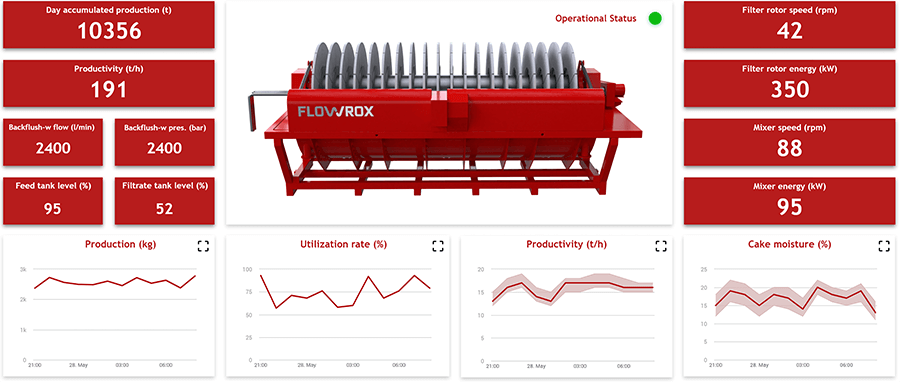
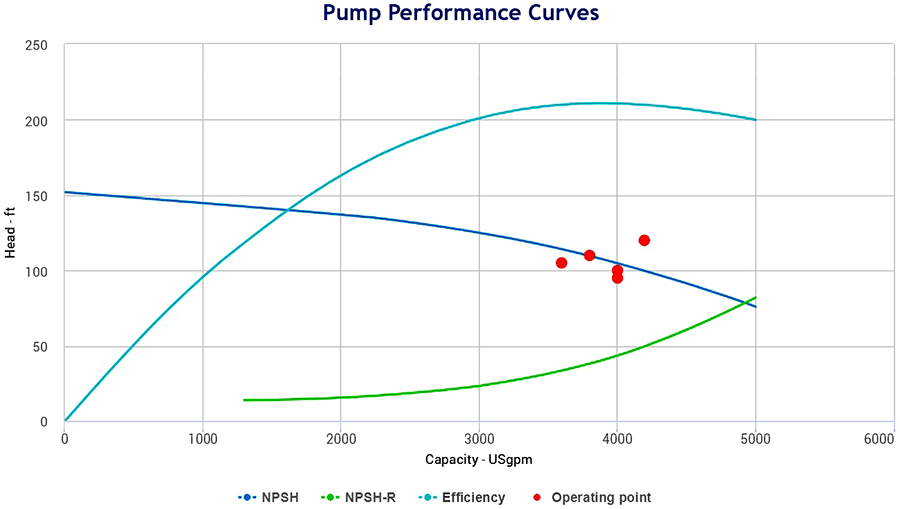