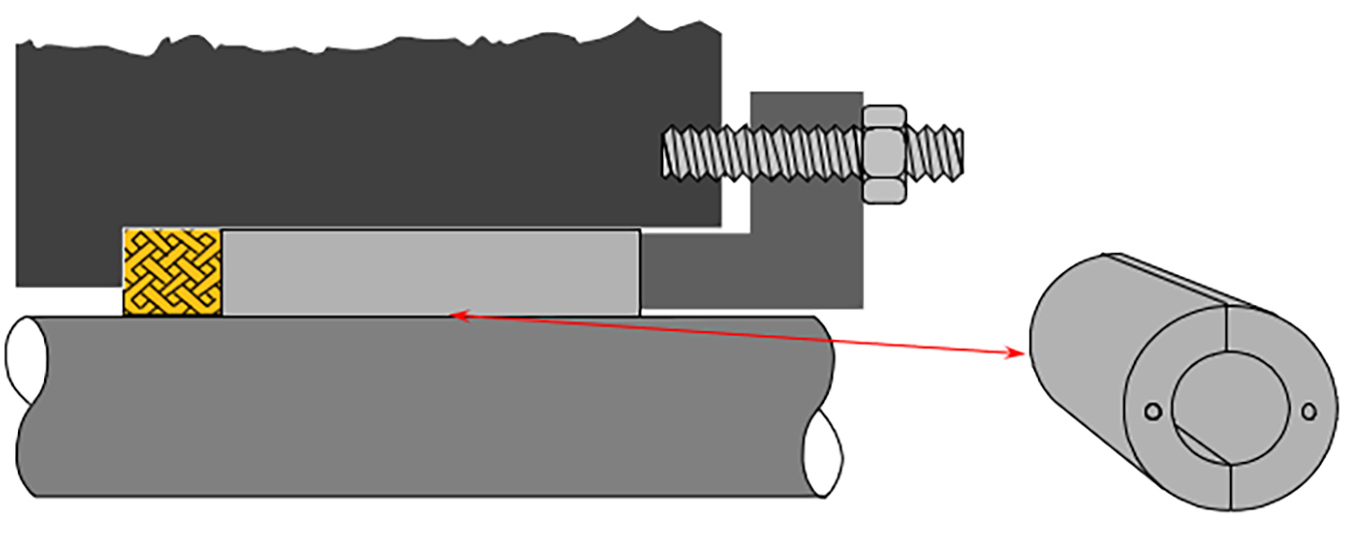
Over the last 100 years, there have been some technological advancements in pump packing—new fibers, lubrication, construction and more. But, even the best designed packing can have poor performance if not properly installed. One of the most important steps that is often overlooked in pump packing installation is inserting the rings into the stuffing box. Poor maintenance practices are sometimes used, and these can be really costly with more maintenance time to adjust, more leakage and loss of product, and shorter packing life. This article is going to focus on four key areas during the inserting rings process:
- locating the lantern ring port
- opening the rings without damage
- tamping rings into the stuffing box
- rotating ring cut alignment inside the stuffing box
One common failure mode seen in slurry packed pumps is not locating the lantern ring with the lantern ring port. A lantern ring not properly lined up over the lantern ring port can result in flush water not reaching the stuffing box ID where the solids are to be kept out of the packing rings. Before any rings are installed into the stuffing box, the packing installer should confirm the packing stackup configuration. The best way to locate the port is to disconnect the flush port and stick a welding rod down the port and measure where it enters the stuffing box from the top of the gland. Taking that measurement and with the overall depth and cross section of the stuffing box, a proper stackup can be determined. Once that is confirmed, the next step of inserting the rings can begin.
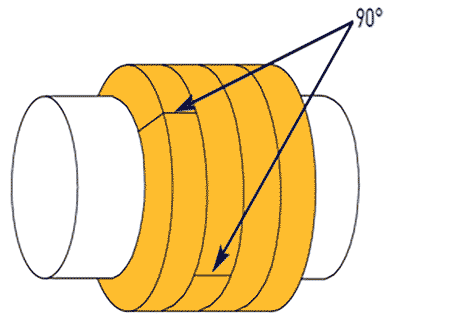
(Images courtesy of Fluid Sealing Association)
Packing rings are a combination of fibers and lubricants in a certain geometry, and it is important that the rings are handled with care. The rings should be separated gently, opened in an “s” shape instead of using a hinge or C-clamp-style opening that can damage or compromise the ring.
Form the ring together around the shaft and push it into the stuffing box so it is completely inside the stuffing box. Next, use the gland nose to push the ring further into the stuffing box. Note that the gland nose bottoms out (becomes flush with the stuffing box) without any resistance. This means the packing ring is not against the bottom of the box. It is important that the ring is tamped into the stuffing box ensuring no gap between it and the bottom of the box. Many tools can be used for this effort including a bushing or tamping tool. Custom-made tamping tools can be created using polyvinyl chloride (PVC) pipe for large applications. Even cardboard can be used to ensure there is no space at the bottom of the box to the bottom of the first ring. Once the first ring is seated correctly, it is important that all remaining rings installed are also tamped using the same method. The last few do not need a tool since the gland will not bottom out and is able to do the job of tamping. When rings are installed without proper seating, it will be hard to get the rings into the stuffing box because of the load needed to compress them. This will also result in rings being over-compressed and squeezing out lubrication that could be used when the pump is running.
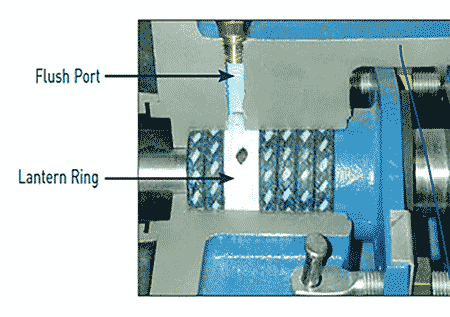
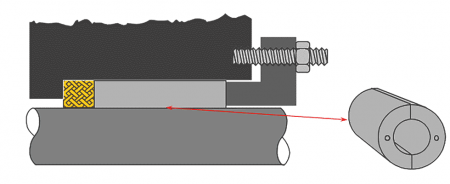
Once the ring is around the stuffing box, make note of where the cut is lined up. It is best to locate the first ring with the cut at the top of the stuffing box (like a clock face, using the 12 o’clock position). The next rings should be put in 90 degrees from the last one (3, 6 and 9 o’clock positions).
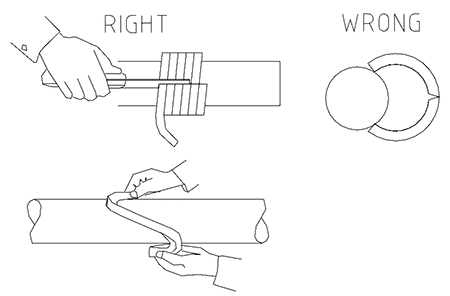
If the rings are installed with the cuts lined up in a row, a straight leakage path will be created. This will result in uncontrollable leakage even after adjustments. If these steps are followed, the packing rings should be inserted correctly, in proper orientation and ready to have a long sealing life.
It is always recommended to review the packing manufacturer installation instructions that will reference storage, handling and maintaining the packing product. Following these steps will also help with troubleshooting failure modes working with packing products because it will educate installers on what to look for if improperly installed. This knowledge will help the user with maintaining a longer life cycle for the packing. Keep in mind that there are new people constantly coming into the industrial maintenance industry, and providing new professionals with this information upfront will allow them to install packing correctly from the start.
We invite your suggestions for article topics as well as questions on sealing issues so we can better respond to the needs of the industry. Please direct your suggestions and questions to sealingsensequestions@fluidsealing.com.