Make your dewatering pump the most effective one
ABEL Pumps
02/28/2018
Consider a common mining application where water flowing into an underground mine is allowed to collect in sumps from which it can be pumped to the surface. This system generally pumps dirty water. There is no consideration here of restricting flow into the mine, so the dirty water needs to be pumped continuously, barring a certain surge capacity in the system of sumps. This approach precludes having dry areas near the bottom of the mine, thus influencing efficiency and mining procedure. Following are five factors to be considered in selecting such a system.
1. Percent Solid of the Fluid to be Dewatered
Ten percent solid is on the high side. Abrasive wear influences maintenance costs of dewatering. As fluid moves through the pump, abrasive wear is proportional to the velocity cubed. This is a consideration in using centrifugal dewatering pumps. Positive displacement pumps allow slurries to travel relatively slowly through the pump.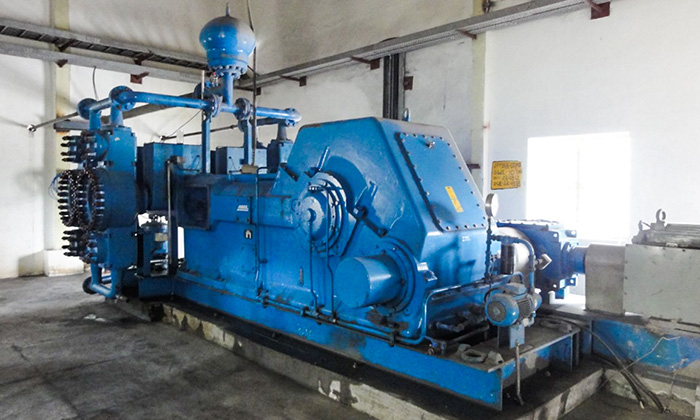